Ensuring The Effectiveness Of Customized Machining Of Non-Standard Components
With the continuous development of manufacturing technology and the increasing diversification of market demands, the customized machining of non-standard components has become an integral part of the manufacturing industry. Customized machining of non-standard components refers to the personalized design and production of components based on specific requirements from customers, encompassing functionalities, dimensions, materials, and more.
Clear Requirements and Communication
Detailed Design and Planning
Building upon a grasp of customer needs, manufacturing enterprises should undertake detailed design and planning. This involves crafting a process flow, selecting appropriate machining methods, determining process parameters, and more. Detailed design and planning ensure the smooth progression of the production process, reducing the need for mid-process adjustments and modifications.
Appropriate Machining Equipment and Processes
The selection of suitable machining equipment and processes is paramount for the customized machining of non-standard components. Based on the characteristics and requirements of the components, manufacturing enterprises should opt for the right machining equipment to ensure accurate and efficient completion of tasks. Concurrently, the application of suitable machining processes ensures component quality and precision.
Stringent Quality Control
Customized machining of non-standard components necessitates rigorous quality control measures. Manufacturing enterprises should establish a comprehensive quality management system, spanning the entire process from raw material procurement to final product inspection. Through stringent checks and tests, the quality of non-standard components can be ensured to meet the required standards.
Flexible Production Adjustment Capability
Customized machining of non-standard components may require some adjustments and modifications during the machining process to meet actual customer needs. Manufacturing enterprises should possess the flexibility to make production adjustments promptly based on customer feedback and requirements, ensuring the final product aligns with customer expectations.
Continuous Improvement and Innovation
Customized machining of non-standard components is an ongoing developmental process. Manufacturing enterprises should continually strive for improvement and innovation, exploring new machining technologies, processes, and materials to enhance production efficiency and product quality. Simultaneously, active learning from customer feedback and experiences allows for constant refinement of customized machining processes and methods.
In conclusion, ensuring the effectiveness of customized machining for non-standard components requires a comprehensive understanding of customer requirements, detailed design and planning, the selection of appropriate machining equipment and processes, rigorous quality control, the capacity for flexible production adjustments, and a commitment to continuous improvement and innovation. By employing these key methods, manufacturing enterprises can effectively achieve customized machining for non-standard components, meet specific customer needs, and enhance product quality and market competitiveness.
Featured Product
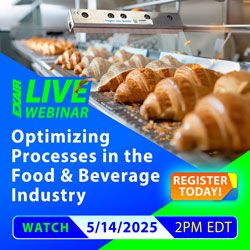
Safety Air Guns use engineered air nozzles
Inexpensive air guns can be found in many places and triggers or other parts break quickly. They simply blow a lot of compressed air. Many produce noise levels that violate OSHA requirements, generating dangerous dead-end pressures. EXAIR's Safety Air Guns eliminate these problems, are durable, comfortable to use. Each uses an engineered Air Nozzle that provides superior performance, lowering air consumption and noise.
See our SAG Promotion running now. http://www.exair.com/184/sagpromo.htm