Types Of Aluminum Alloys For CNC Machining
Aluminum alloys are one of the most versatile and efficient materials designed for products in various industries.
Aluminum alloys are one of the most versatile and efficient materials designed for products in various industries. The material has excellent strength, outstanding corrosion resistance, heat treatability. As a result, many manufacturers have adopted different types of aluminum alloys for a variety of applications.
There are different grades of aluminum alloys suitable for CNC machining, each with different alloying elements and properties. Therefore, it is imperative that you understand the differences between these aluminum alloy grades in order to choose the right one for your project. This guide explores common aluminum alloy types suitable for CNC machining, their properties and applications.
What Is Aluminum Alloy?
Aluminum alloys are a unique combination of different metal elements for increased strength and durability. Aluminum is traditionally lightweight and has excellent corrosion resistance. These alloys are formed by combining aluminum in liquid/molten form with other elements which then cool and solidify to form a homogeneous solid material. Other elements that combine with aluminum to form these alloys may account for up to 15% by mass.
Examples of these additional elements include zinc, iron, magnesium, copper and silicon. What's more, the addition of these elements to aluminum provides the alloy with enhanced electrical conductivity, corrosion resistance, machinability and strength compared to pure metallic elements.
Properties Of Aluminum
Aluminum has many outstanding properties that make it well known and commonly used in most applications. Here are some of them:
Corrosion Resistance
Aluminum develops a natural thin oxide layer that protects the metal from reacting with the environment. Therefore, it is suitable for a variety of applications that may be exposed to corrosive agents, and aluminum alloys have higher corrosion resistance than pure aluminum.
Light
The standard weight of aluminum is exactly 2.7 g/cm³, which is about a third of the weight of steel. Its lightweight properties help to significantly reduce its manufacturing costs. The composition of the aluminum alloy type can also be adjusted to modify the weight depending on the application.
Electrical And Thermal Conductivity
Due to its weight, aluminum is a good conductor of electricity and heat. It has twice the electrical and thermal conductivity levels of copper. Therefore, it is commonly used in the manufacture of power transmission lines. Plus, it has an excellent heatsink/heatsink feature, making it ideal for devices that need to dissipate heat quickly.
Types Of Aluminum Alloys Commonly Used In Machining
This section discusses the various types of aluminum alloys that can be used in machined products.
Aluminum 6061
6061 aluminum has silicon and magnesium as the main elements. It is suitable for a variety of applications due to its strength, corrosion resistance, weldability and heat treatability. It is well suited for extrusion techniques and applying a T6 temper helps make it stronger and more durable. Likewise, it does well with anodizing to improve aesthetics.
Aluminum 7075
7075 aluminum alloy is a strong alloy with excellent strength, similar to steel. Its main alloying elements are copper and zinc. It can be used in applications requiring excellent strength,
Aluminum 5052
5052 Aluminum is a reliable alloy with excellent corrosion resistance and moderate strength. Since there is no copper in the alloy, it is very suitable for salt water applications. Marine equipment is the most common component made from 5052 aluminum. However, 5052 is from the 5xxx aluminum alloy grades and therefore cannot be heat treated.
Aluminum 6063
6063 aluminum alloy contains magnesium and silicon and is often referred to as construction aluminum due to its moderate strength and high ductility. High compatibility with mold forming. Additionally, 6063 aluminum is highly corrosion resistant due to its magnesium silicide content.
Aluminum Application
Aluminum is a metal that has a wide range of applications in various industries. Here are a few examples of industries where aluminum components and products are widely used:
Medical Industry
In industries where cleanliness and biocompatibility are mandatory, aluminum parts and products have taken up the task. Medical devices include various types of aluminum, such as surgical and orthopedic instruments. In addition, some general equipment such as trays and containers also use aluminum as the main component
Aviation Industry
Aircraft require lightweight yet strong construction materials. With aluminum's high strength-to-weight ratio, it fit the bill perfectly. This property also ensures that it can carry as much cargo as metal that is stronger than it. Additionally, with its high corrosion resistance, it also helps prevent damage to aircraft when exposed to harsh environmental conditions.
Electrical Industry
Consumer electronics manufacturers continue to use aluminum alloys in their products due to their excellent thermal conductivity. This property has been used in electronic components such as heat sinks and cooling elements for graphics processors.
Automobile Industry
An ideal vehicle should be lightweight, durable and environmentally friendly. Aluminum is a metal that can help achieve these goals. Thanks to its lightweight nature and high level of durability, the vehicle can be flexible while still retaining its sturdiness. In addition, the use of aluminum makes auto parts recyclable, thereby increasing the sustainability of cars using aluminum parts.
Conclusion
Aluminum is an extremely versatile metal that has different properties depending on the elements it is combined with. Additionally, different types of aluminum have different properties that make them suitable for different industries.
Featured Product
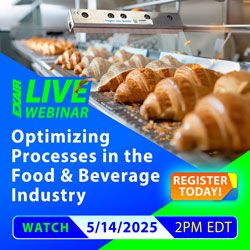
Cabinet Cooler Systems
Stop electronic control downtime due to heat, dirt, and moisture! A low cost, reliable way to cool and purge electronic control panels. EXAIR Cabinet Coolers incorporate a vortex tube to produce cold air from compressed air - with no moving parts. https://exair.co/184_540