Micro Molding - The Need for Collaboration and DfM
This article examines the ways in which companies looking to achieve significant product miniaturization need to approach their product development process, and how they need to adapt their thinking when embracing micro molding. Making smaller and smaller and often increasingly complex parts and components does not just mean simply scaling down macro processes. In addition, there needs to be a fundamental review of the “way” that a product development process is undertaken, there being a disproportionate need to focus on true collaboration with production partners, and a laser sharp focus on design for manufacture (DfM)
While there are many companies already well versed in the use of micro molding in their product development cycles, there are a larger number that recognize the business need to produce smaller and smaller and often more complex and innovative products and components, but cannot see an obvious route to attain these goals.
There is a general understanding throughout industry that micro molding is not just “macro molding but smaller”. There comes a point when making things smaller that the process to achieve this needs to change, and here the analogy of folding paper is often used. When you fold paper in half, and you have a piece of paper half the size of the original. Fold it again, it is a quarter the size. However, when you get to the 7th fold, it is impossible to achieve, so to reduce the surface area the process (folding) has to change.
This is much the same when looking at molding. There are a certain set of rules and understandings of the molding process at the macro level that simply don’t work at the micro level. The flow of molten plastic, its cooling, warpage, necessary venting and gating etc… are all different when molding at the micro scale, and to a greater or lesser extent the process needs to be relearned.
Most if not all OEMs undertaking micro molding at scale outsource their production, so the “way” that micro molding works, while relevant, should not be seen as a barrier to engagement. In a nutshell, your chosen micro molding expert will take away the need for you to understand the vagaries of the characteristics of thermoplastics when molding small! However, there are a number of other areas that any OEM must begin to focus beyond the micro molding process per se, and these will be analysed in this article.
THE PRODUCT DEVELOPMENT PROCESS
Micro molding is only one part of the overall product development process, and it is important for OEMs to appreciate that various “departments” involved in a micro manufacturing project need to be engaged from product design inception.
Absolutely critical for success is to reassess the nature of the relationship between OEM and molder in a micro molding scenario. When dealing with contract manufacturers on the macro level, the relationship can quite acceptably be that of a job shop. The design is presented, the quote is secured, and the parts are delivered. Job done.
This cannot and will not work when undertaking a micro molding project, which necessitates that the OEM and the chosen micro molding company enter a fully collaborative partnership relationship.
The reasons for this are numerous, but begin with the fact that just as micro molding and the macro molding are completely different processes, the design for manufacture (DfM) rules are also entirely different.
DfM for micro molding is hugely important, and the expert in the room to offer advice and counselling is the expert micro molder, your product development partner. Very often, the less baked an idea is when the micro molder is engaged the better, as the earlier that the design of a micro product can be influenced and adjusted to optimise manufacturing outcomes, the better in terms of cost and timeliness of production.
Essentially, DfM ensures that not only will the end product be fit-for-purpose but that it is also optimised for the production processes that will be used to manufacture it, in this case micro molding and automated assembly. The micro molding team that you work with should be able to advise on such issues as material choice, draft angles and undercuts, part lines, ejector pin locations, gate locations, the likely flow of material in the mold, wall thicknesses etc…
Perhaps the key enabling technology when it comes to micro molding is micro tooling. Tooling in any manufacturing scenario is always the most-costly and time consuming part of the product development process, but when looking at micro molding, the tolerances and complexity that is often required in micro molds make it especially critical.
Micro tooling is an art in itself, and for OEMs it is vital that they work with micro molders that are able to design, build, and maintain molds in house, and also have the expertise and experience to optimise tool fabrication.
One size does not fit all when looking at micro tooling, and it is important that OEMs engage with micro molders that can work alongside them to drill down into the specifics of a particular application, understand the effects of a certain material, cycle time expectations, part criteria, and expected volumes before beginning to cut steel.
In house tool fabrication — in fact vertical integration in general ensuring that design, molding, metrology and validation, and automated micro assembly are all undertaken in the same facility with departments working collaboratively — is vital in a micro manufacturing scenario where tolerances are so tight. The probability for successful outcomes increases exponentially when the responsibility for project and production, timeline, and execution are controlled within a single entity.
It goes without saying that a micro molder should be expert in micro molding, but once again underpinning any success is not just engaging with a company that has the right kit, but ensuring that there is a collaborative relationship that allows total transparency at this stage of the product development process.
Once again, the differences between macro molding and micro molding are stark when it comes to the molding process per se. Every stage of the product development process in a micro manufacturing scenario is driven by an obsession with the attainment of micron and sub-micron tolerances, and when it comes to micro molding it is key that OEMs engage and work alongside a micro molder that has the business acumen and experience necessary, an expert team of engineers, an understanding of the correct manufacturing methodologies, and the tooling and processing expertise to ensure optimised outcomes.
Finally, when dealing with miniaturized plastic parts and components, the assembly part of the product development process must be discussed and considered early in the design cycle, again demanding a collaborative and pragmatic relationship between OEM and micro molder. When dealing with micro scale parts and components, the cost of manual assembly is prohibitive, and often requires levels of preciseness when dealing with sub-micron tolerances that are impossible to achieve. Automated assembly is therefore a must in most micro molding scenarios, requiring that OEMs select a micro molding partner that is able to understand the methodology of micro assembly, and achieve the extreme positional accuracy required.
PARTNERSHIP & COLLABORATION
So far we have looked at how collaboration and transparency are vital at each stage of a micro scale product development process from design, through tooling, molding, and assembly. It is important to understand, however, that this level of collaboration and transparency is not just required between the micro molder and the OEM customer, but also between the different teams within the micro molding facility, which is why working with a truly vertically integrated company is so important.
To a greater or lesser extent, OEMs are relying on the micro molder to be their trusted guide in areas that they themselves are not best equipped to understand or exploit. But it is still a project that belongs to the customer, and it is always the customer that should be central to all conversations and reviews that take place during the product development process.
The outcome, in other words, needs to be something that the OEM customer is fully invested in and satisfied with, not a micro product or component that is fit-for-purpose, easy and inexpensive to mold and assemble, but bears no resemblance to the customer’s vision.
Here, transparency is absolutely vital, ensuring that the OEM customer is always on the same page, understands the decision-making process, and works with the micro molder to problem solve and optimise outcomes while always ultimately being in control.
Internally, all teams involved in the product development process must also work with such clarity and transparency as well as collaboratively. As we have already seen, producing a plastic product with micron or sub-micron features, repeatably, economically, and on time means that the “over the wall” approach has to be abandoned. Success in micro molding requires a true inter-disciplinary approach, as it is only in this way that the ultimate goal — an optimized product made to specification repeatably — can be guaranteed.
Effectively, product development teams working collaboratively from project inception allow for a singular focus on quality assurance, which begins with design for manufacturability reviews to ensure the project sets off on the right foot, and extends all the way through to the development of control plans to assess critical part features, Failure Mode and Effects Analysis (FMEA) results, high-resolution in-line vision systems, and high magnification microscopic measurements to verify tool and finished part dimensions.
SUMMARY
Success in micro molding is predicated on the forging of a truly collaborative and transparent relationship between micro molder and client. Decisions made at the early design stage will have effects when it comes to micro tool fabrication, micro molding, and micro assembly. Because of this — and the need to have an unswerving focus on the achievement of extremely tight tolerances and to validate design intent — all departments involved in the product development process must work together from the inception of a product design to ensure successful outcomes.
Roger Hargens has been involved with Accumold from its beginnings in 1985, and from 2000 has been the company’s CEO and President. The company under Roger’s stewardship has grown to a 130,000 square foot fortified facility designed for assurance of supply, employs over 350 staff, and is a net exporter shipping all over the world every day from its Ankeny, IA, USA facility which runs 24 hours a day, 7 days a week.
Comments (0)
This post does not have any comments. Be the first to leave a comment below.
Featured Product
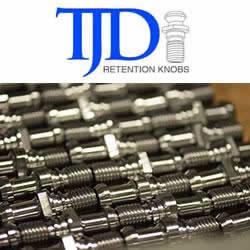