Meissner relies on FASTSUITE E2 software solution to benefit from the use of robotic mold making
Efficiency boost and faster cycle times in mold production
Stuttgart, November 18, 2021 - Toolmaking and plant engineering firm Meissner relies on FASTSUITE E2 to break new ground for its robotics systems: Thanks to powerful automation and simulation in robot-assisted embossing, the company has drastically reduced cycle times in production.
With robot assistance, Meissner can now manufacture an extensively embossed mold in seven to ten days, depending on size. Automation has therefore cut cycle times drastically.
FASTSUITE E2 - plus programming methodology and uploader
To make robot-aided embossing possible, one has to create a dedicated machine control program - a complex task that Meissner brought to a successful conclusion together with software and consulting provider CENIT. Because industrial embossing is a comparatively rare manufacturing technology, the partners decided to adapt an existing FASTSUITE E2 technology package (stud welding) to match Meissner's needs. Based on customer's requirements, CENIT team developed an efficient programming method and complemented it with the required downloader (translator). The process points for the embossing can be uploaded to FASTSUITE E2 as a set and easily programmed by process groups. The pilot project involved 160,000 process points, but the solution can handle a great deal more.
Precise simulation for 24-hour embossing without manual intervention
The result is impressive: In addition to the drastic reduction in processing times, highly realistic simulation by FASTSUITE E2 prevents potential collisions and eliminates any problems with singularities before the robot actually begins its work on the mold. Since the embossing process is verified by simulation, the robot can run for up to 24 hours without manual intervention.
FASTSUITE proves its worth - again
Jan Müller, Plant & Operations Manager at Meissner AG, sees additional benefits in using FASTSUITE E2 as a universal software companion: "We can rely on FASTSUITE to program robots and machines from virtually any manufacturer. That's a great advantage because of course our customers come to us with plenty of different models. On top of that, the 3D simulation software already offers us a wide selection of ready-to-use modules for any number of manufacturing technologies
Featured Product
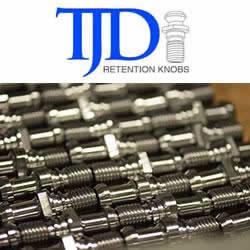
T.J. Davies' Retention Knobs
Our retention knobs are manufactured above international standards or to machine builder specifications. Retention knobs are manufactured utilizing AMS-6274/AISI-8620 alloy steel drawn in the United States. Threads are single-pointed on our lathes while manufacturing all other retention knob features to ensure high concentricity. Our process ensures that our threads are balanced (lead in/lead out at 180 degrees.) Each retention knob is carburized (hardened) to 58-62HRC, and case depth is .020-.030. Core hardness 40HRC. Each retention knob is coated utilizing a hot black oxide coating to military specifications. Our retention knobs are 100% covered in black oxide to prevent rust. All retention knob surfaces (not just mating surfaces) have a precision finish of 32 RMA micro or better: ISO grade 6N. Each retention knob is magnetic particle tested and tested at 2.5 times the pulling force of the drawbar. Certifications are maintained for each step in the manufacturing process for traceability.