GE Plans to Invest $1.4B to Acquire Additive Manufacturing Companies Arcam and SLM; Accelerates Efforts in Important Digital Industrial Space
Expands design envelope to substantially reduce product cost Enables productive new model for services cost and delivery Lead in design and manufacture of highly valued parts Enter a fast-growing industry where GE can build a competitive position Leverages GE Store: key strengths in materials, software, and product design
BOSTON--(BUSINESS WIRE)--GE (NYSE:GE), the worlds leading digital industrial company, today announced plans to acquire two suppliers of additive manufacturing equipment, Arcam AB and SLM Solutions Group AG for $1.4 billion. Both companies will report into David Joyce, President & CEO of GE Aviation. Joyce will lead the growth of these businesses in the additive manufacturing equipment and services industry. In addition, he will lead the integration effort and the GE Store initiative to drive additive manufacturing applications across GE.
"We want all of our businesses to leverage the GE Store, promote digital differentiation, and drive productivity for GE and our customers. We are excited about the opportunity."
Tweet this
"Additive manufacturing is a key part of GEs evolution into a digital industrial company. We are creating a more productive world with our innovative world-class machines, materials and software. We are poised to not only benefit from this movement as a customer, but spearhead it as a leading supplier," said Jeff Immelt, Chairman and CEO of GE. "Additive manufacturing will drive new levels of productivity for GE, our customers, including a wide array of additive manufacturing customers, and for the industrial world."
GE expects to grow the new additive business to $1 billion by 2020 at attractive returns and also expects $3-5 billion of product cost-out across the company over the next ten years.
Arcam AB, based in Mölndal, Sweden, invented the electron beam melting machine for metal-based additive manufacturing, and also produces advanced metal powders. Its customers are in the aerospace and healthcare industries. Arcam generated $68 million in revenues in 2015 with approximately 285 employees. In addition to its Sweden site, Arcam operates AP&C, a metal powders operation in Canada, and DiSanto Technology, a medical additive manufacturing firm in Connecticut, as well as sales and application sites worldwide.
SLM Solutions Group, based in Lübeck, Germany, produces laser machines for metal-based additive manufacturing with customers in the aerospace, energy, healthcare, and automotive industries. SLM generated $74 million in revenues in 2015 with 260 employees. In addition to its operations in Germany, SLM has sales and application sites worldwide.
"Additive manufacturing fits GEs business model to lead in technologies that leverage systems integration, material science, services and digital productivity," said Joyce. "It will benefit from the GE Store and our core engineering capability."
Arcam and SLM will bolster GEs existing material science and additive manufacturing capabilities. GE has invested approximately $1.5 billion in manufacturing and additive technologies since 2010. The investment has enabled the company to develop additive applications across six GE businesses, create new services applications across the company, and earn 346 patents in powder metals alone. In addition, the additive manufacturing equipment will leverage Predix and be a part of our Brilliant Factory initiative.
"We chose these two companies for a reason," said Joyce. "We love the technologies and leadership of Arcam AB and SLM Solutions. They each bring two different, complementary additive technology modalities as individual anchors for a new GE additive equipment business to be plugged into GEs resources and experience as leading practitioners of additive manufacturing. Over time, we plan to extend the line of additive manufacturing equipment and products."
The additive effort will utilize GEs global ecosystem, but be centered in Europe. GE will maintain the headquarters locations and key operating locations of Arcam and SLM, as well as retain their management teams and employees. These locations will collaborate with the broader GE additive ecosystem including the manufacturing and materials research center in Niskayuna, New York, and the additive design and production lab in Pittsburgh, Pennsylvania. They will also complement the technologies brought on by other key acquisitions such as Morris Technologies and Rapid Quality Manufacturing.
Each acquisition is structured as a public tender offer for all of the outstanding shares of stock of each company. The closing of each public tender offer is subject to various conditions, including minimum acceptance thresholds and regulatory approvals. GE is in the process of making the necessary filings with authorities with respect to such tender offers, and, upon approval, the documents will be made publicly available.
Additive manufacturing (also called 3D printing) involves taking digital designs from computer aided design (CAD) software, and laying horizontal cross-sections to manufacture the part. Additive components are typically lighter and more durable than traditionally-manufactured parts because they require less welding and machining. Because additive parts are essentially "grown" from the ground up, they generate far less scrap material. Freed of traditional manufacturing restrictions, additive manufacturing dramatically expands the design possibilities for engineers. "Additive provides a new palette for engineers to create. Parts are also being designed in GE Power, Oil & Gas, Healthcare and across GEs services businesses," said Joyce. "We see value potential to reduce product cost and improve NPI spend. Ultimately, as we develop more productive machines, we can build additive manufacturing ‘as a service for our customers."
In July, GE Aviation introduced into airline service its first additive jet engine component - complex fuel nozzle interiors - with the LEAP jet engine. The LEAP engine is the new, best-selling engine from CFM International, a 50/50 joint company of GE and Safran Aircraft Engines of France. More than 11,000 LEAP engines are on order with up to 20 fuel nozzles in every engine, thus setting the stage for sustainably high and long-term additive production at GE Aviations Auburn, Alabama, manufacturing plant. Production will ramp up to more than 40,000 fuel nozzles using additive by 2020. GE Aviation is also using additive manufacturing to produce components in its most advanced military engines. In the general aviation world, GE is developing the Advanced Turboprop Engine (ATP) for a new Cessna aircraft with a significant portion of the entire engine produced using additive manufacturing.
"GEs aspirations in additive fits our long-term business model. We have world-class industrial businesses that leverage systems integration, material sciences, services and Predix," said Immelt. "We want all of our businesses to leverage the GE Store, promote digital differentiation, and drive productivity for GE and our customers. We are excited about the opportunity."
GE will host an investor call at 8:30AM ET to discuss these transactions. To tune in and access additional documents visit www.ge.com/investor.
About GE
GE (NYSE: GE) is the worlds Digital Industrial Company, transforming industry with software-defined machines and solutions that are connected, responsive and predictive. GE is organized around a global exchange of knowledge, the "GE Store," through which each business shares and accesses the same technology, markets, structure and intellect. Each invention further fuels innovation and application across our industrial sectors. With people, services, technology and scale, GE delivers better outcomes for customers by speaking the language of industry. www.ge.com
GE Aviation, an operating unit of GE, is a world-leading provider of jet engines, components and integrated systems for commercial and military aircraft. GE Aviation has a global service network to support these offerings. For more information, visit us at www.geaviation.com.
Featured Product
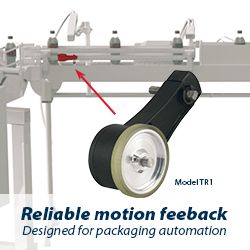