How AI and Machine Learning Are Powering the Next Generation of Pump Maintenance
Industrial machinery, particularly pumps, plays a critical role in sectors ranging from manufacturing and oil and gas to wastewater management and agriculture. Yet, maintaining these devices has traditionally been reactive and costly. Enter AI in pump maintenance and Machine learning for predictive maintenance—the dynamic duo reshaping how industries monitor, predict, and optimize their pump systems. With the growing integration of Industrial IoT for equipment health, businesses are now shifting from old-school scheduled maintenance to intelligent, data-driven approaches.
AI isn't just a buzzword anymore—it's the brain behind smarter decisions. And when it's paired with machine learning, pump maintenance gets a futuristic upgrade. Gone are the days of emergency breakdowns; instead, we now have insights, automation, and reliability.
AI isn't just a buzzword anymore—it's the brain behind smarter decisions. And when it's paired with machine learning, pump maintenance gets a futuristic upgrade. Gone are the days of emergency breakdowns; instead, we now have insights, automation, and reliability.
Smart Monitoring and Predictive Maintenance
At the heart of this transformation lies Smart pump monitoring. Sensors embedded within pumps continuously gather critical data—vibration patterns, temperature, pressure metrics, and flow rates. These data streams are fed into sophisticated algorithms that utilize Machine learning for predictive maintenance to assess the health of equipment in real time.
Using Predictive analytics in manufacturing, companies are now able to forecast when a pump is likely to fail and intervene proactively. This approach not only reduces unplanned downtime but also extends the pump's lifespan. In fact, organizations that have adopted Pump failure prediction using AI have seen a marked decline in operational costs and repair frequency.
By analyzing thousands of data points, AI systems can spot anomalies long before they turn into mechanical issues. These predictive models often include Condition-based maintenance systems, which tailor maintenance schedules based on actual equipment wear, rather than generic timelines. This shift to intelligent servicing is helping industries reallocate resources more efficiently and improve overall productivity.
The Role of AI and Machine Learning in Real-Time Decision Making
The backbone of these innovations is AI in pump maintenance, which enables machines to think and respond autonomously. For example, AI algorithms can determine whether a pump's vibrations are indicative of cavitation or bearing wear. Combined with Machine learning for predictive maintenance, the system self-improves by learning from each diagnosis, thus refining its future predictions.
Edge computing and cloud infrastructure, often built on platforms leveraging the Industrial IoT for equipment health, allow instant communication between devices. Maintenance teams receive alerts and confidence scores straight to their dashboards, streamlining workflows and empowering faster decisions.
Furthermore, integrating Smart pump monitoring systems with centralized platforms provides a 360-degree view of assets. These real-time insights allow technicians and engineers to prioritize repairs, schedule inspections smartly, and drastically reduce the number of emergency interventions.
Business Impact and Future Outlook
The convergence of data and automation is making a tangible impact. Companies employing AI in pump maintenance are reporting reductions in unplanned downtimes by up to 40%, and decreased maintenance costs by nearly 25%. These results stem directly from using Machine learning for predictive maintenance systems and embracing Predictive analytics in manufacturing strategies.
The predictive models and Condition-based maintenance systems not only save money but also optimize manpower. Teams can now shift from firefighting mechanical failures to fine-tuning performance metrics.
The future looks even more exciting. As algorithms grow more sophisticated and datasets expand, Pump failure prediction using AI will become sharper and more accurate. Eventually, maintenance won't be reactive or even predictive—it will be prescriptive. Machines will not only foresee a failure but also automatically suggest or carry out preventive steps.
Conclusion
AI and machine learning are no longer optional upgrades—they're foundational pillars for the next generation of industrial maintenance. Through AI in pump maintenance, companies gain greater insight, speed, and reliability. Coupled with Machine learning for predictive maintenance, organizations can embrace smarter workflows, reduce waste, and ensure continuous operations.
Thanks to innovations in Smart pump monitoring, Industrial IoT for equipment health, and Predictive analytics in manufacturing, pumps are getting the intelligent care they deserve. Maintenance is no longer about fixing what's broken—it's about preventing problems before they occur.
Featured Product
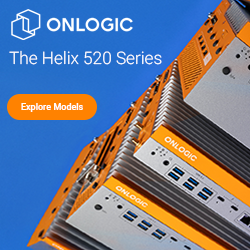