Breaking the Mold on Cooling Tower Solutions
Unique long-term benefits of advanced HDPE cooling tower technology are causing industry to rethink selection criteria
While cooling towers have been a mainstay in many heavy industrial cooling applications for decades, according to industry analytics, the adoption of the technology is significantly increasing for a number of reasons. Most notably longer average lifespan, lower maintenance, and significant energy savings over alternative cooling options.
Some of the largest industrial cooling towers are located at facilities such as oil refineries, chemical plants and paper mills. These heavy industrial operations traditionally required cooling towers that were the size of buildings and constructed on-site. However, those towers share many of the same drawbacks that plague metal-clad cooling tower designs, including those used for more modest process cooling applications.
"The biggest problem with metal-clad cooling towers - regardless of their size - is that they're highly susceptible to corrosion which requires considerable maintenance," says Ben Stolt, Branch Manager at Tencarva Machinery. "This means you're going to have to deal with a lot of expensive, unplanned downtime."
Tencarva Machinery is a distributor of liquid process equipment and custom engineered systems, most of which incorporate pumping packages and electrical controls.
The nearly continuous cycle of maintenance and repair or replacement of metal-clad cooling towers is leading many facility managers to look for alternative designs that are ‘breaking the mold' on how they approach their process cooling requirements.
Stolt explains that many times the best solution is a cooling tower constructed of high-density polyethylene (HDPE). Offering unique, long-term benefits engineered plastic greatly reduces the need for maintenance and can also cut operational costs. He notes that many of the original HDPE towers installed back in the late 1970s, are still in operation today.
However, until the innovation of modular HDPE cooling tower designs, heavy industrial operations were typically stuck with metal as the only option.
"With cooling capacity of up to 2,500 tons per cluster, the adoption of modular HDPE towers is accelerating in heavy industrial operations, and without all the on-site construction costs and delays," Stolt says. "It's a game-changer."
HDPE cooling towers also feature advanced corrosion-resistant materials, low maintenance requirements, improved energy efficiency, and longer-term warranty protection.
Furthermore, the savings on installation time and money using factory pre-assembled cooling towers is likely to present another significant savings. "Compared with the construction effort required to build a large structure in the field, installing the HDPE type of cooling tower is a walk in the park," Stolt adds. "In fact, we just installed a 5-cell modular tower design in 2 days!"
Sizing up the situation
Recently, this scenario played itself out when Tencarva-Knoxville proposed a new cooling tower system for a major paper manufacturing operation located in eastern Tennessee. The mill was converting substantial capacity from the production of one type of paper to another, and decided that an original cooling tower structure, which was built in the 1960s (and completely rebuilt 3 times since), must be replaced.
Gerald Kennedy, project engineer on the paper mill replacement program, said that like other manufacturers, his company management was inclined to use the basic point-of-failure philosophy servicing the cooling towers on an as-needed basis, even though that led to repeated operational interruptions.
"It was a bit frustrating to see that management was inclined to replace the existing tower structure with pretty much the same thing," Kennedy says. "I thought there had to be a better technology that could handle our applications more efficiently."
After researching all options, the engineering team decided to replace the existing system - the oldest cooling tower of its type in the world still in service - with a modular HDPE model offering highly efficient performance as well as savings on maintenance and energy.
Developed by Delta Cooling Towers (www.deltacooling.com), these HDPE engineered plastic units were designed to solve corrosion problems that plague metal towers. The corrosion can be the result of water treatment chemicals, soft water, or simply factors such as salt air or caustic industrial gasses.
Believing an HDPE cooling tower could obviate the corrosion problem and provide other benefits, Kennedy consulted with Ben Stolt to determine which tower design would provide an optimum long-term solution.
A modular solution
"We ultimately arrived at a configuration of Delta's TM Series towers," Stolt says.
The TM Series is a modular system of towers made up of cells that can be nested together using the same platforms, and can be placed on the ground or on the rooftop of a building.
The primary replacement system was composed of eight cells, five of which were devoted to the "dirty loop," which cooled vacuum pumps that potentially contained paper residue. The other three cells cooled the "clean loop," which serviced heat exchangers and other uncontaminated applications.
The flow rate on the clean loop is 3,600 gallons per minute, with 95 degrees in and 85 degrees out of the clean cooling tower structure. The dirty loop flow rate is 1,800 gallons per minute, with temperatures of 115 degrees in and 85 degrees out. In addition, the dirty loop cooling tower has a special "splash" heat transfer fill inside the tower to prevent paper residue from fouling typical clean water fill.
Important ‘plus' benefits
Kennedy notes that another advantage they saw in the modular design of the Delta TM Series towers is the potentially to expand cooling capacity whenever necessary by simply adding one or more additional tower cells.
The new cooling towers feature an air moving system powered by direct variable-frequency drive motors. "The increased efficiency of these drives, which eliminate the friction loss of gears and pulleys, translates into energy savings by as much as 70%," Kennedy explains.
"Also, you don't need service personnel climbing the towers to lubricate gearboxes, which means fewer maintenance expenses as well, concludes Kennedy. "And the 20-year standard warranty was certainly a ‘wow' factor for us."
For more information, contact Delta Cooling Towers, Inc.; (800) 289.3358; email: sales@deltacooling.com; or visit the website: www.deltacooling.com
Featured Product
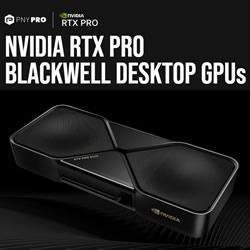
NVIDIA RTX PRO™ BLACKWELL DESKTOP GPUs N
NVIDIA RTX PRO™ - Built for Professionals - NVIDIA RTX PRO Blackwell Desktop GPUs feature the latest breakthroughs in AI, ray tracing, and neural rendering technology to power the most innovative workflows in design, engineering, and beyond.