Meltio’s advanced additive manufacturing proving to be an industrial solution in different sectors with real metal printed parts
Meltio’s industrial customers can print and repair parts on demand with consistent, repeatable results, allowing them to optimize material usage, reduce time and costs, and improve overall production efficiency
Linares (Spain), July 16th 2025.- The unique Directed Energy Deposition (DED) metal 3D printing technology developed by Meltio is gaining traction among different industries around the world to solve their manufacturing and repair needs. The additive manufacturing (AM) solutions proposed by Meltio reduce manufacturing costs and time compared to other conventional processes, repair damaged parts and print obsolete components on-demand.
This is demonstrated by the increase in the number of success stories and industrial applications that Meltio has experienced in the automotive, defense, aerospace, mining, oil and gas industries during the first half of 2025.
A demanding sector like the automotive industry is using Meltio's DED technology for the manufacture of metal parts that must withstand high temperatures and stresses.
With over 10.000 km on the road and remaining with the same initial conditions, DMZ's high-performance exhaust header has proven to be a success. Thanks to Meltio's technology, DMZ has been able to create extremely complex geometries for optimizing exhaust flows in the combustion engine and reducing the assembly time from 8 hours to just one, therefore matching Stellantis Group's demands.
Another motorsport part is the one developed by ERM. The turbo intake manifold, printed with the Meltio M600 in dual material, is capable of withstanding temperatures above 800 ºC, while manufacturing costs and time were reduced by 70%, compared to traditional methods.
More companies in the automotive sector like Iveco, using the Meltio Robot Cell solution at the Bourbon-Lancy plant in France to reduce production lead times and enhance flexibility in designing and manufacturing parts; or Hirudi, producing an impressive stub axle with a 62% weight reduction and a 33% faster delivery time and cost reduction, are also enjoying the benefits of using Meltio's technology.
Part obsolescence and supply chain disruptions have become the greatest threats to defense operations. Meltio addresses these challenges and mitigates these issues with autonomous systems capable of printing and repairing on-demand at the point-of-need.
That was the case of the 300mm diffuser that no one could replace, but thanks to Meltio's AM technology, it became not only possible to produce it, but also printed with improved properties. Another example is the redesign of an eductor naval part for the USS Arleigh Burke (US Navy). A part with high wear, difficult to inspect, and long lead times seemed to be impossible. But a redesign and a material change made it easy to replicate a legacy part in less than 58 hours.
A critical component like a close impeller, was another successful task for the Meltio Engine Integration for Robot arms. Made in cast bronze in a corrosive environment wasn't ideal. With some redesign to improve printability and performance plus switching to stainless steel 316L, a stronger part with greater wear resistance was possible.
These are just some examples that show why armed forces like the USA, Spain, France, and Korea, in particular, and the defense sector in general, are heavily relying on Meltio's capabilities.
From mining sites to offshore platforms, Meltio's wire-laser metal 3D printing technology brings unmatched reliability, flexibility, and cost-efficiency to the toughest industrial sectors: Mining, Oil & Gas. Forget about supply chain delays, drastically cut down the costs of custom parts, and reduce the equipment downtime to a minimum.
In that regard, Roez s.r.o., a Czech research and development company, is advancing in energy innovation with a single-print turbine case. Previously, a complex and costly process, but thanks to Meltio's technology, they were capable of printing the part in one step, reducing costs and time with no additional infrastructure.
"We use Meltio's advanced additive manufacturing technology to develop innovative prototypes and specialised parts that drive energy efficiency and green solutions across nuclear, hydro, and chemical industries, supporting our mission for regional leadership and continuous innovation.
Meltio was the only out-of-the-box industrial wire-laser metal AM solution capable of printing multiple materials with a wide variety of options. Powder 3D printing didn't fit our needs, and the Meltio solution was the only standalone wire metal printer that allowed us to successfully produce a complex turbine case with internal structure—all in a single print and just one prototype." - Feedback from ROEZ
In Japan, Daidore Corporation is a manufacturing company with a focus on agile product development and efficient production of industrial components. Faced with mounting pressure to streamline production and shorten development cycles, Daidore began evaluating advanced manufacturing technologies that could improve both productivity and product quality.
After evaluating several additive manufacturing technologies, Daidore selected Meltio's wire-laser metal deposition technology, specifically the Meltio Robot Cell, due to its unique combination of affordability, flexibility, and scalability.
"Metal Additive Manufacturing is growing in demand among the global industrial sector. It solves the needs of these customers to obtain parts and repair them, effectively and reliably, and guarantees them greater autonomy since Meltio's equipment is installed directly in their workshops and production lines. And this translates into an increase in real success stories during the first half of 2025. We bring reliability and credibility with our disruptive technology and this encourages us to continue to grow and innovate our solutions in the next six months of 2025," explained Lukas Hoppe, Head of R&D at Meltio.
"The need for AM has never been greater and we understand those industrial customer needs and we are clear to demonstrate to them the clear advantages of integrating Meltio wire-laser metal 3D printing solutions into the manufacturing floor and the machine shops to lower costs, increase efficiency and overcome challenges such as supply chain stability."
Same applies to DPR Automatismos, Spanish industrial integrator, that is choosing Meltio for creating metal parts because of their versatility and ability to integrate with robotic systems. Laser metal deposition technology offers excellent value for money, material flexibility and the ability to create complex parts with high precision.
Among many other examples, companies such as Gary Mécanique in France and ALAR (Mexico) for aerospace and the Tecnológico de Monterrey have already adopted Meltio's technology.
Please, see here all the Meltio real use cases for industries:
https://meltio3d.com/resources/
Global industrial recognition: Meltio M600 dazzles at the 3D Printing Awards
The Meltio M600 metal 3D printer has been honored at the 3D Printing Awards 2024 as "Enterprise 3D Printer of the Year (Metals)", thanks to its innovative design and reliability. Its ability to work with materials such as copper, aluminum, stainless steels, titanium, Inconel and nickel has revolutionized production lines in sectors such as automotive, aerospace, mining and petroleum. The Meltio M600 metal 3D printer has amazed the international industrial sector and the 3D Printing Awards 2024 jury with its design and reliability for the creation of metal parts with different materials.
About Meltio
Meltio takes metal additive manufacturing to the next level by developing and manufacturing high-performance, affordable and easy-to-use metal 3D printing solutions using wire laser metal deposition (LMD) technology - a business segment within DED energy direct material deposition technology. The company's mission is to delight worldwide industrial customers, partners and employees by pioneering the development of affordable and reliable metal 3D printing systems. Meltio is revolutionizing the way metal parts are manufactured and repaired by achieving highly reliable results and extraordinarily dense parts with our additive manufacturing technology. Meltio's offerings include the new Meltio M600 industrial metal 3D printer, the new Meltio Engine Blue and the second generation of Blue Laser solutions: the Meltio Engine Blue Integration kit for CNC machines, which turns virtually any computerized machine and CNC milling machine into a powerful hybrid manufacturing center, and the new Meltio Engine Blue integration kit for robotic arms. And the Meltio Robot Cell, an affordable turnkey containerized solution for Meltio Engine Robot Integration. www.meltio3d.com
Featured Product
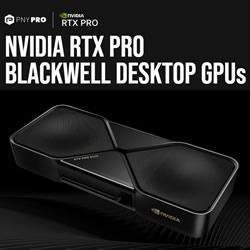