CRP Technology launches on the Additive Manufacturing market Windform TPU, new rubber-like material for SLS process
It's a versatile thermoplastic polyurethane, extremely elastic, flexible, soft thanks to its elongation at break value > 400%. It is suitable for many industrial sectors and applications.
CRP Technology launches on the AM market a new material of the TOP-LINE range for industrial 3D printing service, the rubber-like Windform TPU.
Windform TPU is a thermoplastic polyurethane, white coloured, extremely elastic, flexible, resistant to impact and soft thanks to its elongation at break > 400%.
Franco Cevolini, CEO and Technical Director of CRP Technology: "With Windform TPU, the number of rubber-like materials of the Windform TOP-LINE range, rises to two. We can satisfy many more customers' needs, as they are two rubber-like SLS materials with different characteristics: Windform RL - the first of the Windform range - is a TPE, and it is more rigid, whereas Windform TPU is a thermoplastic polyurethane and it is softer, more flexible."
There are many industrial sectors that can benefit from the use of Windform TPU thanks to its versatility, from transport to robotics, from design to footwear, sports equipment and fashion accessories.
Windform TPU is suitable for manufacturing, for example but not limited to, automotive interior components, gimbal bellows, air cleaner covers, hoses, grips, connectors, joints, snap fits. And again: components for the sport sector, from the sports protections to the running shoes outsoles thanks to its high abrasion resistance.
Windform TPU is also suitable for parts to be used at low temperatures, or that have to be immersed in oils or greases or solvents.
With Windform TPU, the total number of Windform TOP-LINE materials for professional 3D printing (that is Selective Laser Sintering) rises to eleven.
Featured Product
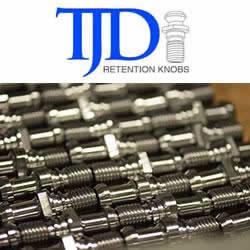
T.J. Davies' Retention Knobs
Our retention knobs are manufactured above international standards or to machine builder specifications. Retention knobs are manufactured utilizing AMS-6274/AISI-8620 alloy steel drawn in the United States. Threads are single-pointed on our lathes while manufacturing all other retention knob features to ensure high concentricity. Our process ensures that our threads are balanced (lead in/lead out at 180 degrees.) Each retention knob is carburized (hardened) to 58-62HRC, and case depth is .020-.030. Core hardness 40HRC. Each retention knob is coated utilizing a hot black oxide coating to military specifications. Our retention knobs are 100% covered in black oxide to prevent rust. All retention knob surfaces (not just mating surfaces) have a precision finish of 32 RMA micro or better: ISO grade 6N. Each retention knob is magnetic particle tested and tested at 2.5 times the pulling force of the drawbar. Certifications are maintained for each step in the manufacturing process for traceability.