NORD DRIVESYSTEMS Provides Advantageous Corrosion Protection for Extreme Operating Conditions
NORD’s nsd tupH™ sealed conversion system delivers an easy to clean surface optimized for harsh processing and manufacturing environments.
Harsh operating conditions are present in many industries such as food and beverage, bakery, automotive parts washing, chemical, water treatment, marine, car wash, and pharmaceutical industries. Applications in these environments are often subjected to intensive cleaning, high-pressure washing, and disinfection processes to meet the highly regulated, hygienic standards. To prevent gear motors from material destruction due to the rigorous cleaning agents and disinfectants, NORD DRIVESYSTEMS developed nsd tupH - a sealed surface conversion system that ensures easy yet safe cleaning, ultimate surface durability, and wear resistance.
The nsd tupH treatment uses a chromate-free chemical process that permanently alters the aluminum housing's physical properties to create a surface that is up to 7 times harder than the original. A clear sealant is then applied on top of the base layer to form a smooth surface that is easy to clean and maintain. The sealant also provides additional protection against acids and alkalis and will not spread corrosion, even if damaged. When compared to traditional surface protection methods such as paint, nsd tupH will not blister, flake, or chip and provides a more durable corrosion resistance.
Stainless steel units are often used in similar harsh environments but unlike nsd tupH units, are heavy, costly, and dissipate heat poorly. The advantages of using aluminum products are the material's inherent low weight, compactness, and ability to effectively conduct heat, keeping operating temperatures low and prolonging the service life of the internal transmission components. Another advantage of nsd tupH compared to stainless steel is the product availability. Whereas stainless steel can only be used with a small range of products, nsd tupH is available with a wide variety of NORD's modular drive system options such as:
-NORDBLOC.1® helical inline gear units
-NORDBLOC.1® two-stage helical bevel gear units
-UNICASE™ parallel shaft gear units
-UNIVERSAL SI worm gear units
-UNIVERSAL SMI worm gear units
-DuoDrive integrated gear units
-Smooth surface motors
-NORDAC ON/ON+ variable frequency drives
NORD units that are treated with nsd tupH also include additional hygienic options such as stainless-steel shafts and hardware, special shaft sealing rings to prevent moisture from entering the gear unit, and IP69-rated protection. Additionally, nsd tupH conforms to FDA Title 21 CFR 175.300 and can be built with synthetic or mineral food grade lubrication for applications with extreme temperatures or those in the food and beverage industry.
Moisture, acids, alkalis, and salts are present in many applications in the food and beverage industry, making rapid drive deterioration a constant concern. Painted cast iron units used in these environments often fall short of demands and see a high turnover rate. NORD's nsd tupH drive systems however, are engineered for robustness and even provide durability in the humid, salty atmospheres of the seafood industry where conventional cast iron units can begin to rust within several weeks and stainless steel units require long cool-off periods before they can be hosed-down.
Not only is nsd tupH ideal for hygienic applications, it is also beneficial in industries such as wastewater treatment where drive systems are exposed to fluctuating temperatures and harsh outdoor conditions. Treating these systems with nsd tupH prevents corrosion from wastewater, precipitation, and chemical cleaning. This durable solution ensures units have a long lifespan with more efficient operation and fewer system replacements.
With the nsd tupH sealed surface conversion system, NORD DRIVESYSTEMS offers a reliable surface treatment solution for gearboxes, motors, variable frequency drives, and components to withstand extreme system conditions.
Featured Product
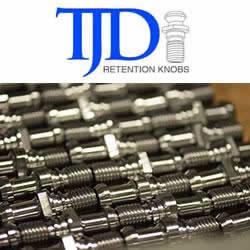