System's disruptive technology at Tecnargilla 2016
At the 25th edition of Tecnargilla, the reference international fair for the ceramics industry and construction, we will be presenting important solutions based on smart manufacturing and artificial intelligence, where innovation and advanced technology have achieved the new idea of the flexible, connected, global factory.
At the 25th edition of Tecnargilla, the reference international fair for the ceramics industry and construction, we will be presenting important solutions based on smart manufacturing and artificial intelligence, where innovation and advanced technology have achieved the new idea of the flexible, connected, global factory.
At Tecnargilla 2016, to be held at Rimini Fiera from 26 to 30 September, we will be previewing the new technological solutions and cutting edge processes prepared by the System Group, of interest to all fields of application related to the ceramics industry.
Here visitors can see System's disruptive technology:
- the new platform of PRIME software services
- the advanced technology of LAMINA for large ceramic sheets
- the latest features in digital printing
- the cutting edge solutions in storage
- the powerful vision system
- the state-of-the-art technology introduced for end-of-line and packaging
- predictive assistance and 24H efficiency of Customer Service
According to the approach of Industry 4.0 System has developed a meaningful IT tool called PRIME: "Our objective is to define a new standard in managing ceramics manufacturing, offering an authentic and effective service. With this principle of "Ceramics as a Service" clients can redesign their production processes and share them in an integrated application for using resources. We have implemented our skills and know-how to produce PRIME, a platform of software services, aimed at controlling production capacity of entire factories, optimising the quality of control processes and the standardisation of information received from systems, in order to provide management tools aimed at improving awareness and decision repeatability", says Mr Franco Stefani, Chairman of the System Group.
For some years already the company has been committed to this process of conversion, facing a period of profound change, which envisages the increasing integration of digital technologies in industrial manufacturing processes. Implementing a Converting Industry means changing existing procedures in favour of digital systems. This changeover would not be possible if we didn't place process analysis at the centre of our work, to understand and learn where we are and where we want to go. The transformation of traditional industry implies a change also on a cultural level and a series of activities focussed on the conversion from analogue to digital, the methods of collecting and using data to create value, in the processing power, connectivity and interaction between man and machine.
The role of man is raised, from maintenance engineer to controller, because we are now dealing with constant monitoring of the manufacturing process.
The System Group
The System Group is an international leader in designing and implementing manufacturing process solutions for the ceramics industry and other industrial sectors such as packaging, electronics and intralogistics, with a multidisciplinary approach embracing precision mechanics, electronics, information technology, physics and chemistry. The Group, whose headquarters is located in Fiorano Modenese in Northen Italy, is active in 25 countries via 37 subsidiaries, has a turnover of EUR 440m and over 1 700 employees worldwide.
www.system-group.it
Featured Product
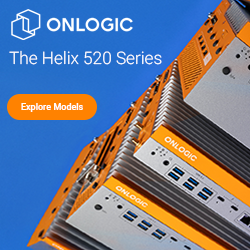