Prerequisites For Establishing A Bulletproof Manufacturing Maintenance Program
Manufacturing companies are continuously developing reliable maintenance strategies in a bid to increase productivity and offset losses arising from unplanned breakdowns. It is evident that technology is playing a vital role as manufacturing facilities transition from reactive and preventive strategies and adopt data driven predictive maintenance programs.
The need to incorporate advanced maintenance programs increases as companies target safe and efficient manufacturing environments. But does a sophisticated maintenance program provide assurances that it will be foolproof?
Whether you are planning to roll out a new maintenance program or optimize an existing strategy, it is essential that the program is profitable, efficient and applicable. Below are some of the fundamental requirements that must be met in order to develop an insurmountable maintenance program to complement your manufacturing activities.
Define all maintenance requirements
Manufacturing plants vary in sizes and layouts with smaller plants having fewer assets. Large scale manufacturing facilities will feature multiple, often complicated but interdependent assets. A detailed survey of assets is useful in creating realistic maintenance objectives against the set production targets. Identifying all maintenance needs for a facility provides a comprehensible scale of anticipated maintenance activities and their impact on production.
Clearly understanding the manufacturing process flow sets a basis for maintenance teams to select and streamline a maintenance program, suggest relevant technologies, plan and assign tasks to maintenance teams and develop long term maintenance goals.
While predictive maintenance programs may prove to be effective for large and complex manufacturing units, it could be economically viable for maintenance teams to adopt preventive maintenance for small scale units.
Prioritize manufacturing assets
Every asset in a manufacturing setup has an important role to play in achieving production targets. Before settling on a maintenance program, it is vital to recognize and rank functional units in the order of their contribution to the manufacturing process. For instance, a boiler will be a highly critical component when compared to an extractor fan in a rubber manufacturing setup.
Key Performance Indicators (KPIs) are then developed and assigned to individual assets based on the criticality rankings. Highly critical assets must be available throughout the production cycle, with slim downtime margins allowed for less critical assets.
Establishing maintenance metrics based on the priority of assets provides an avenue for maintenance teams to continuously monitor the success of a maintenance program against the established targets.
Prioritizing assets based on their contribution to production is inevitable as more than 76% of manufacturing facilities rely on preventive maintenance programs. A bulletproof maintenance program should be capable of dispensing maintenance operations with minimal interference to critical plant equipment.
Determine relevant technology Solutions
Let’s face it, planning for maintenance operations can be tedious. Fatigue resulting from huge workloads could potentially lead to teams overlooking some maintenance activities. Adoption of technology has significantly reduced maintenance bottlenecks, improved the collection of maintenance data and reduced overall maintenance workloads.
A maintenance program that leverages the Computerized Maintenance Management System (CMMS) converts traditional maintenance programs into indomitable and highly efficient systems. A CMMS breaks down and organizes multiple maintenance tasks into small manageable schedules.
The program organizes work orders and provides a collaborative communication platform for maintenance teams. This digital solution makes it simpler for teams to track maintenance trends, create and store multiple maintenance reports, further improving workflows and productivity. Most CMMS programs are developed for easy integration with Enterprise Resource Planning (ERP) and production planning software, which work in collaboration to improve multiple production analytics.
While the internet of things (IoT) and artificial intelligence continue to gain popularity, they have become inevitable tools in the development of foolproof maintenance programs. The shift towards reliability centered predictive maintenance banks heavily on sensor technology. The sensors are used to concurrently collect real time data on the operating conditions of multiple manufacturing assets, continuously tracking the health of the assets. The data is relayed and analysed in real time, providing insights into possible equipment failure. Through these technologies, maintenance teams are able to undertake corrective measures on a wide range of equipment, just before failures occur.
Capacity Building for Maintenance Teams
Buy-in of a maintenance strategy is important for its implementation and by extension its success. Bringing every member on board expedites the implementation process, making it easier to assess the efficiency of a program within the short, medium and long terms. Training and capacity building provides an ample avenue for maintenance teams to be fully acquainted on how to use and implement the new technology. Addition of digital solutions automates the prioritization of work orders, with the reallocation of tasks performed autonomously. All maintenance personnel should understand and be able to utilize the new tools that come with the maintenance program.
Training creates awareness on anticipated role changes in relation to maintenance schedules and how a shift to a selected program affects the allocation of tasks.
Continuously Assess and improve the Maintenance Program
On paper, a maintenance program may be perfect. However, its implementation may not happen as planned as some changes will be rolled out in phases. For a coherent implementation, it is important for maintenance teams to benchmark against set KPIs. Creating a checklist enables the maintenance teams to analyze actual maintenance data against the pre-planned metrics. Maintenance performance data can be in the form of mean time between failures, mean time to repair or frequency of unplanned breakdowns.
With additional data collection tools, maintenance teams are able to analyze progress, pinpointing areas that are slow to implement or those that have negatively impacted production. It is good practice to analyze cost savings brought forth by a maintenance program and its direct impact in increasing productivity.
So, is it wise for you to stop once your maintenance program meets all its objectives? Well, just like manufacturing that relies on Kaizen methods, maintenance programs must be improved continuously. As technology and production improves, new gaps will emerge. A bulletproof maintenance program must provide an allowance for it to be tweaked and retain its competitive advantage and relevance.
Digital solutions must be frequently fine tuned in order to improve data security since the adoption of sensors and IoT technologies increase a manufacturing plant’s vulnerability to security attacks.
Final Thoughts
Selecting an appropriate maintenance program is not a walk in the park. A lot of planning goes into the selection, implementation and continuous improvement of the program. Developing a sturdy maintenance program translates to significant cost savings and improved equipment uptime, increasing the productivity of manufacturing units.
Collective inclusion of maintenance and production teams in planning and implementing a maintenance program immensely contributes to its success. It is imperative that maintenance managers strive for continuous improvement of maintenance programs for them to retain a competitive edge in the ever evolving manufacturing sector.
Talmage Wagstaff.
Co-Founder and CEO of Redlist. Raised in a construction environment, Talmage has been involved in heavy equipment since he was a toddler. He has degrees and extensive experience in civil, mechanical and industrial engineering. Talmage worked for several years as a field engineer with ExxonMobil servicing many of the largest industrial production facilities in the Country.
Comments (0)
This post does not have any comments. Be the first to leave a comment below.
Featured Product
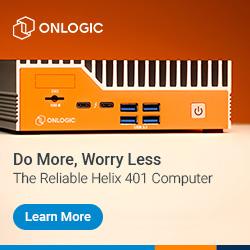