AMADA WELD TECH announces Jupiter Series for Automotive Industry
Increased production and support for critical manufacturing applications for the automotive industry
AMADA WELD TECH announces the availability of the Jupiter series of modular systems for precision joining, available for laser welding, laser marking, resistance welding, micro arc welding, and hot bar bonding applications. Jupiter modular systems can be equipped with all joining process modules available from AMADA WELD TECH to provide solutions to customers. Applications for the Jupiter series for the automotive industry include for the manufacture of Laser Welding Sensors.
With the Jupiter series, customers purchase an automation platform from a global joining equipment leader and receive intensive process development support in AMADA WELD TECH application development centers. Joint early stage process development in AMADA WELD TECH labs ensures that customers receive the ideal system solution for years of high-quality production. Any welding, soldering, bonding, brazing, laser micromachining, and laser marking application can be handled by equipment in the Jupiter series.
The Jupiter modular system platform is a flexible system that comes in four sizes, so it is adaptable to specific production requirements. The stable platform enables connections of very high quality and accuracy. The modular design is configurable to fit all process components and modules. The Jupiter models feature an ergonomic system design with high quality components, designed for 24/7 continuous production. All models are equipped with a human-machine interface (HMI) with touchscreen for easy programming and standard safety features.
Control systems, based upon a programmable logic controller (PLC) or industrial PC, collect all available process parameters and process data into one control system. The data can be stored in local and remote storage areas, all engineered to seamlessly integrate with an Industry 4.0 factory concept.
Optional features for the Jupiter systems include a combustion suppression unit (CSU) for battery pack welding; a transport system with two individual belts that can be configured for a wide range of product carriers, including transfer systems; an automatic cleaning station for electrodes and thermodes; a "Not OK" bin to separate products outside the control limits from those within control limits; and a range of water cooling options. Also available are upgraded data collection and traceability functionalities, including a barcode reader or a label printer; and interfaces for a variety of robotic systems.
AMADA WELD TECH offers its expertise to all of its customers to correctly match any welding, soldering, bonding, brazing, laser micromachining and laser marking application inside the Jupiter series.
Featured Product
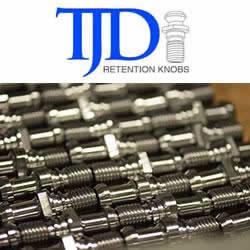