Enhancing Manufacturing with Product Traceability Systems
Product traceability systems allows you to track your supply movements from end-to-end, meaning you can track products to where they were packed, or back through their functional way.
In this Article, we are going to look into traceability in manufacturing, why it's important, the benefits, and how you can apply it.
What's Product Traceability Systems in Manufacturing?
Traceability is the procedure of tracking (and establishing) all your raw resources, parts, and finished goods throughout your manufacturing process. The term itself is joined together from "Trace" and "Capability" and is used to describe the capability to track products by all manufacturing sector, but is most frequently used in sector dealing with perishable goods, like cosmetics or food supply.
Having a product traceability systems program for manufacturing in place will allow you to find literal information on a product, such as:
- Suppliers
- Products
- Examination notes
- Manufacturing details
- Time spent at each workstation
- Distributors
There Are Two Perspectives When It Comes to Product Traceability:
Chain Traceability
This is forward and backward product traceability. Meaning manufacturers are able to track products ranging from raw resources to the end user.
As well as the consumers or distributors can understand where the item is coming from.
Internal Traceability
Product traceability with a limited area, for instance, as covering one specific part of the supply chain. For illustration, if you use outsource manufacturing, the information you admit about their factors is an internal traceability program.
Why is Product Traceability Systems in Manufacturing Important to Apply?
It surely feels like exciting times when the hard work has paid off, and you notice your business are growing, and the number of items you are currently manufacturing, that is expanding too. However, it only takes one batch of defective products to enter the market to:
- Driveaway clients
- Damage your brand
- Hurt your bottom line
- Undo all your hard work
If, it's going to be insolvable to effectively recall a imperfect or polluted item, If you do not have a system in place to track products. That's why having systems in place to ameliorate product traceability is essential.
Not just for products that have a short shelf life but for products that will come outdated due to technological advancements. You might suppose that you do not need a traceability program since you do not vend perishable goods. But, it'll help you ameliorate product effectiveness and product quality control, as you 'll have real- time visibility to understand where problems arise, for example, as bottlenecks in manufacturing.
Now you know what product traceability in manufacturing is and what can be if you do not apply it. However, what are the advantages of product traceability systems in the manufacturing industry?
How to Track Production in Manufacturing?
Product traceability systems in manufacturing involves covering the process of creating goods from start to finish, including the raw resources used, work-in-progress (WIP), and finished goods. There are several manufacturing traceability styles and tools that can be used to track product in manufacturing, but some of the most popular are:
Production Planning and Control
This involves creating a manufacturing plan outlining the product schedule, resources demanded, and the sequence of operations needed to produce the product. Having a strategic plan will help you in allowing you to track progress and determine any delays or issues that may arise in the future.
Manufacturing System
The product traceability systems for manufacturing tracks product in real time, furnishing a detailed view of the manufacturing process, from raw resources to finished products. This system can track product criteria for example, as:
- Cycle time
- Downtime
- Machine application
Barcode and RFID Systems
Barcoding and RFID systems are used to track and trace solutions for products manufacturing process. These systems can identify each item and its position, allowing for real-time supply operation and product traceability.
Kanban System
The Kanban system is a visual system that uses cards or other visual cues to gesture when resources need to be replenished or when a particular task needs to be completed. Manufacturing traceability results like this can help to reduce lead times and increase product effectiveness.
Lean Manufacturing Principles
Lean principles involve streamlining product processes to exclude waste and increase effectiveness. You can optimize the product process and track progress more effectively by relating and barring backups.
By enforcing these styles and tools, manufacturers can track product more totally and efficiently, leading to increased productivity and profitability.
Benefits of Traceability in Manufacturing
Let us discuss some of the advantages of using the product traceability systems in your business.
Root Cause Analysis
Having your product data from end-to-end implies you can execute an in-depth analysis of your manufacturing routes to observe the root cause of any issue. This will enable you to see in which areas of your product are underperforming and help you make changes to ameliorate your manufacturing lead time. For illustration, if some finished products have faults, you will have an overview of your entire product line so you can pinpoint where the faults are present, such as:
- The items that missed a specific process, for example, a quality check
- A new team member is making miscalculations and needs to be trained
- A defective tool or machine needs repairing
Constant Enhancement
Moving on from the root cause analysis leverage of using product traceability, you can also adopt constant enhancement into your item inflow system. A constant enhancement system is basically a form of lean manufacturing. Yet, the biggest difference is that with constant, you and your team members will take responsibility for relating inefficiencies on the shop floor, developing plans, and enforcing advancements for future product runs.
Cloud manufacturing software will be a crucial tool for aiding you in gathering accurate and real time data on your manufacturing, so you can execute regular checkups on your functions for making sure that your item is always running easily. Constant enhancement in manufacturing is perfect for those looking to:
- Eliminate waste
- Implement green manufacturing into their business
Value Stream Mapping
Value stream mapping, also known as material and information inflow mapping, is a lean operation system for helping you understand your manufacturing process and how to redesign it to get the most value from manufacturing. The value stream chart is a traceability system that helps you in covering your:
- Operation steps
- The amounts of raw materials demanded
- The time the product spends at each workstation
Since product traceability in manufacturing observers how your products move through your shop floor, it lends itself well to designing your value stream mapping. Doing this will help you get a fine picture of your operations and more of an idea of what could be bettered on your product lines.
Conclusion
Product traceability in manufacturing is tracking and covering product's journey from raw accoutrements to end-users. It ensures quality, safety, and compliance with regulations. enforcing traceability requires incorporating unique identifiers like barcodes or RFID markers and data capture and operation systems.
Aeologic Technologies offers acclimatized traceability solutions to streamline these processes, enabling real-time visibility, reducing pitfalls, and enhancing functional effectiveness. Embrace Aeologic Technologies expertise to strengthen your manufacturing operations with flawless product traceability and gain a competitive advantage in the market. Take the first step towards a more transparent and optimized manufacturing process with Aeologic Technologies cutting- edge solutions!
Featured Product
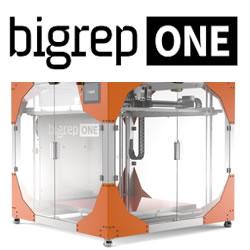
BigRep ONE: Large-Scale 3D Printing
The BigRep ONE is an award-winning, large-format 3D printer at an accessible price point. With over 350 systems installed worldwide, it's a trusted solution for prototyping and production by designers, innovators, and manufacturers alike. Featuring a massive one-cubic-meter build volume, the fast and reliable ONE brings your designs to life in full scale.