EXAIR NEW PRODUCT: Dual Point Mini Cooler for Cooling Small Parts and Tools
The Mini Cooler incorporates a vortex tube that converts an ordinary supply of compressed air into cold air at 20°F (-7°C). Flexible tubing that holds its position is provided to direct the cold airflow. An adjustable magnetic base allows easy positioning. Durable stainless-steel construction and an absence of moving parts assures maintenance free operation.
EXAIR's new Mini Cooler with Dual Point Hose Kit provides a stream of 20°F (-7°C) cold air to prevent heat buildup, reduce downtime and increase productivity. It is effective on small machining operations to eliminate burning, melting and heat related breakage. The dual point option allows the cold air outlet to be directed at two different spots when cooling larger diameter tools, cooling two separate points or opposite sides of a material or process. Single Point systems are also available.
The Mini Cooler is ideal for applications where liquid cooling cannot be used due to part contamination or cost. Tolerances, product finish and production rates can improve dramatically. In addition to preventing premature tool wear, the Mini Cooler is ideal for cooling sewing needles, blades, small tools and lens grinding. All Mini Coolers are CE complaint and operate at a quiet 76 dBA. Mini Cooler Systems with Dual Point Hose Kit, Swivel Magnetic Base and Manual Drain Filter Separator with Mounting Bracket are $345. Learn more at www.exair.com/dualmini.htm.
Featured Product
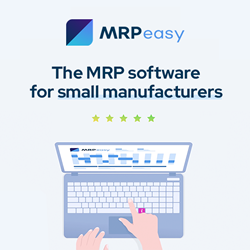