Dual Point Mini Cooler for Cooling Small Parts and Tools
EXAIR's new Mini Cooler with Dual Point Hose Kit provides a stream of 20°F (-7°C) cold air to prevent heat buildup, reduce downtime and increase productivity. It is effective on small machining operations to eliminate burning, melting and heat related breakage.
EXAIR's new Mini Cooler with Dual Point Hose Kit provides a stream of 20°F (-7°C) cold air to prevent heat buildup, reduce downtime and increase productivity. It is effective on small machining operations to eliminate burning, melting and heat related breakage. The dual point option allows the cold air outlet to be directed at two different spots when cooling larger diameter tools, cooling two separate points or opposite sides of a material or process. Single Point systems are also available.
The Mini Cooler is ideal for applications where liquid cooling cannot be used due to part contamination or cost. Tolerances, product finish and production rates can improve dramatically. In addition to preventing premature tool wear, the Mini Cooler is ideal for cooling sewing needles, blades, small tools and lens grinding. All Mini Coolers are CE compliant and operate at a quiet 76 dBA. www.exair.com/184/dualmini.htm
Featured Product
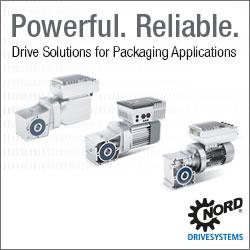