Abrasive Nylon Wheel Brushes Provide Deburring for Extremely Hard Metal Parts
When an application calls for surface finishing, cleaning, polishing, deburring, edge blending or removal of paint, rust or other contamination, a wheel brush is often the ideal solution
When an application calls for surface finishing, cleaning, polishing, deburring, edge blending or removal of paint, rust or other contamination, a wheel brush is often the ideal solution. A type of power brush, wheel brushes are motor-driven and may feature an arbor hole or keyway that supports their use with grinding equipment or CNC machinery.
Wheel brushes are circular in shape with uniform distribution of the fill materials extending radially from the center core to the periphery. When metal wire filaments are used, they are excellent tools for light deburring, edge blending and general surface finishing. The brushing action occurs at the edge or face of the tool on machined parts such as steel shafts, gears, turbine blades, or extrusion cut-offs.
However, when harder materials are involved, wire filaments can break off, or deform - even if crimped. Although knotted wire options are available for more aggressive deburring, for today's hardened steels and alloys even this type of wheel brush is not sufficient.
Instead, for the most aggressive deburring or surface finishing the solution is a wheel brush that utilizes abrasive nylon filaments made of silicon carbide. Taking it one step further, diamond grit can be used for the hardest metals and alloys in use today.
The construction of these composite hub radial wheel brushes, as they are called, provides a long-lasting wheel with less filament breakage and superior performance.
As an example, Los Angeles-based Brush Research Manufacturing is one manufacturer of
abrasive nylon wheel brushes for the deburring for extremely hard metal parts. The company
manufactures a wide array of wheel, cup and end brushes in a variety of sizes, filaments and grits.
Such an abrasive nylon wheel brush can easily get into slots, push the burrs out and remove them.
The abrasive-filled nylon filaments are set into molded cores, allowing higher filament densities and putting more cutting tips at the point of attack. In addition, the filaments are extremely durable and self-sharpening, providing excellent performance and wear life. As the brushes come in contact with the work surface, the filament grit wears off, exposing new cutting particles. In that manner the brush continues to be sharp even after repeated use.
In addition, unlike the bristles of metal brushes the abrasive nylon fibers are not prone to deforming or breaking off like wire brushes.
As a tool, an abrasive nylon wheel brush can be automated on CNC equipment or offline as a secondary deburring operation.
While operators may be unfamiliar with this new option, when deburring extremely hard metal parts is required, they will be well served to look to abrasive nylon wheel brushes.
For more information, contact Brush Research Manufacturing, Brush Research Mfg. Co., Inc., 4642 Floral Drive, Los Angeles, CA 90022; Phone: (323) 261-2193; Fax: (323) 268-6587; email: info@brushresearch.com or visit the web site: www.brushresearch.com.
Featured Product
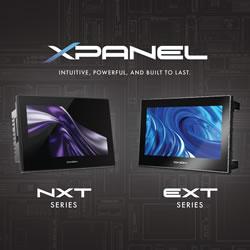
CIMON Xpanel eXT & nXT Series HMI
Introducing the Xpanel eXT and nXT series, advanced industrial HMI solutions that set a new standard for performance and usability. Utilizing our brand new Canvas HMI software for project creation, the Xpanel eXT and nXT series deliver a seamless and efficient user experience. They combine industrial-grade touch technology, powerful embedded OS hardware with a quad-core CPU, and an easy-to-use runtime platform. The Xpanel eXT and nXT series are specifically designed to optimize and streamline industrial operations, enhancing your HMI experience.