Fastems New Software Domain Can Plan, Control and Monitor Even Non-Automated Equipment – Standing Alone or in a Cell
Fastems Manufacturing Management Software (MMS) has proven to be a powerful solution for planning, forecasting, controlling, visualizing, and monitoring automated manufacturing processes. The new MMS Domain, Work Cell Operations (WCO), now makes it possible to include all manual production tasks, work cells, and stand-alone machines in the IT-supported planning, control and monitoring of production.
Fastems Manufacturing Management Software (MMS) has proven to be a powerful solution for planning, forecasting, controlling, visualizing, and monitoring automated manufacturing processes. The new MMS Domain, Work Cell Operations (WCO), now makes it possible to include all manual production tasks, work cells, and stand-alone machines in the IT-supported planning, control and monitoring of production. For this purpose, the solution can be used either separately for machines or manual workstations or in combination with an automated pallet and/or workpiece handling system.
"MMS Work Cell Operations, or WCO, brings the unique Fastems features like automatic, predictive scheduling and full transparency of manufacturing operations, for stand-alone machine tools and other manually operated workstations," said Tomi Kankainen, CDO and VP of Fastems MOM Software business.
WCO promises a whole range of advantages for work preparation, shop floor and controlling, including time-optimized, automated production planning that takes the entire process chain, managed by WCO, into account, along with automatic detailed planning that allows production with smaller part buffers, among other parameters. In particular, employees on the shop floor have a clear view of what tools and materials are needed and which resources may be missing. Additionally, employees always know exactly which tasks are due in a shift as they are provided with clear, prioritized work lists. These various triggers improve the timeliness of resource ordering and transfer logistics so that tools and materials are always delivered on time to the machines, cells, or FMSs. If permitted, the employee at a machine or work cell also has access to all important production documents and instructions via the WCO module. Against this background, WCO also offers greater transparency with regard to current information on manufacturing capacities, production output, and order status.
These few examples illustrate the enormous potential of WCO, which has a direct positive influence on the key parameters for highly efficient overall production, including higher utilization of production capacities, increased production output, shorter lead times, higher delivery reliability (e.g., through automatic planning based on real production orders, due dates and quantities) and less WIP (Work-in-Progress). The result of detailed planning and seamless transfer of information will translate to higher production quality.
Another compelling aspect of the Fastems new WCO software is that it provides all the powerful tools needed to combine automated and non-automated production steps in a uniform production management system. Functions such as deburring and parts washing can now be incorporated into cells and monitored right along with CNC machine tools and the automation equipment integrated into the cell or FMS.
The solution is therefore a decisive step towards full integrated manufacturing management often referred to as MOM (Manufacturing Operations Management), enabling continuous improvement of all production processes through the digitalization of manufacturing workflows.
As with all of Fastems products and services, WCO is offered at several levels of engagement and application for the comfort and practicality of a customer's operations and goals. Fastems automation equipment and software can be installed in phases, with each stage growing in capability and functionality.
For more information, visit, www.fastems.com, or call toll-free 866-702-0611.
# # #
About Fastems
Founded in 1901, Fastems delivers intelligent factory automation solutions that help metalworking manufacturers to increase their productivity. Their provisions include consulting services in the field of material handling up to flexible manufacturing systems, robot-based automation solutions, software for production control, portal and gantry systems as well as a comprehensive range of services. The capacity usage of machine tools can be increased with these solutions, and the processes can be optimized. With the help of the intelligent software MMS production and tool management are efficiently planned, forecasted, controlled, visualized and monitored. Due to the openness to different systems and interfaces, the opportunities offered by new technologies, digitalization and integration are consistently implemented in customer-oriented software and hardware solutions. Fastems has its headquarters in Tampere (Finland). With manufacturing facilities in Finland and Germany as well as a global sales and service organization, the company employs approximately 450 people.
Featured Product
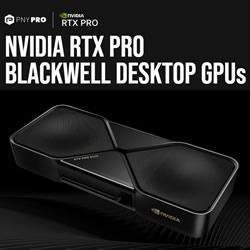