UltraFlex demonstrates induction soldering of aluminum to glass
In addition to ensuring an energy- and cost-efficient soldering process, the use of induction for this soldering scenario would guarantee reliable and consistent soldering results, regardless of the operator skills.
A recent demo application by UltraFlex Power Technologies showcased the successful use of induction for soldering aluminum to glass. The demo application was set up per request of a company from the Aerospace & Defense industry evaluating the option to use induction for soldering of optomechanical parts. A heating cycle as short as possible was required, at maximum heating temperature of 300°C.
The parts to be soldered in this induction heating scenario were an aluminum plate and a glass block. Glass has one of the lowest thermal conductivities due to the lack of ordered crystal structure. Hence, to be able to solder it to the aluminum plate, UltraFlex had to apply a coating of gold, nickel, copper and silver to the glass. In addition to withstanding the heating applied, this coating would also not peel off from the glass.
UltraFlex engineers considered the use of an UltraFlex heater from the UltraHeat S series as most appropriate for this induction heating scenario. UltraHeat S are compact and efficient 2kW induction heaters that operate with either a water-cooled or air-cooled remote heat station. In this case, water-cooling was used, together with a pancake induction coil. An IR pyrometer was used to regulate the temperature of the soldered area.
At a power of 501 W applied, it took mere 15 seconds to solder the two parts, at a temperature of 280°C. Following the application test, UltraFlex engineers confirmed that induction could be successfully and efficiently used for this soldering application. The soldering process could be further optimized if a proper fixture was designed and a pyrometer used to control the heating temperature. They also recommended the usage of solder alloys with lower heating temperatures, as well as the addition of flux.
In addition to ensuring an energy- and cost-efficient soldering process, the use of induction for this soldering scenario would guarantee reliable and consistent soldering results, regardless of the operator skills. The customer would achieve a safe and clean working environment, due to the lack of smoke and noxious emissions.
Find out more at:
https://ultraflexpower.com/
Contact us at:
+1.631.467.6814
uptnews@ultraflexpower.com
About UltraFlex Power Technologies:
UltraFlex Power Technologies (ultraflexpower.com) offers the most advanced and innovative digitally controlled induction heating equipment in the industry. Its compact modular and flexible systems are used for a wide variety of induction heating, casting and melting applications.
Featured Product
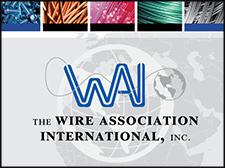