Tompkins Robotics New PickPal Product Series Expands Robotic Solutions Portfolio
Attendees of ProMat can see a demonstration of this system in the Tompkins Robotics ProMat Booth N7140 from the 20th-24th. There are currently two models in the PickPal series, the standard PickPal which can carry 60 kg of orders, and the PickPal+ which handles up to 100kg of orders.
Orlando, FL, March 20, 2023- Tompkins Robotics is expanding its robotic solution offerings and will be introducing its new PickPal product series which is a line of pick assist (PA) autonomous mobile robots (AMR) at ProMat. Attendees of ProMat can see a demonstration of this system in the Tompkins Robotics ProMat Booth N7140 from the 20th-24th. There are currently two models in the PickPal series, the standard PickPal which can carry 60 kg of orders, and the PickPal+ which handles up to 100kg of orders. There are additional models coming soon to carry more orders, have higher capacity, and apply pick assist technology to case picking. This robotic technology follows Tompkins Robotics core design elements of producing adaptive, flexible, and scalable solutions.
PickPal provides a quickly implemented and low operating cost robotic technology that can be inserted into existing operations doing order fulfillment in a scalable RaaS model. The RaaS model has minimal implementation costs and a low cost of ownership while driving significant labor savings and capacity improvement. PickPal will drive capacity, cost, and workforce improvements in operations that are struggling with meeting fulfillment demands. PickPal integrates with other technologies to improve efficiency in existing automated systems as well. Mike Futch, President & CEO of Tompkins Robotics, explains how the PickPal solution is positioned and benefits the supply chain market. Tompkins Robotics PickPal series provides a new solution with more flexible contracts, lower monthly cost, and minimal risk to help 3PL, e-commerce and other fulfillment customers handle the growing problems that traditional, large-scale solutions cannot easily address. PickPals ability to handle the rising number of SKUs, increases in each picking, and faster delivery demands make it a terrific solution for customers to address their fulfillment problems.
Tompkins Robotics continues to develop technologies and new applications that evolve the picking and sortation process helping increase the capacity and utilization of their customers distribution and fulfillment centers. Tompkins Robotics will be demonstrating their new PickPal solution at ProMat, Booth N7140, as well as in the Tompkins Robotics Lab in Orlando, FL. For additional information or to arrange a demonstration of the Induction Lift please visit www.tompkinsrobotics.com. Media are invited to meet with Tompkins Robotics representatives during the product launch press conference at Booth N7140 on Tuesday, March 21st at 1:30 PM. Contact Lauren Fiochetta at lfiochetta@tompkinsrobotics.com for more information.
About Tompkins Robotics
Tompkins Robotics focuses on robotic automation of distribution and fulfillment operations. Beginning over five years ago with our robotic sortation solution, tSort, we have continued to develop innovative solutions to provide our customers unmatched flexibility and capacity throughout their supply chain processes. We have added solutions upstream, like our Pick Assist AMR, PickPal, as well as downstream, with the only automated takeaway unit from a unit sorter robot, xChange. Our warehouse execution systems, tWES, links all these technologies and provides a broad solution set for our customers. Tompkins Robotics continues to evolve and enhance our customers operations with solutions that maximize modularity, floorspace, flexibility, and speed of implementation and our RaaS financing option allows for customers to see an even faster ROI to make them more successful in todays dynamic marketplace. Additional information available at www.tompkinsrobotics.com
Featured Product
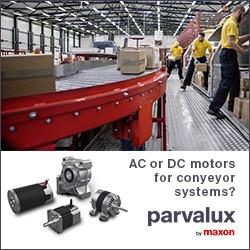