ALLOYED RECEIVES HYBRID AM RESEARCH GRANT AS PART OF CHAMPP CONSORTIUM
The Casting-Hybrid-Additive-Manufacturing-Parts-Production (CHAMPP) programme brings together a critical mass of technical and market expertise with three key partners, namely Alloyed, Brunel University London's BCAST, Gestamp and its affiliate Autotech.
(24th May 2021, Oxford and Stone, UK.) Alloyed is delighted to announce that the CHAMPP consortium, which it is a part of, has been awarded a significant grant to research, develop and test an innovative new hybrid production process that will address a number of the key limitations of additive manufacturing (AM) for the automotive sector, specifically electric vehicles (EVs). The Casting-Hybrid-Additive-Manufacturing-Parts-Production (CHAMPP) programme brings together a critical mass of technical and market expertise with three key partners, namely Alloyed, Brunel University London's BCAST, Gestamp and its affiliate Autotech.
Thus, the CHAMPP programme has been initiated to investigate a hybrid approach to the production of parts by considering the benefits of both casting and AM. The expertise of Alloyed in developing novel and innovative new alloys using its Alloy by Design (ABD®) platform for both casting and AM as well as the capabilities of its Engine® platform for increasing AM performance, together with the expertise of BCAST and Gestamp in their respective fields of casting research and world-class global manufacturing of automotive parts.
The vision is to combine the low cost-per-part capabilities of casting with the design and production flexibility of AM. In this way automotive manufacturers will be able to cast their standard components across multiple models, and subsequently use metal AM to customise those standard parts for specific variants at the volumes required.
To date, research in this area has mostly focussed on steel materials. However, while steel remains a relatively low-cost material, the complex supply chains and/or expensive new machines have been a barrier to large-scale hybridisation reaching the mainstream. Moreover, research on hybridisation using Aluminium (or alloys thereof) has been limited by traditional cast/wrought alloys which, when used with AM processes, result in poor mechanical performance. Similarly, current Aluminium alloy AM powders are generally not suited for automotive production applications as they are expensive and result in poorer mechanical properties with many defects.
The CHAMPP project aims to build on the consortium's prior alloy and hybridisation research to develop and test new Aluminium alloy(s) better suited to future automotive needs. The focus will be on developing alloys that can first be cast and then subsequently built on to produce custom/complex features using AM techniques with a compatible alloy that maintains mechanical properties and performance.
Shouxun Ji, Professor at BCAST, added: "It is exciting to be working in such a high-class consortium of companies and institutions at the cutting edge of the next-generation of casting processes in combination with additive manufacturing as part of a truly advanced hybrid technique for producing metal components. The future is exciting, and BACST is delighted to be central to the CHAMPP initiative."
Potter Phil, Innovation Project Manager at Gestamp commented; "We are proud to be working on the CHAMPP project alongside some prominent players in the metal production and AM space. Obviously for us the tie in with the potential for AM to be used alongside other solutions and innovations in the area of EVs is of pivotal concern, and we see the CHAMPP programme as vital to the furtherance of safer, lighter, more energy efficient, and more environmentally-friendly vehicles in the future."
Sajjad Amirkhanlou, Programme Director at Alloyed, commenting on the grant award, said: "We are delighted to be a part of the CHAMPP programme and bring our considerable experience and expertise to the project. It is vital for AM — if it is to fulfil its true potential — that the speed, size, and cost limitations are addressed fully. Through the CHAMPP programme we will tackle these issues head-on by taking a multi-disciplinary approach and combining AM with an efficient and optimised casting process."
* MarketsAndMarkets.com
ABOUT ALLOYED
Alloyed is uniquely positioned to offer a more comprehensive stack of technologies to its clients to support their metal component production activities, from material identification, through process development, performance optimization and pilot production. These technologies can be applied to client projects individually or in combination to maximize opportunities.
ABOUT BCAST
Brunel University London (BUL; Academic): Brunel teaches ~13,000 students from \>100 countries. The Brunel Centre for Advanced Solidification Technology (BCAST) is the UK's largest physical metallurgy and light metals research group.
ABOUT GESTAMP
Gestamp are a global tier1 automotive full service supplier focussed on the design, development and manufacture of safer and lighter vehicles, reducing energy consumption and environmental impact. Autotech is the R&D subsidiary of Gestamp focussed on pre-production activities including the design, development and project management for customer product development. This group also consider differentiating Gestamp from our competition through innovation, to bring alternative product and process projects, adding value to both our clients and global production plants.
Featured Product
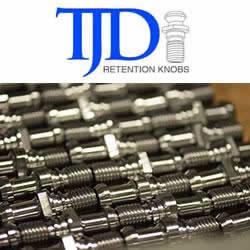