Rethink Robotics' Sawyer Takes Center Stage at IPC APEX EXPO 2016
Sawyer Robot to Demonstrate In-circuit Test Solution on the Show Floor
BOSTON, March 14, 2016 /PRNewswire/ -- Rethink Robotics' high-performance Sawyer robot will take center stage at IPC APEX EXPO 2016, showing off a key printed circuit board testing application. With its compliant motion control, Sawyer has a unique ability to feel its way into precise and fragile fixtures, even when part position changes. This enables an adaptive repeatability that is unique in the robotics industry and provides unparalleled precision without the risk of damaging expensive circuit board testing equipment. Sawyer can work with any type of in-circuit tester to improve efficiency and reduce production costs.
In September of 2015, Rethink Robotics announced the availability and global deployment of Sawyer, which will be making its first appearance at an electronics industry trade show in Rethink's booth #3210 and Keysight Technologies booth #3304.
Sawyer will operate the Keysight i3070 and work as a part of an automated in-circuit test process to help further reduce the cost of testing in ICT for high mix, high volume printed circuit board production. Sawyer will insert the board under test, and then sort passing or failing boards based on the test results. Sawyer will open and close the i3070 fixture cover, just as a person would, eliminating the need to invest in additional expensive automation or changes to existing solutions.
"The worldwide demand for Sawyer has been overwhelming since we announced the robot's availability in September," said Jim Lawton, chief product and marketing officer, Rethink Robotics. "Manufacturers, particularly in the electronics industry, have been seeking a smart, collaborative solution to automate precise and important tasks like in-circuit testing and PCB handling. Sawyer is meeting those needs and transforming how factories operate."
At IPC APEX, Sawyer will demonstrate firsthand how its precision, adaptive repeatability and compliant motion control can improve current electronics manufacturing operations through increased uptime, lower scrap rates and significant process quality enhancements. Able to perform in a complex and imperfect manufacturing environment, Sawyer can quickly shift between tasks and operate like humans do, providing manufacturers with more automation options than ever before.
For more information, please visit www.rethinkrobotics.com.
About Rethink Robotics
Rethink Robotics is transforming the way manufacturing gets done, with smart, collaborative robots able to automate the 90 percent of tasks that until now, have been beyond the reach of traditional automation. Its Baxter and Sawyer robots, powered by the Intera software platform, adapt to real-world variability, can change applications quickly and perform tasks like people do. The result: manufacturers of all shapes, sizes and industries get the fast-to-deploy, easy-to-use and versatile automation solution they need to increase flexibility, lower cost and accelerate innovation.
Based in Boston, the Rethink product suite is available in Asia, Europe and North America. The company is funded by Bezos Expeditions, CRV, Highland Capital Partners, Sigma Partners, DFJ, Two Sigma Ventures, GE Ventures and Goldman Sachs. For more information about Rethink Robotics, please visit www.rethinkrobotics.com and follow us on Twitter @RethinkRobotics.
Featured Product
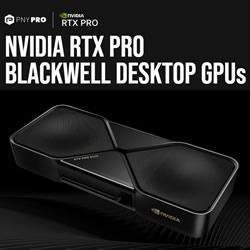