Innovating the New Manufacturing: APSX-PIM and Nexa3D Join Forces to Propel Freeform Injection Molding (FIM) to New Heights
FIM represents a paradigm shift in product development, allowing for the creation of complex geometries and intricate designs that were previously unattainable through traditional manufacturing methods.
In a recent collaboration, APSX-PIM and Nexa3D have united their cutting-edge technologies to pioneer a new era in manufacturing. Their partnership brings forth a seamless integration of the APSX-PIM desktop injection molding machine with Nexa3D's innovative 3D printers, culminating in the ultimate solution for Freeform Injection Molding (FIM). This dynamic synergy between precision injection molding and rapid 3D printing opens doors to unprecedented possibilities in product design, prototyping, and production. FIM represents a paradigm shift in product development, allowing for the creation of complex geometries and intricate designs that were previously unattainable through traditional manufacturing methods.
The APSX-PIM, renowned for its compact footprint and user-friendly interface, empowers businesses of all sizes to engage in injection molding with ease. Now, with the integration of Nexa3D's advanced 3D printing capabilities, the APSX-PIM transcends conventional boundaries, offering a comprehensive desktop FIM package that revolutionizes manufacturing workflows.
By harnessing the precision and speed of Nexa3D's printers, coupled with the versatility of the APSX-PIM, manufacturers can accelerate their innovation cycles and bring concepts to reality within a day. With the APSX-PIM and Nexa3D collaboration, users can seamlessly transition from 3D printing prototypes to injection molded production parts, all within a single, integrated ecosystem. This streamlined approach eliminates the need for costly and time-consuming tooling processes, reducing lead times and maximizing productivity.
The benefits of FIM extend beyond prototyping, offering tangible advantages in various industries, including automotive, aerospace, consumer goods, and beyond. Whether it's rapid iteration during the design phase or on-demand production of end-use parts, the APSX-PIM and Nexa3D partnership empowers businesses to stay ahead in today's competitive market landscape.
Step-by-Step Guide: Making Parts with Nexa3D XiP and APSX-PIM
Design: Begin the process by creating a 3D model of the desired part using CAD software. Leverage the freedom of design afforded by FIM to explore intricate geometries and complex structures.
3D Printing with Nexa3D XiP: Once the design is finalized, transfer the model to the Nexa3D XiP printer. Utilizing state-of-the-art technology, the XiP printer swiftly transforms digital designs into high-resolution 3D printed prototypes with unparalleled speed and accuracy.
Validation and Iteration: Evaluate the printed prototype to ensure that it meets design specifications. With the rapid turnaround time of Nexa3D's printers, iterate quickly to refine the design and address any potential issues.
Mold Creation: Once the prototype is approved, proceed to create the mold using the nexa3D mold generator software or another CAD software. 3D print the mold by using the xMOLD material on the nexa3D XiP printer.
Injection Molding: With the mold in place, initiate the injection molding process using the APSX-PIM. The machine's precise control and repeatability ensure consistent results, delivering high-quality parts with each cycle.
Final Inspection: Conduct a thorough inspection of the molded parts to verify dimensional accuracy and to test the part functionality. Fine tune your design until you hit your targets. With FIM, achieve tight tolerances and superior surface finishes, meeting the most demanding specifications.
Production Scaling: With the optimized workflow enabled by the APSX-PIM and Nexa3D collaboration, seamlessly scale production to meet demand while maintaining the highest standards of quality and efficiency.
To showcase the transformative potential of FIM, APSX-PIM has released an insightful blog post delving into the capabilities and applications of this groundbreaking technology. To witness the transformative capabilities of FIM in action, check out the captivating YouTube video showcasing the collaboration between APSX-PIM and Nexa3D. Additionally, stay updated on the latest developments and insights by following APSX-PIM on LinkedIn, where industry news and updates are shared regularly.
The APSX-PIM and Nexa3D collaboration represents a bold step forward in the realm of additive manufacturing, propelling Freeform Injection Molding to new heights of innovation and efficiency. As businesses worldwide seek to optimize their manufacturing processes and stay ahead of the curve, this partnership offers a compelling solution that promises to reshape the industry landscape for years to come.
Featured Product
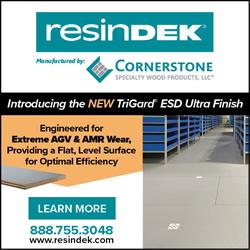