DESIGN GUIDELINES FOR MICRO MOLDING
The art of micro molding is inherently complex, laden with tasks that require consistently hitting the bullseye of extremely tight tolerances. To accomplish this feat, it's imperative to foster a collective commitment to precision across the board — from the intricate creation of micro tools to the micro molding itself, followed by rigorous validation and optimized automated assembly.
When you begin to assess the use of micro injection molding, partnering with a specialized sub-contract manufacturer becomes a strategic asset. This partnership should be strong for the entire journey of your product, from the blueprints to high-volume production, all development preferably taking place under a single roof.
The art of micro molding is inherently complex, laden with tasks that require consistently hitting the bullseye of extremely tight tolerances. To accomplish this feat, it's imperative to foster a collective commitment to precision across the board — from the intricate creation of micro tools to the micro molding itself, followed by rigorous validation and optimized automated assembly.
Beyond this complicated process, the selection of materials and the architecture of design reign supreme in micro molding. These elements are pivotal, not just as afterthoughts but as front-runners in the development process. They must be meticulously considered to sidestep the costly and time-consuming loop of redesigning a product that doesn't fit the mold — quite literally.
That's precisely why manufacturers must join forces with micro molders right at the inception of the product development process. Early collaboration is the secret sauce when crafting a manufacturing process that's not only cost-effective and swift but also nails it on the first attempt.
As we unfold the pages of the micro molding design guidebook, there are important nuggets of wisdom that can illuminate your path from the get-go. This article aims to spotlight those insights. Remember, the call to action cannot be overstated — consult with a micro molding expert at the earliest chance. It's the way to unlock tailored advice, perfectly suited to your project's unique specifications.
CONSULTANTS NOT JOB SHOPS
Welcome to the design conundrum, where original equipment manufacturers (OEMs) often see entities like Accumold as mere production houses or job shops. However, these hubs of micro molding innovation see themselves as so much more. They are the expert consultants in the realm of micro manufacturing. Be sure to choose one which is vertically integrated, however, ensuring expertise that spans from the drawing board to the final automated assembly process, its skills covering design, tooling, molding, validation, and more.
This integrative expertise flourishes best when sown early in the conceptual phase of product development. Imagine the tooling manager, at the genesis of design, offering invaluable insights into molding optimisation, or the assembly manager whose timely advice thwarts delays and cost escalations by pinpointing issues critically early in the product development process.
As you embark on a micro molding journey, keep the destination firmly in your mind's eye. Grasp the essence of your design, navigate its possibilities and limitations — for in the micro world, even the tiniest alteration can unleash a wave of complications, potentially capsizing your project.
Consider a design that features a thin wall of 0.005 inches. Here, a minute 5% dimensional shift could decide if the component materializes or vanishes into thin air. In such fine detail, material selection is not just a choice but a critical consideration that shapes the part's very existence. Design engineers, accustomed to juggling stack tolerances, must now recognize that at a micro scale, these variables fundamentally affect product viability.
When it comes to micro molding, Design for Manufacture (DfM) takes on a new importance and we should in fact look at Design for Micro Manufacturing (DfMM). Here, the conventional rules fade into obsolescence, and a new doctrine emerges for crafting often minute parts, where precision isn't just a feature, it's everything.
Engineers, armed with formidable computational prowess, can conjure ground-breaking designs that look great on screens. Yet, these designs can sometimes fall into the gap between 'ingeniously conceivable' and 'practically producible.' The devil is in the details — zoom in on the screen, tweak a fraction here, a micron there, and you might nudge a design from 'optimized' to 'unmoldable.'
Every micro molding journey is distinct — each design a unique interplay of geometry, form, and material selection, all influencing the manufacturability of a part.
MICRO MOLDING DESIGN GUIDES
In manufacturing, when you're contemplating crafting a component that tips the scales at less than a gram, you've entered the precise world of micro molding. But here's the catch, molding something a hundred of which could fit on a dime is one challenge, replicating that feat with unwavering precision batch after batch is quite another. True micro molding prowess lies in producing piece after precise piece, be it in the thousands, millions, or even billions, without missing a beat in accuracy.
Now, let's talk dimensions. At Accumold, there's a sweet spot for size. Anything up to half an inch is good. The record-holder for the tiniest part we've ever molded? An astonishing 0.031" by 0.012" by 0.015" - a marvel in microns.
Design engineers, take note. Your thin walls be a minimum of 0.004 inches in thickness. Pay keen attention to the transitions from thick to thin and strive for consistency in wall thickness. Features should ideally maintain a 6:1 aspect ratio, a figure that's intimately tied to the material chosen. When it comes to gates, they can shrink down to a minute 0.1 mm, while ejector pins can be as slender as 0.25 mm. And let's not forget shrink rates and the nuances of parting line mismatches — all crucial to the final form of your part.
With all these variables and 'rules' in play, micro molding can seem like an impossible task. Yet, before you write off an intricate design as too daunting, turn to the expertise of a veteran micro molder. Micro molding is all about pushing the frontiers of what's feasible, with each challenge from innovative manufacturers serving as a catalyst for progress. A top-tier micro molder thrives on innovation and will boldly venture into uncharted areas with you. Only when the task is truly impossible will they suggest a design pivot.
MATERIAL ISSUES
Material selection is pivotal to the success of a design to be micro molded. This is a domain where the choices are as vast and varied as the ingenuity within a designer's mind. In the micro realm, those tiny yet critical components often necessitate the use of exotic or supremely engineered thermoplastics. Imagine materials like PEEK, PEI (better known as Ultem®), carbon-filled LCP, or glass-filled nylons taking center stage. And let's not overlook the pliability of soft durometer or elastomeric resins. The direct experience with these materials, especially when micro molding, is the cornerstone of the knowledge needed to fully harness the combined strength of material and part design.
Even in macro product design, material selection sees a number of trade-offs, balancing the ideal for the part's function with the practicalities of molding it into existence. Yet, as we shrink down to the micro level, where the boundaries are tightly drawn, these trade-offs become intricate and complex and can fundamentally affect the viability of the product being made.
Typically, the quest for the right material begins with aligning the functional needs of the part with the promise held in material datasheets. However, be wary, as these datasheets are often written with larger parts in mind, with their guidance on gate size and flow properties tailored for a larger scale.
This leads to a conundrum. Manufacturers follow these datasheets as they venture into micro molding, only to be met with results that miss the mark. Such missteps can trigger a cycle of premature redesigns or, in the worst of cases, lead to the untimely end of entire projects.
At the heart of the matter is a clash between datasheets, the advice of resin suppliers, and part design requirements. This is precisely why it is of paramount importance to consult with expert micro molders at the start of the design phase. They bring to the table expertise earned through years of charting the choppy waters of material selection, and will help forecast if the chosen material will prove an ally or an adversary in the quest to bring your part from concept to creation.
CONCLUSION
Navigating the intricacies of micro molding design is a complex endeavor. The standard benchmarks for geometric intricacy and the performance criteria for materials diverge significantly from those used in creating larger scale items. Thus, engaging with adept micro molding specialists early in the design phase and during product development is crucial. These experts can provide indispensable insights into critical areas such as achieving precise tolerances, determining the best gate locations for material entry, managing issues related to flash and mismatch, offering guidance on which critical dimensions to focus on or limit, and choosing materials that will deliver the best results for the micro molded product.
www.accu-mold.com
ENDS
Paul Runyan is VP Sales & Marketing at Accumold. The company has grown to a 130,000 square foot fortified facility designed for assurance of supply, employs over 350 staff, and is a net exporter shipping all over the world every day from its Ankeny, IA, USA facility which runs 24 hours a day, 7 days a week.
Featured Product
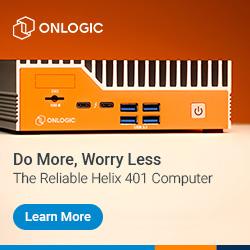