UltraFlex induction brazing carbon steel gas filters within 3 seconds
Thanks to the test application set up by UltraFlex, the customer could confirm that by replacing his current brazing process with semi-automatic induction brazing he would be able to increase the productivity in this process.
The time- and cost-efficient induction brazing process for carbon steel gas filter components has recently been demonstrated by UltraFlex Power Technologies. The demonstration had been set up per request of a customer from the automotive industry looking to evaluate the use of induction to increase repeatability and productivity for this brazing process.
Being a leading manufacturer of advanced, digitally controlled induction heaters, UltraFlex is frequently setting up test applications per customer request. The test applications aim to define the induction heating parameters for each specific customer scenario and estimate the expected time, energy and cost savings the customer could achieve by using induction.
The customer parts to be brazed in this case were a gas filter cap with brazing joints on either end of the filter and pegs. The required heat cycle was 5 seconds per joint, with a continuous duty cycle.
For this induction brazing process, UltraFlex engineers recommended the use of an UltraFlex UltraHeat SM induction heater, along with a HS-4W water-cooled Heat Station. UltraHeat SM are compact and easy-to-use 5 kW induction heaters that can be used with either a water-cooled or air-cooled remote heat station. They feature adaptive digital phase control providing efficient operation in a wide frequency range.
At output power of 5 kW and a target temperature of 1300°F (704.44°C), this brazing process was completed within mere 3 seconds. The heating cycle got vastly reduced thanks to the UltraFlex approach to braze the tabbed joint from the inside. Thus, the operator does not have to wait for the heat to penetrate through, and a strong and reliable joint can be achieved within a very short time, increasing the customer's productivity in this process.
Thanks to the test application set up by UltraFlex, the customer could confirm that by replacing his current brazing process with semi-automatic induction brazing he would be able to increase the productivity in this process. In addition, thanks to the digitally controlled induction heating equipment, which can be pre-programmed with the required heating parameters, the repeatable, consistent results in this process could be fully guaranteed, regardless of the operator skills.
Finally, by using a no-flame brazing, the customer would achieve a green and safe process - safe for the operator, safe for the environment.
Find out more at:
https://ultraflexpower.com/
Contact us at:
+1.631.467.6814
uptnews@ultraflexpower.com
Svetla Markova
About UltraFlex Power Technologies:
UltraFlex Power Technologies (ultraflexpower.com) offers the most advanced and innovative digitally controlled induction heating equipment in the industry. Its compact modular and flexible systems are used for a wide variety of induction heating, casting and melting applications.
Featured Product
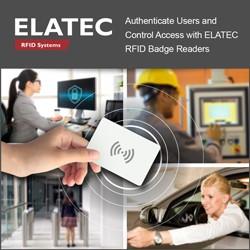