Desktop Metal and Schaeffler to Collaborate on Additive Manufacturing of Multi-Material Powders, including Metals and Ceramics
-Schaeffler has acquired Desktop Metal’s Belgium-based Aerosint and will integrate its multi-material Selective Powder Deposition technology for use with Schaeffler’s laser-based multi-material AM system -Desktop Metal will continue to work with Schaeffler on developing the technology for binder jet 3D printing, where Desktop Metal retains an option for commercial use
Desktop Metal, Inc. (NYSE: DM), a global leader in Additive Manufacturing 2.0 technologies for mass production of metal, ceramic, polymer, and health products, today announced that it is collaborating with Schaeffler AG, the German motion technology company, on additive manufacturing of multi-material powders, including metal and ceramics.
Terms of the agreement were not disclosed.
"Schaeffler is one of the leading global manufacturers of components and systems as well as bearing solutions. The motion technology company has a longstanding excellence in precision mechanical engineering and an innovative mindset open to integrate new production processes like metal multi-material printing. We're excited to collaborate with the experienced team on next-generation multi-material additive manufacturing," said Ric Fulop, Founder and CEO of Desktop Metal. "Aerosint's Selective Powder Deposition (SPD) technology has demonstrated spectacular potential for laser applications, and we both agree that Schaeffler has a nearer-term roadmap for commercializing it with laser-based systems than our binder jetting technology. We will retain an option to commercialize the technology with our systems in the future, and we look forward to developing this roadmap together."
The startup will be renamed "Schaeffler Aerosint SA" and integrated into the Schaeffler Group as an additional location for Schaeffler Special Machinery, the Schaeffler Group's special machine construction unit. Andreas Schick, Chief Operating Officer at Schaeffler AG, commented on the deal: "The expertise of Schaeffler Aerosint, combined with our high level of industrialization competence and decades of know-how in innovative production technologies, will give us a distinctive market advantage."
In addition, Schaeffler will continue its collaboration with Desktop Metal in multi-material solutions, including in the area of toolless manufacturing technologies. "By integrating this key future technology, Schaeffler Special Machinery, as a partner for production excellence, will be able to offer its customers a more diversified portfolio of systems, particularly for the manufacturing and medical technology sectors," said Bernd Wollenick, Senior Vice President Schaeffler Special Machinery.
About Desktop Metal
Desktop Metal (NYSE:DM) is driving Additive Manufacturing 2.0, a new era of on-demand, digital mass production of industrial, medical, and consumer products. Our innovative 3D printers, materials, and software deliver the speed, cost, and part quality required for this transformation. We're the original inventors and world leaders of the 3D printing methods we believe will empower this shift, binder jetting and digital light processing. Today, our systems print metal, polymer, sand and other ceramics, as well as foam and recycled wood. Manufacturers use our technology worldwide to save time and money, reduce waste, increase flexibility, and produce designs that solve the world's toughest problems and enable once-impossible innovations. Learn more about Desktop Metal and our #TeamDM brands at www.desktopmetal.com.
Featured Product
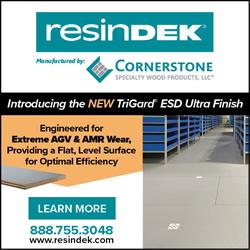