How to Gain Efficiency in Product Design & Manufacturing through Tools, Technology & Software?
Gaining efficiency in product design and manufacturing is what every manufacturer would want, in order to bring products to market faster and remain profitable.
Gaining efficiency in product design and manufacturing is what every manufacturer would want, in order to bring products to market faster and remain profitable. Thanks to the advancement in technologies in form of 3D CAD Designs & 2D CAD Drafting, which has brought a significant improvement in ways the products are being conceptualized, designed and manufactured today. The right use of tools, technology and processes like SolidWorks Product Design solutions and many more, allows even a small manufacturer to stay competitive with big market players.
Application of these accelerators can be best understood when seen from the perspective of product development cycle:
• Conceptualization
• Design
• Product Testing
• Manufacturing Plan
• Production
Conceptualization
The product conceptualization stage largely involves the efforts from CAD Design and Drafting teams that collate the information on the need to develop a new product considering factors such as customer needs, market trends, price, etc.
In a conventional development cycle, conceptualization usually consumes most of the time. This however can be reduced with the use of right technology tools that help in communicating the design intent clearly. Use of 3D modeling tools such as SolidWorks is extremely helpful to visualize the concept and perform preliminary simulations to understand the product behavior and make necessary changes without actually going for a prototype test.
A large content library, easy to use tools and parametric modeling in SolidWorks provides the designer to bring conceptual ideas to life faster.
Design
A design phase involves converting the conceptual idea to manufacturing ready Mechanical CAD Design. Preparing mechanical drafting & 2d CAD drawings requires considering several important factors such as manufacturing feasibility, existing capabilities and identification of supply vendors. Designing stage requires developing manufacturing information in terms of 2D drawings, assembly drawings and bill of materials (BOM) for downstream applications. This process again can be reduced by utilizing the capabilities of SolidWorks. Features like sheet metal design and weldments allow easy generation of bend tables, cut lists as well as manufacturing/fabrication drawings for shop floor requirements.
Product Testing
A successfully designed product is first required to be tested before being sent to actual manufacturing. The process usually involves developing a physical prototype and performing tests on it considering actual load and other environment conditions to ensure that the product will not fail prematurely. It also helps manufacturers to establish warranty and service schedules as well as provides clear picture as to how the product will actually look and behave. With the use of latest technologies and tools however, the product testing process can be shortened significantly as well as the costs associated with the expensive tests can be brought down.
Virtual testing today has become robust enough to identify the product behavior accurately without going for a physical trial. Simulation tools such as ANSYS Fluent and ANSYS Mechanical provides a great opportunity for engineers to test their designs under various loading conditions through numerical analysis.
Simulation although do not completely eliminate the need for physical tests, but help in bringing down the number of trials required. The cost and time involved as such can be dramatically reduced. The rapidly growing 3D printing technology further helps in communicating the design intent clearly. The rapid prototyping technology even has the capability to print metals and develop a product that can be used for actual applications.
Manufacturing Plan
Manufacturing without proper planning is like going up a blind alley. Proper planning of raw material procurement, manufacturing processes, resource allocation, inventory control and delivery processes is essential to ensure that the new innovative product designed is manufactured properly and delivered to the end customers on time. It is also important to communicate the product design information to shop floor clearly to avoid any lag during the actual manufacturing.
ERP tools as well PDM tools like SolidWorks Enterprise PDM helps in performing these tasks easily. It helps in keeping the information flow seamless right from concept development stage and keeps a control over the production costs.
Production
The final step is to initiate the manufacturing process as per established plan.
In actual scenarios, manufacturers often struggle to improve the efficiency despite using the right technologies and processes. This could be partly attributed to the fact that they are required to bring products as early as possible in the market at a competitive price. Addressing the need to develop new products then becomes difficult, since resources are already occupied in developing existing line of products.
Allocating resources specifically to perform the tasks of designing and developing manufacturing information is again costly and affects the product price. This is the reason why majority of the manufacturers today rely on outside design partner that takes care of developing all the required design information for new products. This helps them in focusing their resources on conceptualization, R&D and well as optimizing the manufacturing processes.
A reputed engineering services provider could help manufacturer right from concept through production at half the cost of performing everything in-house. It also takes off the burden of buying additional software licenses from manufacturers, allowing them to price the product more competitively.
Featured Product
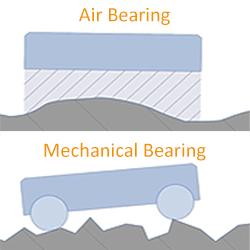