Outsourced SAM Testing Provides a Cost-Effective Solution for Expert Quality Testing and Failure Analysis
Outsourcing ultrasonic-based Scanning Acoustic Microscopy (SAM) testing provides a cost-effective solution for expert quality testing and failure analysis in electronics manufacturing
Ultrasonic-based Scanning Acoustic Microscopy (SAM) has long been the method of choice for
other electronic packages. Ultrasound can locate voids and disbonds between material layers
better than other non-destructive methods because sound waves can look inside the layers to
detect the thinnest of air gaps and delaminations down to a hundredth of a micron.
Increasingly, however, manufacturers in the industrial, aerospace and medical sectors are
turning to SAM technology to ensure good adhesion and mechanical integrity of devices by
examining their internal structures, interfaces, and surfaces. Because potential defects can
occur in different layers, more advanced equipment is required to inspect each simultaneously.
Many are choosing to outsource SAM services rather than do this quality testing in-house.
Outsourcing offers manufacturers key advantages, including capital cost savings on SAM
systems, access to specialized expertise in image management and analysis, and the ability to
diagnose and isolate material defects.
"Customers typically come to us for SAM testing to address one of three needs," says Lisa Logan,
SAM Applications Manager, at Sunnyvale, California-based PVA TePla America provides
contract services and sales for both PVA TePla Analytical and OKOS, both of which design and
manufacture advanced Scanning Acoustic Microscopes. "As part of product R&D, an
engineering team may be evaluating welds, bonds, or the effectiveness of an adhesive. When a
product is in production, we may be asked to scan trays of parts for quality assurance testing.
We may also use SAM testing to investigate why a particular part failed."
2
"Often, when customers come to us, they don't know what problem they have. If it is relatively
easy to solve, investing the time and expense in bringing a SAM system in-house is
unnecessary," she adds.
Contracting SAM services can also be a better match for one-time projects.
"The customer's project may be finite," said Logan. "They may only need to scan 10,000 parts,
and then the project is done. It is much more cost-effective to outsource the work in this case."
"Convenience is a big factor, too," adds Logan. "It is just simpler to give parts to a trusted
partner to evaluate. Our customers often give us a part to analyze when they can't isolate the
issue and ask us to use our expertise to determine the problem for them."
Problem solving
Newark, California-based California Brazing uses SAM testing to validate and verify processes
required by its customers and comply with American Welding Society specifications for brazing
of materials such as aluminum, stainless steel, and copper. Metals are joined together in the
brazing process by melting and flowing a filler material into a joint without melting the
workpieces.
"Brazing specifications define accepted quality requirements for analyzing internal
discontinuities using non-destructive testing," said Jeff Ager, General Manager of California
Brazing. "In our experience, ultrasound [SAM] gives us the highest resolution images, and they
are also easier to interpret than with x-ray technology."
"We use the SAM technology to validate and verify that our processes are always in spec. This
testing happens initially on a new build of a part, particularly for our aerospace and defense
customers, because of their unique requirements. These parts can be all sizes - anywhere from 1
inch by 1 inch to as large as 30 by 30 inches."
He added, "when we have potential brazing failures to investigate, we first go to Lisa and her
team at PVA TePla for testing to pinpoint exactly where it occurred. If necessary, we follow-up
with destructive testing too, but only after we've identified the precise location of the failure
using SAM."
3
Superior non-destructive testing
SAM uses the interaction of acoustic waves with the elastic properties of a specimen to image the
interior of an opaque material. A transducer, the heart of a SAM system, directs focused sound
at a small point on a target object. The sound hitting the object is either scattered, absorbed,
reflected (scattered at 180 degrees), or transmitted (scattered at 0 degrees).
By detecting the direction of scattered pulses and the "time of flight", the presence of a boundary
or object can be determined as well as its distance.
To produce an image using SAM, samples are scanned point by point and line by line. Scanning
modes range from single-layer views to tray scans and cross-sections. Multi-layer scans can
include up to 50 independent layers.
The resolution of the microscopic image depends on the acoustic frequency, material properties,
and aperture of the transducer. Transducers perform such a critical role that manufacturers like
PVA TePla design and manufacture an extensive range of different transducers used in their
contracted testing services.
The frequency of the ultrasonic signals can be increased to the GHz range, which makes it
possible to detect defects in the sub-micron range.
At PVA, their contract testing services are performed only on equipment the company
manufactures, namely the 300, 302 HD2, 500, and 501 HD2 scanners. These scanners provide
scanning ranges from 200 μm x 200 μm to 500 mm x 500 mm using transducers up to 400
MHz. PVA's proprietary transducers deliver high image resolution to evaluate the integrity of
each part.
Given the critical role it plays, in-depth knowledge of the advanced software features available is
another considerable benefit.
"SAM testing houses that purchase equipment may only be familiar with some of the features of
the software," says Logan. "As the manufacturer, we have to understand all the features and can
even request customizations if needed."
4
A matter of interpretation
The quality of the equipment and knowledge of its use is only one factor in SAM testing.
Operating a SAM system requires a trained technician and, even more importantly, experience
configuring the equipment and interpreting the scans. Setting up the scans and interpreting the
images is similar to a radiologist reading MRI scans of a medical patient.
"Imagine if you got an MRI," said Logan. "Wouldn't you want your doctor to have the clearest
image possible to make the best medical decision? When you realize that an undetected flaw can
have a catastrophic impact on a part, it's the same for quality testing too."
SAM system experts know how to work with three different imaging modes, A, B, and C.
The A mode is an X, Y, or Z point and provides information on all the echoes occurring inside of
a part. These echoes provide valuable insight into material analysis, time-of-flight imaging,
amplitude, and polarity. The A scan must be interpreted appropriately to produce an accurate B
or C scan, which is shared with the customer.
"An operator needs to interpret, focus and change the volume of the A scan as well as adjust
certain things for the image to be accurate," said Logan. "It is important to ensure that the image
does not convey something false."
According to Logan, PVA TePla typically tests products ranging from the smallest electronic
components to 50-pound aluminum parts.
"The smallest and thinnest parts increase the difficulty of interpretation because the echoes of
the interface become really tiny and close together," said Logan. "It causes an overlap of echoes,
and you end up having to adjust the frequencies used. As you go higher up in frequency, it is
more difficult to manage the transducers."
According to California Brazing's Ager, "we have thought about bringing ultrasonic testing inhouse, but to be able to do it well, we need someone who can read the images and help interpret
them. It is not easy to find people who have that depth of experience."
"We have a very good working relationship with PVA TePla," said Ager. "As a result, there is very
little interaction needed because she's so familiar with our process and the types of products we
manufacture. I think that's the biggest advantage - a deep understanding of our process."
5
"We typically get our results from PVA TePla in a few days, said Ager. "We might have a
conversation about focusing further on a particular area or a certain level, after which Lisa
would go back and focus on that."
Finding your SAM partner
When selecting a SAM partner to outsource quality testing and failure analysis, manufacturers
should consider how well the SAM equipment matches their testing needs and the breadth and
depth of experience of the testing team.
In-depth knowledge of the SAM equipment is critical to optimize image resolution. The ideal
situation is having factory-level experience in the manufacturing of acoustic microscopes and
their software development.
With a strong SAM outsourced partner, manufacturers effectively add a powerful resource to
resolve their quality testing and failure analysis challenges.
For more information on PVA TePla's contract SAM analytical services, visit
www.pvateplaamerica.com/service/sam-analytical/ or call (951) 741-5294
Featured Product
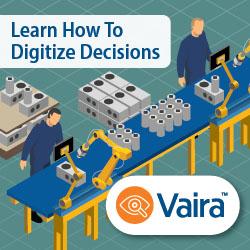
Pleora Technologies - Digitize Manual Manufacturing
Vaira™ helps manufacturers digitize, automate, and upgrade error-prone manual processes and decisions to boost productivity and increase profits by helping humans make decisions consistent, reliable, and traceable. The camera-based solution is powered by a scalable suite of shop floor-ready apps built on proven machine vision and AI expertise for frontline manufacturing operations, with two-way integration to resource planning tools to help drive continuous analysis, insight, and improvements. Start digitizing immediately, streamlining processes customized to your unique requirements and reduce errors that lead to costs, delays, and quality concerns.