The perils of not adopting predictive maintenance
The need to predict the future
Manufacturing and process industries lose an estimated $20 to $60 billion each year due to unscheduled downtime and poor asset quality. That is a staggering amount! Overall Equipment Effectiveness (OEE), a common manufacturing KPI, falls anywhere between 40-85% on average for most manufacturers and has a direct correlation with a plant's profitability. Unfortunately, a reluctance to embrace new software, due in part to the upfront cost, has hindered progress in operations. However, it has never been clearer that there is an urgent need to improve uptime across plant floors.
With the growing need to meet increasingly demanding customers, derive value from big data, deploy cloud solutions and harness the growing power of computing, manufacturers are rapidly shifting to predictive maintenance technologies. Based upon advanced analytics, predictive maintenance marks a new way of organising and implementing maintenance on an industrial scale.
A predictive maintenance plan monitors the performance of equipment under normal operating conditions to reduce the likelihood of failure by being able to - to a great degree of accuracy - predict the future. Predictive maintenance can provide a valuable safety net as we move towards the fourth industrial revolution. As outlined by Deloitte: "In the environment of Industry 4.0, maintenance should do much more than merely preventing downtimes of individual assets. Predicting failures via advanced analytics can increase equipment uptime by up to 20%."
Maintaining your equipment
When done effectively, predictive maintenance is a reliable maintenance strategy, preventing the frequent and costly need for reactive maintenance to be performed on the production line. In the US, dental work is expensive - but a regular check-up, and the completion of minor procedures, would negate the need for more expensive and painful dental work in the future.
As is often said, data is king. That is certainly the case with predictive maintenance where data acts as the fuel to the predictive maintenance engine. Therefore, it is not something that should be done half-heartedly. It is important to provide maximum data quality and coverage. Quite simply, the more information that is available on events, the more accurate the predictions will become.
Providing greater visibility
The manufacturing industry finds itself at a crossroads. Predictive maintenance could be the shot in the arm the industry needs. In many ways it does exactly what it says on the tin. Namely, predictive maintenance provides a reduction of downtime due to being able to predict when a piece of equipment is likely to fail. With studies suggesting unplanned downtime costs manufacturers an estimated $50 billion each year, that is a major advantage. However, not only can knowing ahead of time when an asset will likely fail reduce breakdowns by 70%, but by providing greater visibility it reduces the need to keep superfluous spare parts on hand.
The perils of connectivity
With Industry 4.0, factories are interconnected and smart. Various assets and systems connect via large-scale machine-to-machine communication (M2M) and the internet of things (IoT) to share, analyse, and action data. This has numerous advantages, not least of which providing productivity, agility, and the ability to work to ever-diminishing margins.
However, with machines being increasingly interconnected along the production line, a failing of one machine can halt the entire production process. A domino effect is not uncommon. Therefore, being able to predict potential points of failure so that necessary maintenance can be well-orchestrated and run at less impactful times (i.e. outside of production hours or while the needed personnel is close by) is imperative. Predictive maintenance maximises runtime as repairs can be carried out just before a breakdown, minimising the time taken to maintain equipment as well as production hours lost to manual maintenance.
The role of digital audits in going predictive
There is an important step to be taken before predictive maintenance can be successful in reducing costs and combatting unexpected breakdowns - and that's to invest in digital audits. In the course of a robust layered process audit (LPA) program, auditors will identify machine errors that can lead to unplanned downtime if they go uncorrected. While machines are increasingly interconnected, it is still the case that many machines are not, making visual inspections a must. If non-conformances are being tracked in a traditional pen-and-paper fashion, it is simply not possible to take predictive action based on audit findings even within a single facility. Further, putting preventive measures in place at other plants with the same equipment as soon as an initial non-conformance is identified is only possible when audit results are reported out in real time. Implementing a digital audit platform ensures that as soon as an audit is completed the results are communicated instantly, any identified issues are assigned mitigations immediately, and all facilities are able to track recent and frequent failures for the purposes of conducting predictive maintenance.
Predictive maintenance can only be effective if it has the data to rely on. Digital audits play a key role in maintaining quality levels, ensuring they are consistent and that processes are correct. This is the platform predictive maintenance needs to be built on, so it can flag any quality discrepancies against the original data set.
Don't be left behind
More than half of manufacturing plants now implement a predictive maintenance plan according to Plant Engineering. And for good reason: maintenance remains a time and resource-intensive process. A third (35%) of manufacturers spend more than 10% of their operating budgets on maintenance. Scheduled maintenance takes on average about 19 hours a week, with this rising to more than 30 hours a week for three-in-ten (31%) plants. By implementing predictive maintenance, a manufacturer can, on average, save between 8% to 12% over preventive maintenance and up to 40% over reactive maintenance, according to the Department of Energy. This is not to be sniffed at and is causing predictive maintenance to gain in popularity so much that the market is expected to grow by nearly $10bn by 2026. Isn't it time that you gave it a go?
Featured Product
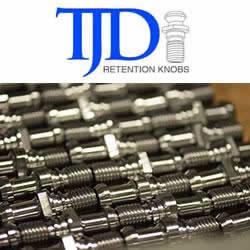