Emerson’s Control System Update Helps Optimize Operations with Enhanced Flexibility and Connectivity
DeltaV distributed control system update features new PK Controller functionality for advanced physical layer and consumption-based deployments
Global technology and software leader Emerson is building upon the innovative technologies and solutions in the DeltaV™ distributed control system (DCS) with the release of DeltaV Version 15 Feature Pack 1. This feature pack release includes new technology and enhancements to current capabilities that not only improve control system situational awareness and performance, but also help ensure more efficient, sustainable operations.
Hybrid and process industry business drivers are continually changing as market dynamics shift product demand and costs. A modern, flexible control system is critical to help manufacturing sites and operations personnel adapt and drive productivity through seamless data connectivity and intuitive decision support applications. The latest release of the DeltaV control system continues the regular cadence between major DeltaV releases to help users more quickly realize the project savings and operational efficiencies that come with new features for their control system software.
"In an era of market volatility, increased focus on sustainability and few spare personnel, organizations are exploring automation projects that will expand their flexibility to help them stay nimble, making it easier to quickly deliver quantifiable value," said Claudio Fayad, vice president of technology for Emerson's process systems and solutions business. "Expanded connectivity and subscription options provide organizations the flexibility they need to design projects with very specific outcomes, measure the success quickly, and then make changes they need to rapidly bring return on investment in line with expectations."
The DeltaV PK Controller line now includes built-in, native integration of PROFINET, further enhancing the wide variety of applications and system sizes addressed by the PK Controller line. With PROFINET capability, the PK Controller is now ready to integrate advanced physical layer (APL) devices, accelerating the adoption of high-speed devices in process environments. Additionally, the DeltaV PK Flex Controller is the newest addition to the line, adding flexible, software-defined control capacity that can scale and adjust as engineering or operational requirements change. Delivered as a subscription, the DeltaV PK Flex Controller reduces upfront cost, eliminates complexity associated with control engineering tasks and allows customers to easily adjust control capacity throughout the lifecycle of a facility.
The extensive suite of software applications that are core to the DeltaV system have also been enhanced in this feature pack, delivering more operational insights through robust analytics and intuitive operator environments. The newest version of DeltaV advanced control applications—Neural, Predict, and Predict Pro—are now available in 1-, 3-, or 5-year term-based licenses improving flexibility and reducing upfront investment supporting a quicker return on investment.
In addition, improved integration of web applications further establishes DeltaV Live as the center of a robust operational intelligence ecosystem providing a single, cohesive view of operations by securely integrating data, video streams, enterprise analytics and other decision support applications. This new capability adds to the existing set of high-performance tools in DeltaV Live to maximize situational awareness and deliver the ultimate operator experience.
Learn more. Visit the DeltaV DCS Version 15 Feature Pack 1 webpage.
https://www.emerson.com/en-us/automation/brands/deltav/deltav-v15/deltav-v15-fp1
Featured Product
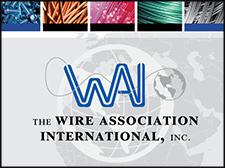