VELO3D Raises $28 Million in Series D Funding Round, Paving the Way for Product Expansion
Product portfolio will expand to deliver more machine options and compatible alloys to 3D print mission-critical metal parts for industrial applications
CAMPBELL, Calif., April 28, 2020 - Digital manufacturing innovator VELO3D announced today that it has raised $28 million in a Series D funding round. New investors Piva and TNSC joined the round, along with existing investors Bessemer Venture Partners, Playground, and Khosla Ventures. This brings VELO3D's total funding to $138 million.
"With the VELO3D integrated solution of Flow™ advanced pre-print software, Sapphire™ printer, and Assure™ quality management software, companies can finally break free of the constraints of existing metal additive manufacturing processes," states Benny Buller, Founder and CEO of VELO3D. "Customers in industries such as aerospace, oil & gas, and power generation are now able to achieve part quality for their mission-critical applications with performance levels that weren't possible before with 3D metal printing."
VELO3D plans to use the new capital to expand its product portfolio to include more machine options, compatible alloys, and enhanced software and hardware capabilities. The company anticipates that the injection of fresh capital will help them reach sustainable profitability by mid-2022.
Piva is the largest investor in the new round and has a strong heritage in industrial markets, as they are backed by Malaysia-based PETRONAS, one of the world's largest energy companies.
"VELO3D is revolutionizing the way we think about advanced manufacturing today," said Ricardo Angel, CEO and Managing Partner at Piva. "We have been impressed by Benny, the team and their breakthrough technology that will have a significant impact on the efficient design and manufacturing of more complex components, previously unattainable, with clear commercial traction already in the aerospace and aviation markets. VELO3D will lead a new wave of more resilient, distributed manufacturing capabilities for its most critical components, which the world will need to ensure local product availability and timeliness, while mitigating potential future worldwide disruptions."
Founded in 2015, VELO3D operated in stealth mode for the first 4 years, then announced availability of the Sapphire printer in 2019. In that first year of commercialization, VELO3D generated nearly $30 million in sales and gained seven new customers, many of which have placed repeat orders. VELO3D now has a global customer footprint that includes Japan, Korea, and Australia.
# # #
About Piva
Piva invests in the leading people and companies solving the world's greatest industrial and energy problems with breakthrough technologies and new, innovative ways of doing business. Backed by a global Fortune 500 energy company, Piva is a San Francisco based venture capital firm with an accomplished and connected team investing in early to growth-stage companies around the world. For more information: Piva.vc, LinkedIn or Medium
About VELO3D
VELO3D empowers companies to manufacture anything. Bringing together an integrated solution of software, hardware, and process-control innovation, Velo3D introduced the first SupportFree capability for 3D metal printing. This enables unlimited design innovation by reducing the need for support structures in metal additive manufacturing. The company's Sapphire® system is built with a semiconductor mindset on quality assurance, ensuring repeatability and dependability throughout serial manufacturing. Headquartered in Silicon Valley, California, Velo3D helps companies deliver immediate business impact by making the impossible, possible. To learn more: www.VELO3D.com
Featured Product
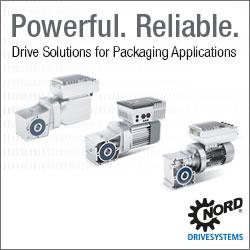
NORD Delivers Powerful, Reliable Drive Solutions for Demanding Packaging Applications
When you need quality, flexibility and high efficiency, NORD has you covered with complete drive solutions for primary and secondary packaging, end-of-line packaging, and higher-level applications. NORD supports you through the entire life cycle of your drive systems with pre-sales engineering support, online tools, and a global service network. Drive systems for both vertically and horizontally networked technology with all the options for sensor incorporation and integration into the higher-level control system.