Brown Machine Group Announces Industry-Leading C-RUSH System for Reducing Manual Labor and Increased Productivity in Paper Cup Manufacturing
SMART-DOLA™ feature enables production of unlimited number of fixtures
BEAVERTON, Michigan - Brown Machine Group (BMG) is pleased to announce the aXatronics C-RUSH System, designed for use in paper cup manufacturing applications. The first of its kind to automatically remove sidewalls, or Blanks, from high-speed, vertical die-cutters and robotically place them into work-in-progress containers, the C-RUSH System significantly reduces manual labor and improves die-cutter productivity. C-RUSH is equipped with SMART-DOLA™ - a new patent pending die-cutter output lane assembly (DOLA) fixture that dramatically improves overall system throughput.
Designed by aXatronics and manufactured in the Nalle Automation Systems (NAS) facility in Knoxville TN, C-RUSH allows the operator to interface with the die-cutter by pausing and resuming the robotic pick and place automation. No robotic experience or a high level of training is required to operate the system, which can handle up to two million 21-ounce sidewalls per day - the equivalent of more than 20 tons of paper. Designed for 24/7 operation, C-RUSH makes die-cutters more productive by reducing die-cutter downtime or production slowdown due to personnel fatigue.
A single uniquely designed robotic end-of-arm-tool (EOAT) handles cup sizes from 12 to 30 ounces, automatically unloading a multilane DOLA before placing each stack of sidewalls into a tote. Lane handling and stacking configuration includes interleaving tier sheets and stacking patterns engineered to each cup's specifications. The C-RUSH System automatically changes its configuration with no operator intervention when changing dies.
The new SMART-DOLA™ fixture enables production of an unlimited number of different cup sizes with no pre-programming of the individual robot controller required. The SMART-DOLA™ contains all pertinent ‘recipe' data for the specific size and shape of the sidewall it is designed to handle. This recipe data is automatically uploaded into the robot controller whenever the fixture is mounted onto the die-cutter, eliminating the need for specialized personnel to load the recipe data into each robot individually. Using laser distance measuring sensors, the SMART-DOLA™ can slow down the die-cutter before it becomes full - without requiring an operator to return the die-cutter back to high speed functioning. This dramatically improves the overall system throughput.
Operator safeguards provide CAT 3 safety with fencing and personnel laser-based area sensors. Other features include automatic recovery after error conditions and acknowledge of an E-STOP. In addition, the conveyor system is designed with automated guided vehicle (AGV) capabilities.
The C-RUSH is installed and supported by Nalle Automation Systems, known for outstanding customer support.
For more information about how the C-RUSH system can meet application-specific requirements and to learn how the robot components can be sized to meet higher volumes or heavier materials, visit https://brownmachinegroup.com/machine/axatronics-c-rush-system/.
About Brown Machine Group
Brown Machine Group in Beaverton, MI, is a global leader in thermoforming technology and innovation with high-quality product lines manufactured by Brown Machine, Lyle Industries, Nalle Automation Systems, Freeman Company and aXatronics. It designs and manufactures a complete line of continuous and cut-sheet thermoforming equipment, tooling, automation, robotic systems and provides related services including retrofit upgrades, prototyping, process optimization and technical support. Its equipment has been "Made in the USA" since 1952 and it has thermoforming systems operating in over 65 countries worldwide in virtually every industry. Visit www.brownmachinegroup.com for more information.
Featured Product
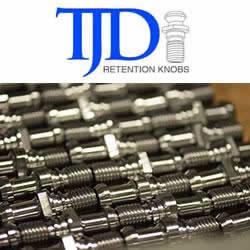