Manufacturing Productivity: Zero and Thin Clients Minimize Downtime
Zero client terminals can dramatically reduce process downtime by virtually eliminating issues related to compatibility, maintenance, and virus protection
Downtime in manufacturing can translate into millions of dollars in lost revenue. Minimizing disruptions is just as pivotal as maximizing quality and output to maintain profit margins. As more computers and software are used to automate the production process, the computer's uptime is crucial to prevent unplanned downtime on the manufacturing plant floor.
The failure of any computer used in manufacturing causes unexpected delays during production and can last any length of time. Without notice, this stoppage can induce considerable revenue loss. Every item a manufacturer produces represents potential profit. These values add up over time—based on how fast each unit is produced. These unplanned halts during production disrupt the maximized hours of a workday and inevitably diminish optimized revenue.
A preventive maintenance plan can help to minimize manufacturing downtime. The most expedient corrective actions can also minimize downtime when a computer failure occurs due to hardware problems, an operating system crash, or a computer virus. The time required to address the failure is in direct correlation to the availability of materials to fix the hardware, as well as a knowledgeable workforce with the ability to resolve the issue.
"The priority for manufacturers is to achieve maximum efficiency by eliminating unplanned downtime altogether," says Paul Shu, President of ARISTA Corporation, a leading provider of rugged computing platforms and audio-visual solutions.
He adds that Zero Client terminals stand out in this area, and have the quickest recovery when failure occurs.
Minimizing Manufacturing Downtime
The computers used to automate the manufacturing process may last for several years before failure or replacement. However, computer hardware changes, operating system updates, and software revisions typically occur every one to two years. The challenge is that it may take hours, days, or even months to recover when new hardware is not compatible with the existing Operating System, or existing HMI/SCADA software is not compatible with new Operating System.
Zero Client computers minimize or eliminate these incompatibility issues. A Thin Client / Zero Client only acts as a terminal (display, keyboard, and mice), as software is executed at the servers.
Zero Client hardware changes make no impact to the operation recovery. Zero Clients do not have storage (No HDD or SSD), or an Operating System. The operation recovery only takes a few minutes after Zero Client hardware is replaced. The Zero Client's Operating System resides in servers. A Zero Client boots off from the servers remotely and the Operating System is not retained in the Zero Client after it is powered off.
Since Zero Clients do not have storage, an Operating System, or any application software, virtually no maintenance is required for plant floor workstations. This results in significant savings of time and effort when multiplied across potentially hundreds of manufacturing facility workstations.
For manufacturers, minimizing maintenance work decreases downtime, which increases productivity and profit. In fact, the Zero Client itself is impervious to worms or viruses since it does not have storage and the Operating System does not reside in the client after power off.
The Zero Clients' Operating System boots remotely. If the Operating System were actually compromised after the system booted, simply rebooting the Zero Client is all it would take to resolve the issue. Compare this to the time and money it would take to supply updates to each Windows-based computer on the plant floor, or the maintenance required to remove a virus.
Zero Clients also require minimal CPU horsepower and memory size to operate, since the units do not have storage capability. Fewer components result in higher meantime between failure hours, which improves reliability. The result is that Zero Clients have a much higher lifespan than traditional Windows-based workstations used on the manufacturing plant floor.
For more information, contact ARISTA Corporation at (510) 226-1800, e-mail sales@goarista.com, or write to 48460 Lakeview Blvd. Fremont, CA 94538.
Featured Product
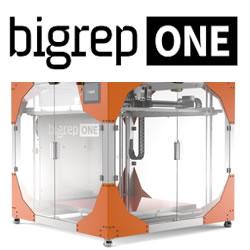
BigRep ONE: Large-Scale 3D Printing
The BigRep ONE is an award-winning, large-format 3D printer at an accessible price point. With over 350 systems installed worldwide, it's a trusted solution for prototyping and production by designers, innovators, and manufacturers alike. Featuring a massive one-cubic-meter build volume, the fast and reliable ONE brings your designs to life in full scale.