MEETING THE DEMANDS OF MINIATURISATION — MICROMETAL GROUP DRIVES INNOVATION IN PRECISION MANUFACTURING
The company’s reel-to-reel and advanced sheet PCE technologies are revolutionising how companies approach precision engineering, ensuring they stay competitive in markets that increasingly value miniaturisation and intricate designs.
(8th August 2024, Muellheim, Germany) As industries worldwide strive to meet the growing demands for smaller, more intricate components, the micrometal Group is leading the charge with its cutting-edge photo-chemical etching (PCE) processes. The company's reel-to-reel and advanced sheet PCE technologies are revolutionising how companies approach precision engineering, ensuring they stay competitive in markets that increasingly value miniaturisation and intricate designs.
Jochen Kern, Head of Sales & Marketing at micrometal Group says, "In today's fast-paced technological landscape, the trend towards miniaturisation is unmistakable. From electronics and medical devices to automotive and aerospace components, the demand for smaller, lighter, and more complex parts is accelerating. This shift is driven by the need for higher functionality within constrained spaces, improved performance, and the overall push towards more compact and efficient systems. The micrometal Group, a global leader in PCE, is at the forefront of this trend, providing solutions that meets the stringent requirements of modern manufacturing. The company's ability to produce components with fine details and high precision is unmatched, making it an essential partner for businesses aiming to innovate and excel in their respective fields."
PCE offers unparalleled advantages for precision manufacturing. Unlike traditional machining methods, PCE does not involve mechanical force, which eliminates the risk of deformation and ensures the integrity of the material. This is particularly critical for industries where accuracy and consistency are paramount.
One of the primary benefits of PCE is its ability to produce highly detailed and complex parts with exceptional repeatability. Companies in the electronics sector, for instance, can achieve the fine circuit patterns necessary for modern devices. In the medical field, manufacturers can produce micro-scale components required for advanced diagnostic and therapeutic equipment. The automotive and aerospace industries benefit from lightweight, high-strength parts that enhance performance and efficiency.
Kern continues, "The use of micrometal Group's PCE processes provides numerous advantages for businesses across various sectors, key among which is that is promotes design flexibility. Effectively, PCE allows for the creation of intricate and complex designs that would be difficult or impossible to achieve with traditional manufacturing methods. This flexibility enables engineers to innovate and develop new products that push the boundaries of what's possible. The process is also cost-effective for small to medium production runs, eliminating the need for expensive tooling and reducing material wastage, leading to significant cost savings for manufacturers."
The ability to produce parts with tolerances as tight as ±0.01 mm using PCE ensures that components meet the exact specifications required by demanding applications. This level of precision is crucial for sectors like aerospace and medical, where even the smallest deviation can have significant implications. PCE can also be applied to a wide range of metals, this versatility making it suitable for various applications across industry. Also, the quick turnaround time for prototypes allows companies to expedite their product development cycles. This agility is essential in today's competitive market, where speed to market can be a decisive factor in a product's success.
Kern concludes, "As the demand for miniaturisation and intricate components continues to grow, the micrometal Group is committed to advancing its PCE technology to meet the evolving needs of the market. The company is investing in research and development to further enhance the precision, efficiency, and versatility of its processes, ensuring that it remains a key enabler of innovation in precision manufacturing."
www.micrometal.de
Featured Product
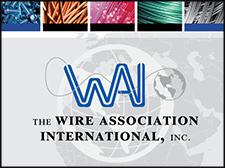