Keys to Biocompatible and Hypoallergenic Manufacturing
With medical implants on the market for nearly every part of the body, working with materials that are both hypoallergenic and biocompatible is essential. Implanting a substance that isn’t biocompatible could be dangerous or even deadly. What are the keys to biocompatible and hypoallergenic manufacturing and how will that change in the future?
The Importance of Biocompatibility
The dictionary defines biocompatibility as “the quality of being compatible with living tissue or a living system by not being toxic or injurious and not causing immunological rejection.” Everything, from pacemaker electrodes to replacement hips and bone screws need to be biocompatible, as they’re implanted in the body.
A lack of biocompatibility can trigger an immune reaction, causing the body to reject the implant. In a worst-case scenario, reacting with naturally occurring chemicals in the body can cause toxic responses. In these cases, additional and sometimes dangerous surgery is necessary to remove the incompatible implant.
Biocompatibility is a blanket term that usually refers to polymers, which can include anything from ceramics and metals to various types of plastics.
Common BIocompatible Materials
There are more than a dozen biocompatible materials that are safe to use in the human body. These materials fall into three categories: metals, polymers, and ceramic biomaterials.
- Biocompatible metals include stainless steel, cobalt-chromium alloys titanium and titanium alloys, as well as precious metals like platinum and palladium.
- Biocompatible polymers include polylactic-co-glycolic acid (PCL), polyLactic Acid, platinum-cured liquid silicon rubber (LSR) for both short and long-term implants and even cellulose, for various applications.
- Biocompatible ceramic biomaterials include alumina, bioglass, hydroxyapatite and zirconia.
This isn’t an exhaustive list by any means, but it does provide a small sample of the different biocompatible materials currently available and approved by the FDA for medical use. It is essential to lab-test each material. Do not assume compatibility simply because it is on a list such as this.
Keys to Biocompatible and Hypoallergenic Manufacturing
Biocompatible material manufacturing has been a challenging field to work in, because of a lack of communication within the industry. The FDA, contrary to popular belief, does not certify individual materials as biocompatible. Instead, it only considers and approves finished products that are ready for testing. That means companies are responsible for testing each material in their device for biocompatibility before they become part of the finished product.
There are two different types of contact companies need to consider when designing a biomedical device: direct and indirect contact. Direct contact defines anything that comes into direct contact with body tissue. Indirect contact is for anything that fluids or gasses pass through before coming into contact with body tissue.
Sustainability is also becoming an important part of biomedical manufacturing, as companies and consumers alike begin seeking out ways to reduce their impact on the environment. In addition to having a beneficial effect on the environment, working toward sustainable manufacturing techniques is an easy way to bring in new customers. The market talks with its wallets, and in recent years, they’ve been content to spend more money with brands that are actively working to protect the environment.
The Future of Biocompatibility
Biocompatibility is already a challenging field to work in, with changing regulations and the need for consistent testing throughout the manufacturing process. Adding sustainability to the mix may serve to make it even harder, but it may also make it easier for manufacturers to create biomedical implants in a more efficient manner moving forward.
Right now, the materials approved for use in biomedical implants are limited, but as new alloys and polymers emerge, the chances are high that many of them will prove to be biocompatible as well. These will help to shape the future of biomedical manufacturing and the medical industry as a whole.
Comments (0)
This post does not have any comments. Be the first to leave a comment below.
Featured Product
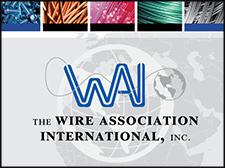