MICROMETAL PROVIDES PARYLENE PROTECTIVE COATINGS FOR METAL PARTS & COMPONENTS
This is one in an array of ancillary post-process options provided my micrometal as the company constantly invests to produce optimised outcomes for customers looking for ultra-precise metal components often used in safety critical applications.
(28th March 2022, Muellheim, Germany) micrometal GmbH (incorporating Etchform and HP Etch) is pleased to be able to provide Parylene protective coatings to the precision metal parts and components made using its photo-chemical etching (PCE) process. This is one in an array of ancillary post-process options provided my micrometal as the company constantly invests to produce optimised outcomes for customers looking for ultra-precise metal components often used in safety critical applications.
Jochen Kern, Head of Sales and Marketing at micrometal explains, "Parylene is the ultimate protective coating, and is used for customers that require protection of equipment, components, and surfaces in a range of end-use applications. Parylene is a hydrophobic polymer which is lightweight and can be applied as an extremely thin homogeneous film. This film is absolutely smooth and totally transparent, and does not cause any unwanted effects such as surface tension and distortion. The coating provides incredible resistance to aggressive media and liquid hydrocarbons, and can also be used as a diffusion barrier to gases. The coating also passes the salt fogging test, and is biocompatible which opens up its use in medical applications such as stents, catheters, needles, medical electronics, medical seals, medical elastomers, hearing aids, implants, pacemakers, and electro-surgical instruments."
micrometal also routinely uses the Parylene coating process for automotive applications (such as fuel cells, gaskets and seals etc…,) LED's, electronics, MEMS/ nanotechnology applications, and in defence and aerospace applications such as for circuit cards and satellite electronics etc…
Parylene coating is a 3-step process. Step one is the evaporation of the parylene from its solid "dimer" state into its gaseous state, which is done by heating the dimer to 175°C. Step two pyrolyses the gas to convert it into its monomeric form, and step 3 sees the monomeric gas deposited in the vacuum deposition chamber at room temperature as a transparent polymer film. Depending on the final application, the coating thickness can be anything between 1 µm to up to 50 µm thick.
Kern continues, "The advantages of using a Parylene coating are numerous and varied. It obviously exhibits superior protective properties, and is insensitive to inorganic agents, acids, bases, and solutions. This means that it is appropriate to use on metal parts and components that are to be used in highly dynamic and harsh end-use environments. The coating is resistant to corrosion, is a good barrier to moisture and chemicals, has high temperature resistance (from -220°C to + 200 °C), and high dielectric strength (5000V / 25 μm). The coating process also ensures layer thickness consistency regardless of geometry, and its low coefficient of friction means that it can be used as a lubricant."
Parylene is optically clear, and as a dry film lubricant eliminates the need for liquid release agents. As it is applied at room temperatures, it can effectively be used on any metal parts and components that can withstand a moderate vacuum.
Kern concludes, "Industry is beginning to recognise the role that PCE has in the modern supply chain, and how the precision of the technology and unique process criteria allow for the mass manufacture of parts impossible using more conventional metal fabrication techniques. The ability to apply Parylene coatings to the parts that we manufacture fits with our mission to provide a versatile and ever evolving level of service for customers that demand best-in-class precision metal parts and components."
www.micrometal.de
Featured Product
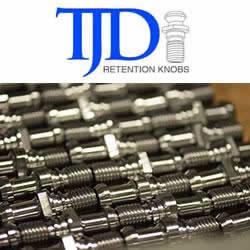