Milling vs. Turning: The Differences in CNC Machining
In CNC machining, CNC milling and CNC turning are two common cutting processes, they are significantly different in terms of working principle, cutting method, application and workpiece shape.
CNC turning: CNC turning technology allows high precision machining which is suitable for making cylindrical parts. One of the greatest advantages of CNC turning technology is the realization of high-precision machining and high-efficiency production, which is particularly suitable for multi-axis lathes to carry out multiple processes at the same time.
Features of CNC Milling
1.Production Capacity
The productivity of CNC milling is best suited for batch processing. In short, CNC milling equips companies that produce small batches of parts in a single run.
2.Material Consumption
CNC milling machines are designed to save and minimize material use. CNC milling has significantly lower material consumption compared to CNC turning. In the long run, this directly translates into lower material costs and better waste management for the Health Safety Environment department.
3.Cutting Tools
CNC milling doesn't necessarily require the use of well-defined tools. You can use a completely different set of cutting tools for a variety of operations. This is not only better than a lathe, but it makes them more efficient.
4.Product Specification
CNC milling can produce a wide variety of parts. It can handle both complex shaped parts and simple parts. Various parts can be manufactured using milling, for example fittings and gears, pumps, engine parts, surgical instruments and implants, etc.
Features of CNC Turning
1.Production Speed
CNC turning is faster for boring, drilling and forming operations. This allows manufacturers to meet deadlines and increase productivity on the go.
2.Accuracy
CNC turning is more accurate, allowing operations to be completed with precise machining. As a result, it is trusted for many important parts with round surfaces, such as rollers, bullets, gears and drills.
3.Adaptability
CNC turning is adaptable and can be interconnected with CNC milling to meet industrial requirements. It can also produce parts for other mechanical components from bolts and nuts to torque and turbines. However, backward compatibility and asymmetric design are critical to the beneficial effects of this interconnect.
4.Product Shape
It is very difficult to produce parts with circular designs using CNC milling processes while CNC turning handles these tasks perfectly. As a result, it can be used to manufacture some of the most important parts in industry like nozzles, nuts and bolts, pipes, ball joints, rollers and circular turbines, etc.
In summary, CNC milling is suitable for workpieces that require complex shapes and features, while CNC turning is more suitable for making cylindrical parts. The choice of which process to use depends on the shape of the workpiece, its requirements, machining process and production needs. Nonetheless, it can also use the two processes in sequence, as there may be applications that require two operational processes.
Featured Product
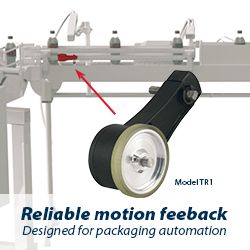
Model TR1 Tru-Trac
The Model TR1 Tru-Trac® linear measurement solution is a versatile option for tracking velocity, position, or distance over a wide variety of surfaces. An integrated encoder, measuring wheel, and spring-loaded torsion arm in one, compact unit, the Model TR1 is easy to install. The spring-loaded torsion arm offers adjustable torsion load, allowing the Model TR1 to be mounted in almost any orientation - even upside-down. The threaded shaft on the pivot axis is field reversible, providing mounting access from either side. With operating speeds up to 3000 feet per minute, a wide variety of configuration options - including multiple wheel material options - and a housing made from a durable, conductive composite material that minimizes static buildup, the Model TR1 Tru-Trac® is the ideal solution for countless applications.