3D Hubs launches manufacturing fund in fight against COVID-19
Global online manufacturing platform, 3D Hubs, launches fund to manufacture critical parts for COVID-19 initiatives.
As the coronavirus continues to spread, medical facilities and hospitals are under an increasing amount of strain, often lacking critical medical equipment needed to effectively fight COVID-19. All over the world, initiatives have been launched to help with the rapid development and production of such equipment, but many are struggling to access the funds and manufacturing capacity required to act quickly.
In order to increase accessibility to this crucial equipment, 3D Hubs has launched the COVID-19 Manufacturing Fund, connecting these projects with both the funds and means of production they need to rapidly produce vital equipment such as protective masks and ventilator parts. Thanks to its global network of manufacturing partners, 3D Hubs is in a unique position to offer such projects access to a virtually unlimited manufacturing capacity that is able to sustain the rapid production of parts. Providing access to various manufacturing technologies including 3D printing, injection molding and CNC machining, this capacity and speed is vital to producing parts in these times of crisis.
In less than 12 hours after launching, the fund has raised over $18,000. 3D Hubs has so far partnered with Make4Covid and The University of Denver to manufacture up to 10,000 protective face shields for hospitals in Denver. Key components for the Prusa face shield RC2 are being produced, to be used ‘in the field' in hospitals that are facing shortages in the midst of this deepening crisis. 3D Hubs has also partnered with Project Open Air to work on ventilator splitters to increase the capacity of existing ventilators.
Co-founder and CPO of 3D Hubs, Brian Garret comments:
"Thousands of designers and engineers around the world are stepping up to design parts for life-saving applications. We want to make sure these parts reach those in need as soon as possible. By launching this fund, and committing our global manufacturing capacity, we're accelerating these initiatives as fast as we can."
About 3D Hubs:
3D Hubs is an online manufacturing platform that provides engineers with on-demand access to a global network of manufacturing partners. Users can easily upload their design, instantly receive a quote, and start production at the click of a button.
Founded in Amsterdam in 2013, 3D Hubs has raised over US$30 million and produced more than 4 million parts, using various manufacturing technologies, including CNC machining, 3D printing, injection molding and sheet metal fabrication.
Featured Product
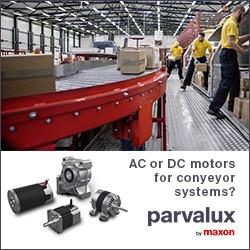
Strain Wave Gearheads by maxon - Highly precise, compact, and efficient.
Strain wave gearheads are ideal for use in applications requiring precision motion control and high torque transmission in a compact design. maxon strain wave gearheads are a specialized type of gearhead where precision and compact design are crucial. This type of gearhead is often used in applications in a confined space. With their advanced gear tooth design, maxon's strain wave gearheads provide high efficiency and good back drivability. Typical applications include:
Robotics, Aerospace, Medical technology and Optical systems
.