Propelling the field of small sats forward with 3d printing and Windform® composite materials
CRP Technology and LISA UPEC collaborated to create the 3D printed structure of a nano-satellite that is a 3U CubeSat formfactor. Thanks to selective laser sintering technology and composite material WIndform XT 2.0, several critical issues and strict space requirements have been overcome.
Space industry has been revolutionized by the ever-increasing production and launch of small satellites.
Although much still must be done to reach an extensive use of additive manufacturing for Space applications, CRP Technology's built a considerable experience supplying cutting-edge solutions for space key industry leaders.
A clear and remarkable example comes from the experience with the Laboratoire InterUniversitaire des Système Atmosphérique (LISA) of Universite Paris-est Creteil (UPEC) on the construction of a nano-satellite that is a 3U CubeSat formfactor.
The project was carried by students under CNES and Space Campus University supervision.
The goal was to develop a demonstrator that can be flight-ready in Low Earth Orbit.
CubeSat structure is critical as it has to fulfill the launch-pad (P-Pod) requirements in terms of dimension, flatness and roughness, but also for outgassing, UV resistance, thermal expansion, and general space constraints.
Plus, if it breaks, or stays stuck in the P-pod launcher, the mission is over.
Professional 3D printing, combined with Windform® XT 2.0 Carbon-composite material, proved to be the best choice: the 3D printed part has successfully passed the control and testing criteria, and has fully complied with the requests and LISA's standards.
LISA and CNES performed many tests on the 3D printed nano-satellite structure such as vibration tests and thermal-vacuum tests.
The project manager at LISA, commented, "We are more than satisfied with selective laser sintering technique and consider Windform® XT 2.0 one of the disruptive revolutions in the small satellites arena. We do hope additive manufacturing will be intensively using in space application."
Featured Product
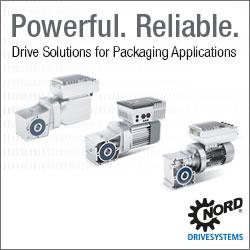
NORD Delivers Powerful, Reliable Drive Solutions for Demanding Packaging Applications
When you need quality, flexibility and high efficiency, NORD has you covered with complete drive solutions for primary and secondary packaging, end-of-line packaging, and higher-level applications. NORD supports you through the entire life cycle of your drive systems with pre-sales engineering support, online tools, and a global service network. Drive systems for both vertically and horizontally networked technology with all the options for sensor incorporation and integration into the higher-level control system.