The development status of welding automation of steel pipe welding
The inability to continue to work, the future of welding work will be done mostly by robots, steel pipe welding automation will certainly become the future of welding trends.
In the steel pipe welding automation process more and more quickly, a variety of types of welding robots came into being, welding robots in the process of work mainly using the "teaching - reproduction" mode, the welding path needs to be set in advance in the robot, the subsequent The robot follows the set trajectory for welding, with high repetition accuracy and improved welding efficiency. However, due to the thermal deformation of the workpiece during the welding process and the deviation of the fixture positioning, the actual welding path does not match the taught path, which reduces the welding accuracy and efficiency and may lead to welding failure and scrap of the workpiece in serious cases.
The laser seam tracking sensor is placed in front of the welding head to collect the shape of the weld seam, and then the software algorithm will derive the real position of the welding target point, and transmit the data to the robot in real time to guide the robot to weld on the real trajectory, complete all kinds of complex welding, avoid welding quality deviation, realize unmanned welding, and can greatly improve the welding accuracy and work efficiency. Welding automation selects suitable welding equipment according to actual needs to ensure the smooth progress of welding work.
When welding non-standard automation equipment can be used for automatic welding, the workpiece can be rotating movement to achieve the desired position of the weld pipe. It is too early for welding robots to completely replace manual welding, but the goal of replacing 90% of welders with welding robots in batch welding operations is achievable. Welding robots are favored by more and more SMEs for their high efficiency, high quality, and ease of management. For some products that require high precision but cannot be solved by welding robots, users need to add automatic weld seam tracking and positioning systems in time. Pressure welding can perform welding between dissimilar materials, including metals, plastics, ceramics, etc. The welding is well formed, and the weld seam is beautiful and solid. The welding automation of welding automation machine needs to have good resistance to electromagnetic field interference so that the weld seam can be tracked automatically.
Automated welding is robot welding instead of manual welding, after the manual clamping of the workpiece is completed, then the robot will weld the workpiece. Robot automated welding has the advantages of high consistency of weld seam, stable quality of finished product, uniform appearance of weld seam, fast welding speed and low technical threshold compared with manual welding. At present, it is difficult to recruit skilled workers, and it is even more difficult to recruit for welding. Because welding has a certain harm to the body, so the younger generation are reluctant to choose welding class work. Plus the older generation is about to face the decline in physical function, the inability to continue to work, the future of welding work will be mostly done by robots, automatic hanging welding will certainly become the future of welding trends!
Nansteel Manufacturing Co.,Ltd is a company specializing in the production of carbon steel pipes, stainless steel pipes, structural sections and pipe fittings, with a wealth of experience in production, including different seamless pipe specification, welded pipes and so on. For more, please visit: www.nan-steel.com
Featured Product
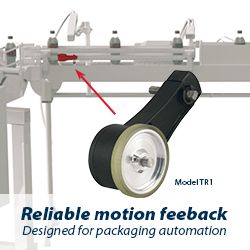