North American’s Largest Linear Friction Welder Now Operational at LIFT in Detroit
The friction welder, built and installed by the global leaders in friction welding, Manufacturing Technology, Inc. (MTI), has the largest tooling capacity of any linear friction welder in the world. This allows for the production of the largest full-scale parts available. Previously, companies interested in using a linear friction welder of this scope would have to travel to Europe.
DETROIT - The first and only linear friction welder capable of full-sized part development in North America is now fully operational and ready for project work at LIFT - Lightweight Innovations for Tomorrow, a national manufacturing innovation facility operated by the American Lightweight Materials Innovation Institute, in Detroit.
Currently, linear friction welding technology is used in aerospace to achieve light-weighting blisks and Integrally Bladed Rotors (IBR) to aircraft engines. With the machine being available for R&D, LIFT and its partners will explore how this technology could benefit other industries specifically automotive and defense.
"Our facility and our institute are already unique but having this machine in our building and available to manufacturers around the country positions us to continue leading the industry into a smart manufacturing future," said Nigel Francis, CEO and Executive Director, LIFT. "We encourage companies - both large and small - to reach out to us at LIFT to see how this machine and our other services can help them achieve their goals."
"We are thrilled to have this machine up and running in Detroit," said MTI President and CEO Dan Adams. "From aerospace, automotive, defense, rail, and mining industries, our customer have been looking for a machine that is capable of full-scale parts, and now they have it right down the road in Detroit."
In order to best serve North American customers, MTI and LIFT will have shared capacity of the machine.
The South Bend, Indiana-based MTI will run and maintain the machine at LIFT's facility in Detroit. MTI will also complete customer directed work on the machine and support any programs that LIFT has moving forward.
LF35-75 Specs
Size: 22' x 8 x 14'
Weight: 122,000 pounds (61 metric tons) - roughly the same weight as a Boeing 737
ABOUT LIFT
LIFT, operated by the American Lightweight Materials Manufacturing Innovation Institute (ALMMII), is a Detroit-based, public-private partnership committed to the development and deployment of advanced lightweight metal manufacturing technologies, and implementing education and training initiatives to better prepare the workforce today and in the future. LIFT is one of the founding institutes of Manufacturing USA and is funded in part by the Department of Defense with management through the Office of Naval Research. Visit www.lift.technology, follow on Twitter @NewsFromLIFT or on LinkedIn at https://www.linkedin.com/company/lift---lightweight-innovations-for-tomorrow/ to learn more.
About MTI
MTI has established itself as a leader in friction welding, including Rotary Friction, Linear Friction, Low Force Friction, and Friction Stir Welding technologies. In addition to contract manufacturing services, MTI has delivered machines to Boeing, GE, Rolls- Royce, Pratt and Whitney, Federal Mogul, and many of their tier one suppliers. A family owned business founded in 1926, MTI employs 185 people in their South Bend, United Kingdom, and Slovakia locations.
For more information on MTI and its family of world-class friction welding technologies, visit www.mtiwelding.com.
Featured Product
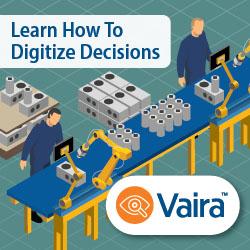