Leading OEMs Discuss How Collaborative Robots & Automation Technologies Shape Automotive Manufacturing
Future Directions For Changeover, Traceability, New Materials, Joining Techniques As Well As Data Management & Controls Architecture.
Next-Generation Collaborative Robots & Automation Technologies Automotive Manufacturing 2016
Next-Generation Collaborative Robots & Automation Technologies Automotive Manufacturing will assess the commercial benefits of implementing new robotics & automation technologies on production efficiency, cost and profitability.
The automotive manufacturing industry is no stranger to automation and robotics. However, what the industry is now witnessing is an influx of next-generation collaborative robots and automation technologies - technologies that are going to be provided at a lower cost than what the industry is used to, whilst driver safer, faster and more profitable manufacturing and maintaining a solid life-cycle.
Featuring key decision makers from Ford, General Motors, Subaru, Honda, Toyota, Nissan and more!
Key Focus Areas:
Where does automation make sense?
How to comply with global safety regulations
How to implement collaborative robots
Verifying robot safety
Error proofing & digital defect detection
How flexible are assembly lines to handle new product?
Managing changing controls architecture
Collecting and utilizing data
And more!
This two-day information packed agenda will deliver the latest OEM-led case studies to thoroughly assess the commercial application, integration and benefits of innovative collaborative robotic and automation technologies which will allow you to drive them factories quicker.
Featured Product
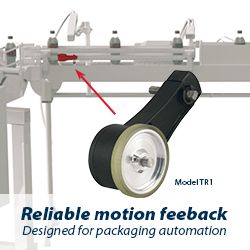
Model TR1 Tru-Trac
The Model TR1 Tru-Trac® linear measurement solution is a versatile option for tracking velocity, position, or distance over a wide variety of surfaces. An integrated encoder, measuring wheel, and spring-loaded torsion arm in one, compact unit, the Model TR1 is easy to install. The spring-loaded torsion arm offers adjustable torsion load, allowing the Model TR1 to be mounted in almost any orientation - even upside-down. The threaded shaft on the pivot axis is field reversible, providing mounting access from either side. With operating speeds up to 3000 feet per minute, a wide variety of configuration options - including multiple wheel material options - and a housing made from a durable, conductive composite material that minimizes static buildup, the Model TR1 Tru-Trac® is the ideal solution for countless applications.