Renishaw’s Blue Laser Sets New Standard for On-Machine Tool Measurement
Building on the success of the enhanced NC4 range of tool setters launched in 2017, the NC4+ Blue is Renishaw’s latest evolution of the non-contact tool setter, delivering a step-change in tool measurement accuracy, with tool-to-tool performance proven to the most up-to-date ISO230-10 standards.
West Dundee, IL - May 29, 2019 - Renishaw, a precision engineering and manufacturing technologies company, announces the launch of its latest non-contact tool setting solution. The new NC4+ Blue system joins the many smart factory process control solutions developed by Renishaw which have been proven to help machine shops across many industries transform their production capabilities.
Featuring the industry's first blue laser technology (patent pending) and improved optics, Renishaw's NC4+ Blue systems deliver significant improvements in tool measurement accuracy, ensuring components can be machined more precisely and with reduced cycle times.
Compared to red laser sources found in conventional non-contact tool setters, blue laser technology has a shorter wavelength, resulting in improved diffraction effects and optimized laser beam geometry. This enables the measurement of very small tools, while minimizing tool-to-tool measurement errors - a critical consideration when machining with a wide range of cutting tools.
NC4+ Blue systems also use Renishaw's latest non-contact tool setting software packages, which include a new dual measurement mode with auto optimization technology. Combined, these features ensure fast and reliable tool measurement - even in wet conditions - saving users time and money.
NC4+ Blue support is now embedded into Renishaw's extensive range of graphical user interfaces, including on-machine and mobile apps such as Renishaw Set and Inspect, and GoProbe. These consistent, easy-to-use programming platforms are perfect for users who are new to probing or have little machine code knowledge, while still offering operational benefits to more experienced users.
Renishaw technologies provide the data that enables intelligent decision-making for Industry 4.0. On-machine tool measurement allows manufacturers to automate and optimize their processes and minimize quality problems and CNC machine stoppages. With the latest version of Renishaw's on-machine Reporter app, users can now view historical tool data captured by the NC4+ Blue and export the results for use in their chosen software and control systems.
About Renishaw
Renishaw is one of the world's leading engineering and scientific technology companies, with expertise in precision measurement and healthcare. The company supplies products and services used in applications as diverse as jet engine and wind turbine manufacture, through to dentistry and brain surgery. It is also a world leader in the field of additive manufacturing (also referred to as 3D printing), where it designs and makes industrial machines that "print" parts from metal powder.
The Renishaw Group currently has more than 70 offices in 35 countries, with around 4,500 employees. AM Solutions Centers are located in the USA, UK, Germany, Canada, India and China. For more information on Renishaw, visit www.renishaw.com.
Featured Product
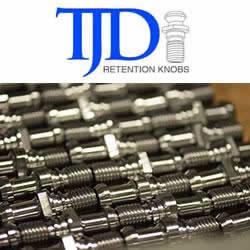