Catalyst Systems: The Future of Industrial Purification
By Dalton Frasier, Lead Application Engineer at PSB Industries
In industrial processes, purification is a critical function that ensures efficiency, regulatory compliance, and quality. Catalyst systems, often integrated with adsorption technologies, have emerged as a powerful solution to enhance purification. By accelerating chemical reactions, catalysts enable the conversion of unwanted compounds into less harmful substances, while adsorption packages physically capture and remove contaminants. The integration of these technologies is redefining industrial purification, offering streamlined operations, improved cost-effectiveness, and heightened environmental benefits.
The Shift Toward Integrated Purification Systems
Many industrial sites require a combination of purification technologies, from sacrificial purification beds and pressure swing adsorption (PSA) systems to cryogenic separators, compressors, and dryers. Historically, these technologies operated independently, leading to complex designs and increased operational burdens. Integrated catalyst and adsorption systems address these challenges by combining processes within a single framework, reducing the footprint of purification operations and enhancing overall efficiency.
One of the significant advantages of integrated purification systems is the ability to leverage existing components for multiple purposes. Heat exchangers, coolers, and blowers can be utilized for dual purposes, optimizing energy use while minimizing equipment redundancy. This approach not only simplifies design and installation but also reduces long-term maintenance costs.
Key Challenges in Industrial Purification and the Role of Automation
One of the primary challenges in industrial purification is the lack of comprehensive knowledge regarding gas compositions and reaction chemistries. Partial or incomplete data can lead to inefficiencies, as purification technologies depend on precise reaction conditions. For example, air consists of roughly 79% nitrogen and 21% oxygen. However, trace gases such as argon, carbon dioxide, and other impurities are also present. When working with catalytic and adsorptive systems, trace contaminates must also be accounted and simplistic overviews must be avoided.
Automation plays a crucial role in optimizing catalyst-adsorption systems. Industrial purification often occurs in remote or unmanned locations, making it essential for systems to operate autonomously. Automated purification skids continuously monitor conditions, self-adjusting to optimize heat cycles and reaction efficiency. These systems can detect anomalies—such as overheating or media saturation—and take corrective actions in real time, eliminating the need for constant human oversight. The result is increased reliability, enhanced safety, and reduced operational costs.
Beyond labor cost savings, automated purification systems significantly reduce the likelihood of human error in critical applications. Industrial purification often involves handling hazardous gases and complex chemical reactions that require precise control. A self-monitoring system ensures that parameters remain within optimal thresholds, mitigating the risk of unintentional emissions, hazardous leaks, or inefficient purification cycles. These built-in safeguards protect both workers and surrounding environments, leading to fewer workplace incidents and lower regulatory compliance burdens.
Additionally, automation minimizes the costs associated with employing dedicated personnel to monitor purification operations around the clock. Many industrial sites operate in challenging or hazardous environments where human presence is limited, such as offshore processing plants or high-temperature manufacturing facilities. By deploying advanced automated systems, companies can significantly cut labor costs while maintaining consistent process efficiency.
The environmental impact of automation in industrial purification is another key advantage. By continuously adjusting purification processes in real time, these systems reduce energy waste and optimize resource consumption, lowering the facility's overall carbon footprint. Automated monitoring also ensures that toxic emissions are minimized by proactively addressing issues before they escalate. This not only helps companies meet stringent environmental regulations but also supports broader corporate sustainability goals.
Furthermore, automated catalyst-adsorption systems integrate predictive maintenance capabilities, identifying potential failures before they occur. By addressing maintenance needs proactively, companies can avoid unexpected shutdowns, extend the lifespan of critical components, and reduce waste associated with system failures. These benefits translate into both economic and environmental gains, reinforcing automation as an indispensable tool in modern industrial purification.
Advantages of Integrated Purification Over Traditional Methods
Compared to traditional purification methods, integrated catalyst-adsorption systems offer several advantages. One of the most notable benefits is their compact design. Integrated systems occupy significantly less space than traditional purification setups, reducing the need for extensive infrastructure and making them easier to incorporate into existing industrial facilities. This smaller footprint translates to lower real estate costs and greater flexibility in facility layout and expansion planning.
Another advantage is the commonality in design that integrated purification systems provide. Standardizing these systems minimizes compatibility issues that can arise when sourcing components from different vendors. By ensuring that all elements of the system adhere to a unified design, companies can streamline sourcing, installation, and maintenance processes. This standardization simplifies operations, reduces the risk of integration errors, and enhances overall system reliability.
Lower operational costs are another key benefit. By combining catalytic and adsorption processes into a single unit, integrated systems optimize energy use and minimize resource consumption. This efficiency leads to reduced utility expenses, lower emissions, and extended component lifespans, all of which contribute to significant cost savings over time. The reduction in the number of separate purification components also decreases the likelihood of mechanical failures, further reducing maintenance costs and operational downtime.
Finally, integrated catalyst-adsorption systems improve overall process efficiency. The synergy between catalytic reactions and adsorption mechanisms enables the simultaneous removal of multiple impurities from industrial gases and liquids. This dual-functionality ensures higher purity levels in the final product, reduces the need for additional purification stages, and enhances system performance. By optimizing every step of the purification process, integrated systems deliver superior results while maintaining cost-effectiveness and environmental sustainability.
Sustainability and Regulatory Compliance
Environmental regulations are becoming increasingly stringent, requiring industrial facilities to minimize emissions and optimize energy use. Integrated purification systems align with these sustainability goals by reducing the number of components, lowering utility consumption, and cutting down on emissions. By capturing and recycling high-value gases, these systems prevent unnecessary waste and reduce the overall environmental footprint of industrial operations.
Moreover, the elimination of venting and flaring in purification processes ensures compliance with emission control policies. Facilities using integrated catalyst-adsorption systems benefit from reduced regulatory reporting requirements, as these systems effectively contain and process all contaminants within a closed-loop framework.
Advancements in Integrated Purification Systems
The development of integrated catalyst and adsorption solutions has been pivotal in the industrial purification sector. Recognizing the need for efficient and streamlined purification processes, numerous companies have successfully deployed integrated systems across North America, consistently delivering high-quality renewable natural gas.
Unlike generic purification solutions, customized catalyst systems are designed to meet the unique requirements of each industrial site. By understanding reaction chemistry and adsorption principles, these systems ensure maximum efficiency, minimal waste, and seamless integration into existing workflows.
As the industry continues to evolve, innovative companies are pushing the boundaries of what is possible in purification technology. Companies like PSB Industries, a specialist in the design and fabrication of systems for dehydrating and purifying gasses and liquids, are at the forefront of cutting edge innovation. PSB Industries integrated purification systems incorporate cutting-edge automation features that continuously refine system performance. By learning from past operational cycles, these systems optimize power output, prevent unnecessary downtime, and provide predictive maintenance alerts. The ability of PSB Industries' skids to self-adjust ensures minimal human intervention while maintaining peak purification efficiency. Additionally, PSB Industries is at the forefront of the industry-wide shift toward modularity. By designing purification systems with interchangeable components, PSB Industries enables clients to benefit from scalable and adaptable solutions. This modular approach ensures that new purification technologies and catalyst advancements can be seamlessly incorporated into existing systems without requiring a complete overhaul.
PSB Industries integrated purification solutions not only enhance efficiency but also drive economic and environmental benefits. By reducing the number of required components and optimizing energy consumption, PSB Industries systems lower operating costs while minimizing resource waste. Clients benefit from fewer maintenance requirements, lower failure rates, and improved long-term reliability.
Furthermore, PSB Industries purification technologies eliminate emissions by capturing every molecule within the process, ensuring full compliance with environmental regulations. By preventing gas loss and venting, PSB Industries enables industrial operators to achieve their sustainability targets while maintaining high levels of operational efficiency.
The industrial purification landscape is evolving rapidly, with modularity, automation, and efficiency driving the next generation of solutions. As industries seek more sustainable and cost-effective purification methods, the demand for integrated catalyst-adsorption systems will continue to grow. PSB Industries remains committed to advancing purification technologies, leveraging its expertise to deliver innovative and reliable solutions for clients worldwide. By prioritizing customization, automation, and environmental responsibility, PSB Industries is setting the standard for the future of industrial purification—ensuring cleaner, more efficient, and more sustainable operations across diverse industries.
Featured Product
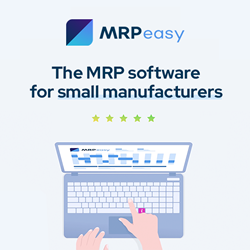