Benefits of Using Automation for Chemical Manufacturing
Automation in manufacturing and chemical production is the integration of robotic systems and software for controlling and monitoring the manufacturing and production of chemicals.
Automation in manufacturing and chemical production is the integration of robotic systems and software for controlling and monitoring the manufacturing and production of chemicals. Further, it decreases the demand for manual labor and offers higher accuracy and productivity in the production process. There are several benefits of using automation for chemical manufacturing. It can also help in reducing waste, improving safety, and decreasing environmental impacts.
Introduction
In chemical production and manufacturing, automation highly improves the efficiency and standard of a process. The benefits of automation for chemical manufacturing are allowing for more efficient handling and control of chemical reactions. In order to accomplish desired product quality. It also has a considerable impact on safety and environmental outline. In today's guide, we will be covering the top benefits of automation for chemical manufacturing along with related concepts.
About The Company
Aeologic Technologies is a dynamic, solution, and value-driven technology company allowing businesses with innovative and innovative technologies and solutions. We are providing our services in transport, education, food industry, retail, logistics, industry 4.0, health and environment, and natural resources management (NRM) areas.
Top Benefits of Automation for Chemical Manufacturing
Following, we've discussed the major benefits of automation for chemical manufacturing.
1. Enhancing Safety
Automation can be implemented to maximize safety in chemical production and manufacturing by decreasing human error and enhancing the accuracy of procedures. It can also aid to monitor process conditions more precisely and providing feedback to operators in real-time.
Furthermore, automation can be integrated for detecting dangerous conditions before they become dangerous and to alarm operators to take corrective action. Automation can also facilitate in reducing the number of manual tasks, which can help in avoiding accidents due to operator fatigue.
Finally, automation can be applied to deliver a more consistent quality of product, which is helping to minimize the risk of unsafe products reaching the market.
2. Improving Efficiency
Automation is the application of technology for controlling and monitoring production processes, decreasing the need for human intervention. Furthermore, it can help to increase productivity and efficiency in chemical production and manufacturing processes in a variety of processes.
First, automation can decrease errors and boost accuracy. Automated systems can help in ensuring that the right chemicals and materials are utilized in the right amounts, and that the right processes are followed in the system This can help in reducing waste and augment the quality of the finished product.
Second, automated systems can help in accelerating production processes. Automation can be used for streamlining production and cutting down on time-consuming manual tasks. This can be leading to higher throughput and a faster manufacturing cycle
Finally, automation can help in improving safety in the workplace. Also, automated systems can help in decreasing the risk of accidents, as well as helping to enforce safety procedures and protocols. Automated systems can also facilitate in reducing the risk of exposure to hazardous chemicals and materials.
3. Cost Savings
Automation can help to decrease costs in chemical production and manufacturing in several ways. Moreover, the benefits of automation for chemical manufacturing processes can help to reduce labor costs, reduce waste, improve the accuracy, boost productivity, and consistency of production, and reduce the requirement for manual oversight.
Automation can also minimize energy costs, equally in terms of the energy used to power the machines and in terms of the energy used to create the chemicals themselves. It further aids to decrease the cost of raw materials by streamlining the production process, reducing waste, and enhancing the accuracy of the production process.
4. Reducing Waste
Automation is one of the most productive ways to decrease waste in chemical production and manufacturing. Automation decreases human error and makes sure that processes are performed efficiently and accurately.
Further, automated systems can more accurately measure the amounts of materials used for each production process, which facilitate to reduce waste. It also offers real-time data on production processes, which can be implemented to make adjustments to reduce waste.
Finally, automation can be integrated to track and monitor the waste materials produced during production processes, enabling for more effective waste management.
5. Increased Scalability
Automation has been an important part of chemical production and manufacturing for several years. Automation is the implementation of computers, machines, and other technology to automate processes and operations. Also, the benefits of automation for chemical manufacturing is allowing for more efficient production and manufacturing, as well as higher scalability.
Moreover, it can be applied to boost scalability in chemical production and manufacturing by accelerating the production process, increasing production accuracy, and reducing costs.
In addition, it can also help in improving safety by removing human error and increasing consistency. It can also augment scalability by enabling multiple production lines to be run simultaneously, boosting production throughput and decreasing the amount of time required to produce a given amount of product.
Wrapping Up
The benefits of automation for chemical manufacturing can provide increased efficiency, enhanced product quality, decreased costs, improved safety, and improved regulations compliance.
The application of automation in chemical production and manufacturing allows for faster, more reliable operations, and more accurate, reducing the risk of human error and improving overall process control. Automation can also allow real-time monitoring of significant process variables, such as pressure, temperature, and chemical concentrations, which can enhance product quality and decreasing the risk of defects or batch failures.
Featured Product
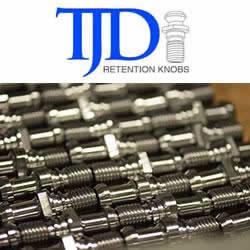