CoVent-19 Challenge Asks Millions of Designers and Engineers to Respond to the Ventilator Crisis
-Global, open innovation initiative via Stratasys GrabCAD platform designed to help develop a rapidly deployable mechanical ventilator -Challenge by Boston non-profit leaders and anesthesiology resident physicians launches now
A dozen Boston area anesthesiology residents have launched an eight-week hackathon hosted on GrabCAD.com to design a rapidly deployable, minimum viable mechanical ventilator for patients with COVID-19-related ventilator-dependent lung injury. The CoVent-19 Challenge is open to teams and individuals anywhere, and finalists will work directly with Stratasys 3D printing experts and the CoVent-19 Challenge team to turn their designs into prototypes for testing.
"As anesthesiologists at Massachusetts General Hospital, we are experts at using ventilators to care for critically ill patients, so it was natural for us to feel an immediate calling to do something about the ventilator shortage," said Dr. Richard Boyer, founder and director of the CoVent-19 Challenge. "We've been watching as countries around the world struggle with providing invasive mechanical ventilation to all who need it. Despite the important efforts by ventilator manufacturers to ramp up their own production, there's a need for a solution particularly for areas where standard mechanical ventilators may be hard to obtain."
Current sponsors include Stratasys Ltd. (NASDAQ: SSYS), Ximedica, Valispace, HackFund, and Yelling Mule. Stratasys is providing the top three winners with a total of $10,000 in credits they can use for 3D-printed parts from Stratasys Direct Manufacturing.
According to one Chinese medical device maker, the demand for ventilators due to COVID-19 is at least ten times what's available in hospitals around the world. In Italy, doctors are being forced to triage patients due to a severe ventilator shortage. In the U.S., current ventilation capacity is about 170,000 patients, while some projections show nearly one million patients may need mechanical ventilation.
The challenge will run on Stratasys' GrabCAD Challenge site beginning April 1. This site reaches a community of more than 7 million professional designers, engineers, manufacturers, and students, and anyone can participate. The general entry round, focused on initial designs, will run for four weeks, with a panel of judges, including Stratasys Founder and Chief Innovation Officer Scott Crump, selecting up to 20 finalists. Evaluation by judges of minimum-viable ventilator designs will assess safety, reliability, and manufacturability, while minimizing cost and complex software and electronics.
Finalist teams will work with medical and technical experts through a four-week invitation-only round to develop and test functional prototypes. Stratasys application engineers will provide 3D printing consulting and services to the finalists.
The CoVent-19 Challenge team is working with private and public sector partners to be able to expedite U.S. government approval of a winning design. The team has secured experts in regulatory measures and safety testing to ensure all products meet U.S. and international standards.
For more information on how Stratasys is responding to the COVID-19 pandemic and how others can help, visit www.stratasys.com/covid-19.
Stratasys is a global leader in additive manufacturing or 3D printing technology and is the manufacturer of FDM®, PolyJet™, and stereolithography 3D printers. The company's technologies are used to create prototypes, manufacturing tools, and production parts for industries, including aerospace, automotive, healthcare, consumer products and education. For more than 30 years, Stratasys products have helped manufacturers reduce product-development time, cost, and time-to-market, as well as reduce or eliminate tooling costs and improve product quality. The Stratasys 3D printing ecosystem of solutions and expertise includes 3D printers, materials, software, expert services, and on-demand parts production. Online at: www.stratasys.com.
Featured Product
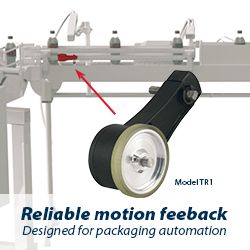