Innovative laser systems provide a boost to microelectronics manufacturing
LASYS 2020: Laser depaneling is cost-effective and very clean/Ideal for high-end electronics in medical and aerospace technology
Laser micro processing plays a crucial role in the electronics and semiconductor industries, which is also reflected in current market data. "While the global market for laser systems for material processing reached a volume of almost €17 billion in 2018," says Dr Arnold Mayer, President of Optech Consulting, "laser systems for microelectronics manufacturing accounted for a quarter of this." However, he points out that laser-based micro-lithography systems are not taken into account in this figure. "These systems represent around €10 billion in turnover in 2018," the analyst adds.
"The main topic in laser micro processing remains its gradual miniaturisation. Even more complex structures, finer details and results which are precise on the micro scale are to be achieved in the shortest possible processing time," says Thomas Nether, Senior Vice President of LaserMicronics Micromachining Services at LPKF.
There is a steady trend in semiconductor components and electronics devices towards accommodating an increasing number of functions in a smaller space. For instance, manufacturers of TVs, notebooks, smartphones, tablets, kitchen appliances, cars and the like are fitting their products with more and more sensors. Many manufacturing methods in electronics would now be inconceivable without laser technology. "Lasers improve the throughput and the quality in display production, they allow LEDs to be produced cost effectively, they drill, notch, cut and structure rigid and flexible circuit board materials, ceramic substrates and semiconductor wafers in an efficient way," mentions Martin Paster, Head of Sales and Marketing at InnoLas Photonics, as some of the benefits.
Manufacturing solutions are in demand
Visitors to the LAYS international trade fair, which will take place for the seventh time from 16-18 June 2020 in the Stuttgart trade fair halls, will be able to explore how laser systems can contribute to electronics and semiconductor manufacturing and which innovations can make their work even more cost-effective. LAYS is considered to be unique among trade fairs as its concept is tailored to laser material processing and is applicable to a range of sectors and materials. The exhibition is intended for a wide variety of industries, such as automotive, mechanical engineering, electronics, optical, plant and apparatus construction, metalworking and metal processing, medical technology, plastics and toolmaking as well as mouldmaking. An extensive accompanying programme with exclusive talks from the fields of research and practice will run alongside the fair. This information and communication platform may also be of use to semiconductor and electronics manufacturing. If you are looking for productive laser solutions for your manufacturing, LASYS 2020 is exactly the right place for you.
Cost-effective laser depaneling of circuit boards
Electronic circuit boards, which are used in all electronic devices, are now no longer produced individually, but rather with several on a large board in order to reduce costs. At the end of the manufacturing process, the individual circuit boards must then be cut out, which is known as blanking or depaneling. "Previously, milling machines were mainly used to do this," says Martin Paster, "because they are quick and cheap to operate." However, the expert for InnoLas Photonics explains there are major disadvantages when milling is compared with the laser process. "Dust that forms during milling may result in the product having reliability issues. The tool vibrates, which can result in soldering points being damaged. Valuable space is wasted by using very wide cuts and due to the large cutting distance from components that is necessary. During milling, thin circuit boards and narrow contours tend to vibrate or even break. This is why this method of processing has design limitations," Paster adds. In contrast, depaneling using lasers provides considerable benefits thanks to its use of contact-free and precise laser cutting technology. Paster explains that previous laser systems were not ideal because they either heated the material too strongly or were too slow and, therefore, were not cost-effective. "The launch of the BLIZZ laser series by InnoLas Photonics means that there is now a suitable laser for this application. What sets this laser apart is its high pulse energy of one millijoule at a wavelength of 532 nanometres, combined with a very short pulse duration of under 15 nanoseconds and a high average power of 40 watts," says the Head of Marketing. Paster adds that this enables the circuit boards to be laser cut in a non-contact, quick and dust-free manner while maintaining the same excellent quality. "Especially for thin substrates," he continues, "our laser is vastly superior to conventional milling when it comes to cutting circuit boards. The laser is very low-maintenance and therefore highly cost-effective in industrial applications."
Maximum cleanliness for high-end electronics for medical technology and the aerospace industry
"The demand for maximum technical cleanliness increases significantly when using the depaneling process," confirms Thomas Nether from LPKF. According to the expert, the advantages inherent to laser cutting technology - such as geometric freedom, minimal mechanical component load and narrow cutting channels - can be further enhanced when depaneling with ultra-short pulse (USP) lasers and using LPKF's CleanCut technology. "This means that the cutting edges can be generated without any carbonisation. This is particularly important if, for example, the printed circuit boards in high-end electronics are used in the aerospace industry or medical technology," explains Nether. In addition to the need for smaller and smaller masses, medical implant technology and the broad field of sensor technology require electronic assemblies which are completely reliable. "The requirement for clean manufacturing should not be underestimated amongst the competition. The more steps that are taken in the process chain regarding technical cleanliness, the quicker and more reliable the results will be," the expert from LPKF points out.
3D laser micro-welding for various applications
As components in the electronics industry are becoming increasingly miniaturised, the challenges faced by lasers as a high-precision tool are growing. For instance, machine manufacturer Schüssler Technik is overcoming new challenges with respect to laser micro-welding. The company has created an innovative laser CNC processing centre for 3D laser micro-welding. Thanks to highly precise axis movements, intricate components can effortlessly be joined in a wide variety of positions (5+2-axis). This means, for instance, that components such as HALL sensors can be connected to condensers or that copper rings can be welded for engines. "Setting machines up with the support of cameras
optimises the processing time. The axis system's high-precision quality drives provide a perfect weld seam. This means that no finishing is required and process costs are saved," says Michael Bürger, Sales and Marketing Manager at Schüssler Technik. The modular system allows different optics and laser types to be combined.
Thanks to the CAD/CAM system, it is also possible to perform free-form micro-welding tasks. "This allows us to adjust to every application - and, needless to say, to other industries," adds Bürger.
Precision laser work on sensitive sensors for measuring technology
The miniaturisation of electronic components often has inconvenient side effects, such as increased heat generation, which can damage sensitive electronic components. Almost all electric and electronic materials can therefore be fed into GFH's GL series of laser micro processing systems using USP laser beam cooling channels. "Many components in testing and measuring technology are also decreasing in size while increasing their functional density - for example, this is the case with sensors which measure particularly low tolerance ranges," says Florian Lendner, CEO of GFH. "When manufacturing these sensitive parts, our laser micro processing systems perform tasks to remove material as well as carrying out precision drilling. Almost any material can be processed using machines from the GL range," he adds.
Thomas Nether from LPKF believes that the growing variety of materials processed poses another challenge to laser micro processing. "We currently have a growing demand for laser processing a wide range of materials. A particularly important area of application for us is cutting various ceramics, as well as thin sheets and glass fibres. This is where USP laser systems are almost indispensable because they operate with precision and high processing speed and are gentle on the material," adds Nether.
Forward-looking: Optimised separation and joining of semiconductors
To ensure that future needs are met, experts at the laser institute at the Hochschule Mittweida University of Applied Sciences (LHM) are researching how existing laser production technologies can be optimised.
An important process within the semiconductor industry is the defined separation of semiconductor wafers. "Stealth dicing" is considered to be state-of-the-art technology. This process involves producing laser-based microcracks within the material cross-section. At these cracks, the semiconductor substrate is separated in a defined way. "Innovative laser sources provide the opportunity to continue to optimise this type of material processing," says Prof Alexander Horn, Head of the "Dynamics of Ultrafast Selective Laser Processes" Research Group at the LHM. "We use USP lasers with mid-IR laser beams (with wavelengths of 3-10 micrometres) to generate predetermined breaking points. However, as the inorganic semiconductors are transparent to the wavelength of this laser light, this type of processing is only based on non-linear processes within very small volumes. The advantage of this process is that it reduces the thermal load on the processed material. This allows the wafer manufacturers to continue to increase the packing density," Prof Horn continues. He says that this process also means that semiconductor materials can be joined together. "Thanks to our research at the LHM, we are preparing to take this process into industry," says Horn. For example, he believes that in the future there will still be a need to increase productivity in laser micro processing. "For this reason, at the LHM we are working on fast beam deflection systems, including when used with high-power USP lasers. Conventional galvanometer scanners currently reach speeds of up to 15 m/s. In contrast, the polygon scanners developed at the LHM reach deflection speeds of more than 1 km/s. That's how we'll achieve pulse speeds which are perfect for the semiconductor industry in the future," adds Horn.
Info box
Laser depaneling has more benefits than milling. Compared to milling machines, laser production systems offer considerable advantages when separating circuit boards (depaneling):
• Contact-free and precise laser cutting technology
• Dust-free process, therefore bringing high product reliability
• No design limitations
• No damage to soldering points due to vibrations
• No vibrations or breaks for thin substrates
• Low-maintenance and therefore very cost-effective in industrial applications
• Complete circuit board: Significant savings in terms of space and materials
• Cost-effective and saves resources
About LASYS
LASYS will be taking place from 16 to 18 June 2020 at Messe Stuttgart and, as the only international trade fair to do so, will continue to focus on system solutions for laser material processing. Since the start of the trade fair in 2008, it has successfully established itself as a user platform for laser system solutions and applications. LASYS covers all industries and materials, and is primarily aimed at decision-makers from international industry.
Other industry fairs taking place at the same time will provide LASYS visitors with additional information. These include the Global Automotive Components and Suppliers Expo, the Engine Expo, the Automotive Interiors Expo, the Automotive Testing Expo, Surface Technology Germany and CastForge - the Trade Fair for Castings and Forgings with Processing.
Further information is available online at: www.lasys-messe.de
The text file, trade fair photos from LASYS and trade fair logos can be downloaded online at: www.lasys-messe.de/presse
Follow us: www.twitter.com/Lasys_TradeFair
Featured Product
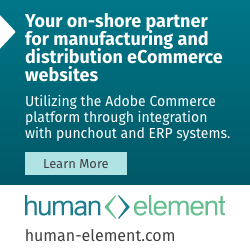