CRP Technology launches new injection molding material 100% recycled
A composite with thermoplastic matrix, PA12 based and Carbon fibers reinforced, Windform XT 2.0 IMG is the first CRP Technology's injection molding material. It is 100% recycled with no addition of virgin powder from exhausted Windform XT 2.0 for Laser Sintering
CRP Technology launches the Windform XT 2.0 IMG material and initiates a new era in the world of industrial production and sustainability.
It is 100% recycled from Windform XT 2.0 industrial 3D printing material.
Engineer Franco Cevolini, CEO and Technical Director of CRP Technology, says, "For some time we at CRP Technology have been studying an alternative and total use of those exhausted Windform powders for selective laser sintering, that fallen into disuse as they no longer meet our high quality standards."
The CRP's solution establishes that the exhausted Windform powders are not recycled with the addition of a percentage of virgin material, but they are 100% reused and properly transformed to be suitable for other technologies, which can be both traditional and additive. "In this case - continues Franco Cevolini - we regranulated the Windform XT 2.0 powder cake, and make it suitable for injection molding technology.
The test phase ended with excellent results and now we are ready to sell it to those who manufacture on large volumes basis."
Windform XT 2.0 IMG formulation features premium performances ranking from high stiffness and resistance to shock to extreme details accuracy even with thin thicknesses.
Its excellent properties makes it ideal for demanding application in a variety of industries such as automotive, transport, e-mobility, agriculture, robotics and industrial design.
With the launch on the market of Windform XT 2.0 IMG injection molding material, CRP Technology begins to offer top-of-the-range materials for different technologies, such as injection molding grade, which permit the companies to shorten the supply chain, and save time and money.
Indeed, the high quality injection molded parts in Windform XT 2.0 IMG preserve same performances of prototypes realized in AM with Windform XT 2.0
"Furthermore - Franco Cevolini adds - the companies that use our Windform XT 2.0 IMG for production, limit their carbon footprint as they are employing a 100% recycled material."
Featured Product
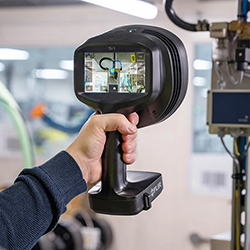
Affordable Excellence: The Go-To Tool for Finding Compressed Air Leaks
Find compressed air leaks fast with FLIR's new cutting-edge Si1-LD acoustic imaging camera. Leveraging advanced ultrasonic technology and onboard analytics, this affordable camera pinpoints leaks and quantifies incurred losses even in the nosiest environments. Upgrade your maintenance routine with the cost-effective FLIR Si1-LD - significantly reduce energy costs and increase system uptime. Get Started Today.