Let’s explore the role of HMIs in modern manufacturing, their impact on process improvement, and the specific solutions offered by KEB America.
How Human-Machine Interfaces (HMIs) Empower Smarter Manufacturing
Article from | KEB America
Human-Machine Interfaces (HMIs) have become a cornerstone of modern industrial automation, bridging the gap between people and machines. Their primary purpose is to give users more control through real-time system monitoring and valuable insights.
The result is increased productivity and accuracy, which directly improves profitability. This has led to widespread adoption across the automotive, packaging, plastics, and energy industries.
Let’s explore the role of HMIs in modern manufacturing, their impact on process improvement, and the specific solutions offered by KEB America.
KEB’s panel HMIs offer robust industrial displays with versatile communication and control.
What is an Industrial HMI?
An industrial HMI is an interface that connects human operators with machinery and production systems. It includes hardware (e.g., touchscreens, panels) and software designed to provide real-time visualization, control, and interaction with complex automated processes.
HMIs serve three core functions that we can group into three distinct areas:
- Visualization of Processes: HMIs provide a graphical representation of machine states, production data, and system diagnostics. This gives engineers instant insights into operations.
- Data Integration: Modern HMIs communicate with PLCs (Programmable Logic Controllers), sensors, and enterprise systems. This consolidates diverse data streams into one platform.
- Control and Automation: Operators can adjust parameters, set commands, and troubleshoot issues directly, reducing reliance on manual intervention.
Rather than viewing an HMI simply as a dashboard interface, consider its essential role in maximizing system performance, minimizing downtime, and ensuring safety.
KEB HMIs are designed to work with various PLC brands.
How HMIs Are Revolutionizing Manufacturing
Data-centric processes increasingly drive industrial manufacturing, and HMIs are at the forefront of this shift. These systems fundamentally reshape how facilities operate, offering unprecedented levels of intelligence, efficiency, and agility. This is taking place in a few key areas.
1. Smarter Processes Through Real-Time Data
Modern HMIs integrate with IoT devices, sensors, and advanced automation systems to create an interconnected manufacturing ecosystem. By enabling operators to visualize and act on real-time data, HMIs influence every stage of production:
- Data Consolidation and Visualization: HMIs gather operational data from PLCs, SCADA systems, and field devices, presenting it through intuitive dashboards in KEB’s X1 HMIs. This ensures operators have the tools to monitor processes efficiently and make data-based adjustments in real time.
- Predictive Maintenance: Using integrated analytics, tools like the COMBIVIS Studio HMI anticipate equipment wear and tear. These features help prevent costly downtime and optimize production schedules.
- Remote Monitoring and Control: Engineers can access HMI systems via cloud-based platforms, enabling control from remote locations. This flexibility is particularly valuable for distributed systems like energy grids or multi-site manufacturing.
KEB’s X1 HMIs come in four sizes and feature capacitive multi-touch screens.
2. Efficiency Gains Through Automation
HMIs make industrial production more efficient by automating routine tasks and providing valuable system insights. This leads to improved throughput.
- Streamlining Machine-to-Machine (M2M) Communication: Protocols such as EtherCAT and OPC UA enable HMIs to act as central hubs for automated workflows that coordinate activities across multiple machines.
- Advanced Alarm Systems: HMIs deliver precise alarm notifications with contextual data, allowing engineers to respond promptly and effectively to emerging issues. For example, an HMI might highlight a temperature spike in a plastic extrusion machine and suggest corrective actions directly on-screen.
- Reduced Human Error: HMIs use automated configurations and workflows to require fewer manual adjustments by human operators. This also leads to greater consistency and accuracy.
3. Empowering Decision-Making Through Insights
The advanced data-processing capabilities of HMIs empower engineers and managers to make informed decisions rapidly. By leveraging the wealth of information provided, manufacturers can:
- Optimize Resource Allocation: Detailed insights into production metrics help identify bottlenecks and streamline resource distribution. For example, HMIs can analyze performance variations across turbines in wind turbine operations to prioritize maintenance schedules efficiently.
- Dynamic Process Adjustments: HMIs enable operators to adapt production parameters dynamically during high-demand periods. This means more timely deliveries without compromising quality.
- Energy Optimization: By analyzing power consumption patterns, HMIs help facilities reduce energy waste and lower operating costs, aligning with sustainability goals.
In essence, HMIs serve as the operational brains of modern manufacturing. They drive more intelligent processes, enhance efficiency, and encourage data-driven decision-making at every level.
KEB X1 HMIs come with flexible mounting options.
Why KEB America’s HMIs Stand Out
KEB America engineers Human-Machine Interfaces to meet the demands of modern industrial automation. Combining advanced technological features with unparalleled durability, these HMIs offer solutions that address current challenges and future needs in manufacturing.
1. Advanced Visualization and Control
KEB’s HMIs are equipped with high-resolution, capacitive touchscreens. These offer precision and responsiveness, even in environments where operators wear gloves. Multi-layered visualization capabilities include:
- Real-Time Data Displays: Dynamic charts, live production metrics, and diagnostic tools give operators a comprehensive view of system performance at all times.
- Customizable Dashboards: Engineers can customize HMI layouts to suit specific processes. This allows immediate access to critical controls and data without unnecessary clutter.
- Multi-Language Support: Multilingual options make HMIs usable across diverse workforces and organizations – synchronizing global operations.
2. Seamless Integration and Compatibility
One of KEB’s defining strengths lies in its commitment to interoperability:
- Wide Protocol Support: Full compatibility with industrial communication standards like EtherCAT, Modbus TCP/IP, OPC UA, and CANopen makes it easy to integrate an HMI into existing automation infrastructures.
- Edge and Cloud Connectivity: HMIs enable secure data exchange directly between edge devices and cloud platforms. This result is advanced analytics and remote system monitoring.
- PLC Interfacing: KEB HMIs work seamlessly with PLCs from leading manufacturers, streamlining implementation across multi-vendor setups.
By incorporating Industry 4.0 and IoT readiness into the core architecture, KEB’s HMIs are built to adapt to evolving technological landscapes. This keeps manufacturers ahead of industry changes.
KEB offers custom firmware development that can be customized to operational requirements. This further streamlines integration and more profound process optimization.
Power-over-Ethernet connection ensures IP67 protection.
3. Industrial-Grade Design
Designed for rugged industrial environments, KEB’s HMIs are known for their durable build quality:
- High Environmental Ratings: IP67-rated enclosures protect against dust, water, and extreme temperatures, making them suitable for demanding applications. In addition, Power-over-Ethernet (PoE) combines power and data transfers over a single cable – ensuring IP67 protection.
- Long Lifecycle Components: High-quality capacitors, processors, and displays ensure reliability and minimal maintenance over prolonged use.
- Mounting Versatility: Options for panel, VESA, or standalone installations provide flexibility during deployment. The X1 HMIs are compatible with wall, gooseneck, and tube mountings.
KEB prioritizes energy-efficient design and hardware. HMIs consume minimal power without compromising performance, satisfying green manufacturing initiatives.
4. Enhanced Usability Features
KEB’s focus on operator experience translates into HMIs that are as intuitive as they are powerful:
- Smart Alarm Systems: Contextual alerts and troubleshooting guides help engineers resolve issues efficiently without disrupting operations.
- Remote Access Tools: Using secure protocols, operators can monitor and control systems from smartphones, tablets, or PCs. This significantly reduces on-site intervention.
- Intelligent Diagnostics: Built-in tools analyze operational data to recommend performance optimizations and flag potential failures before they occur.
Practical Applications of HMIs in Manufacturing
Human-Machine Interfaces revolutionize manufacturing by offering tailored solutions across various industrial sectors.
1. Automotive Industry
The automotive sector demands precision and streamlined operations, and HMIs deliver on that.
- Robotic Assembly Control: KEB’s C6 X1 HMIs enable seamless coordination of robotic arms on assembly lines. These high-resolution panels ensure precise operations and reduce assembly errors.
- Real-Time Diagnostics: The COMBIVIS Studio HMI provides detailed logs and diagnostics, allowing operators to address faults immediately and minimize halts in production.
- Quality Assurance: Automated inspection systems connected to HMIs detect defects during assembly and trigger corrective workflows, maintaining product consistency.
2. Packaging Industry
In packaging, agility, and adaptability are key to handling diverse product requirements:
- Dynamic Label Management: HMIs allow operators to modify label designs and configurations in real-time, reducing delays during production changes. KEB’s HELIO HMI Software provides customizable interfaces, enabling operators to swiftly adjust label designs and configurations to meet diverse packaging requirements.
- Material Handling Optimization: The C6 HMI LC combines HMI and PLC functionalities, streamlining material handling processes through integrated control and visualization. By tracking material flow, the HMI prevents jams and ensures smooth operations along conveyor systems.
3. Plastics Industry
Precision in plastics manufacturing, such as injection molding, is crucial for maintaining product quality:
- Injection Molding Precision: HMIs with granular accuracy monitor parameters like temperature, pressure, and cycle times. KEB’s C6 X1 HMI or C6 S14 IPC are powerful machine controller for plastics manufacturers. Operators can monitor temperature stability and prevent material defects during injection molding.
- Process Visualization: By presenting real-time visuals of the molding process, HMIs help engineers detect inefficiencies and optimize production speeds.
4. Energy Sector
The energy sector benefits from HMIs by enabling efficient management of decentralized systems:
- Grid Monitoring: HMIs oversee renewable energy sources such as wind turbines and solar arrays. The C6 HMI Panels and X1 HMIs facilitate effective monitoring of renewable energy sources, providing operators with real-time data to optimize energy output.
- Predictive Maintenance: Utilizing COMBIVIS Connect, operators can perform remote diagnostics and maintenance, predicting and preventing equipment failures before they occur.
HELIO features rapid prototyping that empowers you to customize industrial HMIs using real time machine data.
5. General Industrial Applications
Beyond industry-specific use cases, HMIs provide universal benefits across manufacturing:
- Real-Time Feedback Loops: Operators can adjust machine settings dynamically, reacting to production demands more quickly.
- Remote Access Capabilities: Engineers can monitor and control facilities remotely through KEB’s X1 HMIs, equipped HELIO or a third-party software, enabling secure offsite commissioning and support. This capability is especially valuable for global operations with geographically dispersed sites, as it reduces the need for on-site interventions.
The Future of HMIs in Manufacturing
As industries adopt Industry 4.0 principles and IoT-driven automation, Human-Machine Interfaces (HMIs) are evolving into highly intelligent tools. Below are key trends shaping the future:
- IoT Integration: Expanded connectivity will consolidate data from sensors and edge devices into unified, cloud-accessible HMIs. Enhanced analytics will allow real-time detection of inefficiencies and dynamic optimization of the factory floor.
- AI-Powered Interfaces: HMIs enhanced with machine learning can predict equipment failures, optimize process parameters on the fly, and provide operators with advanced decision support.
- Augmented and Virtual Reality: AR/VR technologies will offer immersive troubleshooting and training experiences. For instance, an operator wearing AR glasses could see real-time diagnostic overlays on physical equipment.
- Cybersecurity Enhancements: Stronger encryption and anomaly detection will guard against security breaches as HMIs become more interconnected.
By incorporating these advancements, HMIs are meeting the demands of today and paving the way for a smarter, more resilient future in manufacturing. Following these trends, KEB’s HMIs are designed as future-ready solutions that are easily scalable to meet new Industry 4.0 standards and integrate seamlessly with expanding IoT ecosystems.
Industrial HMIs lead to smarter, more efficient, and agile manufacturing. By connecting operators to machines, HMIs empower industries to optimize processes, reduce costs, and stay competitive in a market that is always changing.
With cutting-edge features and proven reliability, KEB America’s HMIs are ideal for manufacturers looking for advanced solutions customized to their needs. Explore the possibilities with KEB America to revolutionize your manufacturing processes.
The content & opinions in this article are the author’s and do not necessarily represent the views of ManufacturingTomorrow
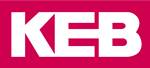
KEB America, Inc.
KEB America is a trusted manufacturer of industrial automation products in North America. We manufacture, assemble, and support our German-engineered suite of controls, drives, motors, brakes, and clutches at an ISO 9001:2015 certified, 150,000-square-foot facility in Shakopee, Minnesota.
Other Articles
Master-Follower Configuration: Precision Control with Encoder-Based VFD Synchronization
Liquid-cooling VFD Increases Efficiency and Savings in Plastics Machinery
More about KEB America, Inc.
Comments (0)
This post does not have any comments. Be the first to leave a comment below.
Featured Product
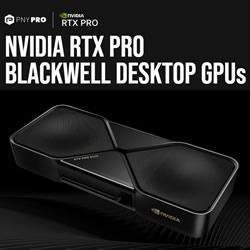