The industry demands absolute precision, totally repeatable manufacturing processes, and zero failure rates for products that are frequently used in safety-critical applications. As such they must work alongside and partner with companies that are working
With the advent of cutting-edge sensor technologies, measurement capabilities have become increasingly sensitive, enabling the detection and characterization of minute features and deviations in samples. To leverage the full potential of these advanced sensors, it is essential to have motion control stages that can move the samples or sensors with extreme precision and stability.
(May 26th 2023, Arvada, CO, USA) The demand for nanometer-capable stages is increasing exponentially as the trend to achieve greater precision and control in metrology and nano-metrology applications continues.
With the advent of cutting-edge sensor technologies, measurement capabilities have become increasingly sensitive, enabling the detection and characterization of minute features and deviations in samples. To leverage the full potential of these advanced sensors, it is essential to have motion control stages that can move the samples or sensors with extreme precision and stability.
The ability to traverse several hundred millimeters while maintaining nanometer-level accuracy opens up new possibilities for research, quality control, and manufacturing processes that require intricate measurements and fine adjustments. As a result, the development of nanometer-capable stages has become crucial to meet the demands of modern metrology and unlock further advancements in various industries.
Any inaccuracies or errors in the motion can significantly affect the measurement results. Even minor deviations or vibrations during the movement of the sensors can introduce unwanted noise and artifacts, compromising the overall accuracy of the measurements.
"To overcome this challenge, motion systems must be engineered with exceptional precision and stability. They need to be capable of achieving sub-nanometer resolution and maintaining tight tolerances throughout the entire range of motion. By surpassing the accuracy of the sensors, these high-precision motion systems ensure that the measurements obtained are not limited or compromised by the motion itself, enabling researchers and industries to achieve the highest level of measurement accuracy possible," explains ALIO Industries President Bill Hennessey
For such applications, ALIO provides its vertical Z-stages and monolithic XY bases. ALIO's Z-stages stands out with their innovative design, offering a vertical solution that is completely linear-based and delivers performance comparable to air-bearing systems.
Hennessey continues, "What sets ALIO's Z-stage apart is its exceptional precision, surpassing traditional Z-wedge solutions by an order of magnitude. This means that our Z-stage can achieve unparalleled levels of accuracy and stability in vertical positioning applications."
By eliminating the drawbacks associated with traditional Z-wedge mechanisms, such as non-linearity and mechanical hysteresis, ALIO's unique design ensures consistent and reliable vertical movement with sub-nanometer resolution, opening up new possibilities for nano-metroloy applications and nanotechnology, semiconductor manufacturing, and optics manufacturing, enabling OEMs to achieve levels of performance that were previously unattainable with conventional solutions.
Using a vertical Z-stage on a monolithic XY base allows the customer's payload to be mounted directly on the top of the stage in-line with the motor, encoder, bearings, and counterbalance, thus minimizing overhanging brackets and greatly reducing potential Abbé errors (optical distortions that occur due to the variation in focal lengths for different wavelengths of light, resulting in color fringing and reduced image sharpness).
ALIO's XY monolithic stages introduce previously unheard-of straightness and flatness of travel with nanometer precision to reduce measurement uncertainty for metrology OEMs, ensuring more precise and reliable measurement data, which is crucial for quality control, research, and next generation manufacturing processes.
ENDS
www.alioindustries.com
Featured Product
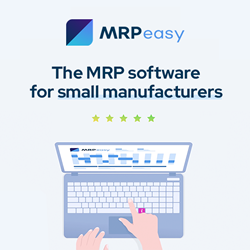